Получение диметилового эфира дегидратацией метанола на Аlpo4 sio2 катализаторах. Технология производства диметиловый эфир
Технология производства метанола, диметилового эфира через стадию образования синтез-газа
Сегодня исходный синтез-газ (сингаз) для синтеза метанола получают в результате конверсии (превращения) углеводородного сырья: природного газа, коксового газа, жидких углеводородов (нефти, мазута, легкого каталитического крекинга) и твердого топлива (угля, сланцев).
Реакции паровой (1), углекислотной (2) и кислородной (3) конверсии природного газа:
СН4 + Н2О = СО + 3Н2 -206 кДж/моль
СН4 + СО2 = 2СО + 2Н2 -247
СН4 + 1/2О2 = СО + 2Н2 +36
Образование метанола протекает по обратимой экзотермической реакции:
На промышленных установках синтеза метанола чаще всего работают при давлении 20–35 МПа в интервале температур 370–420 °С. Ввиду высокой экзотермичности реакции и в связи с необходимостью тонкого регулирования температуры, повышение которой отрицательно сказывается как на равновесии, так и на избирательности процесса, в реакционных аппаратах обычно предусмотрен ввод холодного синтез-газа в пространство между полками, на которых размещен катализатор — оксиды меди, с добавками оксидов хрома и цинка.
В качестве побочных превращений при синтезе метанола наблюдается образование воды, метана, диметилового эфира и высших спиртов:
Технологическая схема классического процесса получения метанола:
Рисунок 1 - Схема синтеза метанола:1 — скруббер; 2 — адсорбер; 3 — теплообменник; 4 — реактор синтеза; 5 — холодильник; 6 — сепаратор; 7, 8 — ректификационные колонны К-7 и К-8; I — синтез-газ; II — вода; III — реакционные газы; IV — метанол-сырец; V — диметиловый эфир; VI — метанол; VII — высшие спирты
Свежий синтез-газ под давлением 1–2 МПа поступает на водную отмывку от диоксида углерода в скруббер 1. После скруббера газ дожимается до нужного давления, очищается в адсорбере 2, заполненном активированным углем, от пентакарбонила железа и разделяется на два потока. Один поток подогревается в теплообменнике 3 и подается в колонну синтеза 4, другой в холодном состоянии направляется в пространство между слоями катализатора. Реакционные газы охлаждаются в холодильнике 5, при этом из них конденсируется метанол и некоторые побочные продукты: вода, диметиловый эфир, часть высших спиртов и др. В сепараторе 6 конденсат отделяется от газов, которые возвращаются в процесс.
Конденсат метанола-сырца направляется в ректификационную колонну 7 (К-7). С верха К-7 отгоняется диметиловый эфир. Кубовая жидкость К-7 поступает в колонну 8. В качестве дистиллята в К-8 отбирается метанол с примесью воды. Он направляется на очистку от воды с помощью острого пара. Из куба К-8 отводятся высшие спирты. Выход метанола составляет 85–90 %.
Синтез ДМЭ из смеси СО + Н2 включает следующие основные экзотермические реакции:
Синтез метанола:
CO + 2h3 → Ch4OH, ∆H =- 90.7 кДж/моль
Дегидратация метанола:
2Ch4OH → Ch4OCh4 + h3O, ∆H = -23.4
Реакция конверсии водяного пара:
h3O + CO → CO2 + h3, ∆H = -41.2
Прямой синтез ДМЭ из синтез-газа
2CO + 4h3 → Ch4OCh4 + Н2О, ∆H = -207.4
3CO + 3h3 → Ch4OCh4 + CO2,∆H = -244.95
Как правило ДМЭ получают из-синтез газа состава Н2:СО=1:1.
studopedia.net
Принципиальная технологическая схема — МегаЛекции
КУРСОВАЯ РАБОТА
по дисциплине: | «Теория химических процессов |
органического синтеза» | |
Ццццццццццццццццццц | |
Цвццвцна тему: | «Теоретический анализ процесса |
получения диметилового эфира» |
Цвццввацацввввццввцвццццц22ц2цвцвцвцвуувввв
Г
Выполнил: | студент 3-ЗФ-10 | А.В. Цыганов | |||
« | » | 2015 г. | |||
Руководитель: | доцент | Ю.А. Дружинина | |||
« | » | 2015 г. |
САМАРА 2015
г
Задание на контрольную работу. 3
ГыПолучение диметилового эфира по технологии «Ярсинтез». 6
Технология одностадийного синтеза диметилового эфира из природного газа. 8
2. Полный теоретический анализ изгггггбранного процесса получения ДМЭ 11
гг
ГЛитературагг. 22
Г
гЗадание на контрольную работу
Вариант №19.
1. Выполнить обзор литературы по областям технического применения диметилового эфира и масштабам его производства.
2. Выполнить обзор литературы по методам получения диметилового эфира, способам его выделения из реакционной массы и перспективам развития технологий.
3. Выполнить полный теоретический анализ избранного процесса получения диметилового эфира:
· Стехиометрия и материальные расчёты.
· Термохимический анализ для индивидуального превращения и для процесса в целом.
· Качественный и количественный термодинамический анализ для индивидуального превращения и для процесса в целом.
· Качественный и количественный кинетический анализ для индивидуального превращения и для процесса в целом.
4. Дать рекомендации по условиям осуществления избранного процесса получения и выделения диметилового эфира. Предложить принципиальные технологические схемы реализации избранного процесса
1. Обзор литературы
Диметиловый эфир (ДМЭ) СН3ОСН3, бесцветный газ с запахом, напоминающим запах хлороформа; молярная масса 46,07; температура плавления -138,5 °С, температура кипения -25,0 °С; плотность 2,091 г/л. Растворим в этаноле, диэтиловом эфире, воде. Диметиловый эфир родоначальник класса алифатических эфиров; сравнительно инертен, разлагается только при температуре красного каления, не реагирует при умеренных температурах с Na, сильными кислотами и щелочами. Обладает слабо выраженными основными свойствами. [1]
1.1. Техническое применение диметилового эфира и масштаб его производства
Диметиловый эфир сегодня широко используется в качестве распылителя для монтажной пены, технический ДМЭ применяют также как бытовой газ, например, в Китае. Не менее широко свойства диметилового эфира применяются и в строительстве – в красках для автомобилей, красках для граффити. ДМЭ участвует в производстве метилирования аминов, используется с целью получения диметилсульфата, является хорошим вспомогательным средством в борьбе с бородавками. [2]
Так же популярен на рынке диметиловый эфир высокой степени очистки (99,99%). Сферой его применения является парфюмерия, где ДМЭ используют как аэрозольный пропеллент для потребительских товаров, в частности, лака для волос.Сегодня в средствах, распыляемых из баллончиков, все еще используется пропан-бутан. Но диметиловый эфир постепенно, но уверенно вытесняет конкурента, благодаря лучшим потребительским свойствам: в отличие от пропан-бутана он не имеет запаха, но вытесняемый из баллончика продукт обладает мелкой дисперсностью, диметиловый эфир позволяет использовать вдвое большее давление – до 16 атм., против 8 атм. у пропан-бутана. Кроме того ДМЭ экологичен вследствие отсутствия токсичности, легко разлагается в тропосфере. Последнее существенно, учитывая протекающие в атмосфере Земли процессы и Киотское соглашение о сокращении выбросов парниковых газов странами с развитой экономикой. [3]
ДМЭ является наиболее перспективным моторным топливом, позволяющим обеспечить нормы, определяемых требованиями правил ЕЭК ООН №49-02 (нормы «Евро-3» и «Евро-4») нормы, без применения специальных дорогостоящих мероприятий.
В России с 1992-го, а за рубежом с 1994 г. ведутся работы по использованию ДМЭ в качестве моторного топлива для дизелей. Основными фирмами разработчиками в России является НИИ двигателей, а за рубежом Haldtr Topse A/S, Technical University of Denmark, AVL LIST Gmbh (Austria), Amoco Corp. (USA), Navistar International Co (USA).
Автомобили с двигателями, работающими на диметиловом эфире, разрабатывают KAMAZ, Volvo, Nissan и китайская компания SAIC Motor.
Объемы производства ДМЭ в мире составляет несколько десятков млн. тонн и быстро увеличиваются:
§ В КНР в 2006 году принято законодательство, регламентирующее применение ДМЭ в качестве прямого автомобильного топлива. Стратегия расширенного применения синтетических моторных топлив оформлена в виде госзаказа на 130 млрд. долл. до 2020 года.
§ В Швеции и Дании общественный транспорт полностью переведен на ДМЭ
§ Корейская компания Коgas готова построить на Дальнем Востоке завод по производству диметилэфира (ДМЭ) стоимостью $470 млн. Корея планирует закупать всю продукцию завода. Планируемая мощность завода – 300 тыс. тонн ДМЭ в год с возможностью дальнейшего увеличения. Срок окупаемости завода – 4 года. Для строительства требуется участок площадью 150 тыс. кв. м, он должен находиться рядом с газопроводом, по которому газ будет поступать на завод, и недалеко от порта для отправки ДМЭ в Корею. По оценкам компании, к 2020 году Корея будет потреблять 6,5 млн тонн диметилэфира в год, поэтому данное предприятие обеспечит лишь 5% потребности страны в этом топливе.
§ Иранская компания Zagros Petrochemical Company строит завод по производству ДМЭ мощность 800 000 тонн ДМЭ в год.
§ Рядом японских компаний совместно с Total Fina Elf SA образована компания DME Development Co. Ltd., которая разработала производственную установку с проектной мощностью 825 тыс. тонн в год.
§ Такие крупные компании, как Mitsui, Japan Oil и Mitsubis Gaz Chemistri, вскоре доведут выпуск диметилового эфира до 10 тыс. тонн в сутки.
§ В апреле 2001 года на "Новомосковском Азоте" в цехе "Синтез", где производился аммиак и метанол, была смонтирована ректификационная колонна для получения диметилового эфира из метанола-сырца. Сегодня эта установка выпускает 50 тонн ДМЭ в месяц.
§ В 2004 году вышло распоряжение правительства Москвы "Об организации работ по внедрению диметилового эфира на транспорте в качестве экологически безопасного альтернативного топлива". После этого у "Щекиноазот" появился заказчик — столица России. И пока в Москве институтом двигателей разрабатывалась топливная аппаратура на ДМЭ, на "Щекиноазот" началась реконструкция установки по производству диметилового эфира, повторный запуск которой запланирован на III квартал 2007 года. Проектная мощность установки составляет 3 тыс. тонн в год. [4]
1.2. Методы получения диметилового эфира
В настоящее время существует несколько способов получения ДМЭ, которые можно разделить на две группы – это дегидратация метанола (традиционная технология) и одностадийный синтез из синтез-газа (перспективная технология).
Получение диметилового эфира по технологии «Ярсинтез»
Технология «Ярсинтез» разработана с целью получения высокочистого ДМЭ не имеющего посторонних запахов и пригодного для использования в парфюмерной промышленности.
Получаемый ДМЭ имеет концентрацию более 99,99% масс. (без учёта воды). Содержание метанола – не более 0,0005 % масс. Содержание воды – менее 0,05% масс.
Синтез ДМЭ основан на реакции межмолекулярной дегидратации метанола в присутствии специфического катализатора (КИФ). Синтез происходит по следующей схеме:
Катализатор КИФ разработан в ОАО НИИ «Ярсинтез» и производится в промышленном масштабе.
Дегидратация метанола проводится при умеренных температурах (до 160 °С). Использование принципа «каталитической дистилляции» сочетающего стадии синтеза и разделения продуктов в одном технологическом аппарате позволяет проводить процесс при конверсиях и селективности практически равных 100%.
Принципиальная технологическая схема
Принципиальная технологическая схема получения ДМЭ представлена на рис.1.
Рис. 1 Принципиальная технологическая схема получения ДМЭ
Исходный метанол из емкости Е-1 насосом Н-2 через подогреватель Т-3, обогреваемый водяным паром, подается в нижнюю ректификационную зону реакционно-ректификационного аппарата К-10. так как перепад температур составил более 100 К, то для проведения данного процесса необходимо предусмотреть отвод тепла из зоны реакции (РРА) К-10 состоит из трех зон: двух ректификационных (нижней и верхней) и средней реакционной – заполненной катализатором.
В реакционной зоне на катализаторе протекает реакция межмолекулярной дегидратации метанола с образованием ДМЭ и воды. Верхняя ректификационная зона предназначена для отделения ДМЭ от метанола и воды, нижняя ректификационная зона предназначена для разделения метанола и воды.
Обогрев РРА осуществляется водяным паром через выносной кипятильник Т-7.
Из куба колонны К-10 выводится вода, которая сбрасывается в химзагрязненную канализацию.
Пары ДМЭ с верха колонны К-10 конденсируются в дефлегматоре Т-4, охлаждаемом оборотной водой. Конденсат после Т-4 собирается в емкости Е-5, откуда насосом Н-6 частично возвращается в колонну К-10 в качестве флегмы, а балансовый избыток – товарный ДМЭ – направляется на склад.
В зависимости от качества используемого метанола и предъявляемых требований к качеству товарного ДМЭ технологическая схема может быть дополнена стадией очитки метанола, включающей одну ил и две ректификационные колонны.
Наиболее часто встречающимися примесями в ДМЭ являются: ацетальдегид, акролеин, ацетон, метилэтилкетон, изопропанол, метилизопропилкетон, но содержание каждого из них не превышает 1 ppm.
Рекомендуемые страницы:
Воспользуйтесь поиском по сайту:
megalektsii.ru
Установки по производству диметилового эфира (ДМЭ) | Производителя
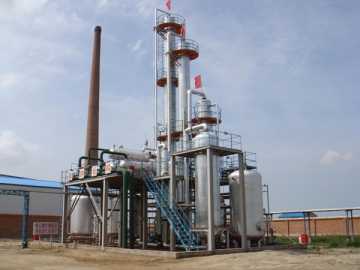
Этот продукт был снят с производства и более не предлагается.
Производство и применение диметилового эфира имеет стратегическое значение для экономики и защиты окружающей среды. Поэтому наша компания занимается разработками по производству диметилэфира, производя заводы по синтезу ДМЭ для тех клиентов, которые нуждаются в данном продукте.
Как известно, диметилэфир это одно из основных веществ органической химии, активно применяемое как в промышленности, так и в повседневной жизни. В промышленности ДМЭ в основном применяется для производства топлива, хладагентов, аэрозольных пропеллентов, полиуретановой пены и других сырьевых материалах органического синтеза. В повседневной жизни, ДМЭ может использоваться в качестве бытового топлива или как альтернативное топливо вместо дизеля или бензина для автомобилей, при этом его подготовка, хранение и разлив не представляют сложности благодаря его экологической чистоте.
Наша установка по производству диметилэфира имеет следующие характеристики: 1. В качестве сырья используется чистый или сырой метанол 2. Регенерация метанола или дистилляция диметилэфира не требуют потребления пара, потребление энергии низкое. 3. В процессе синтеза происходит незначительное количество побочных реакций; катализатор высокой активности и длительным сроком службы; низкие затраты на разделение и потребление сырьевых материалов. 4. Переработка сточных вод для вторичного использования, отсутствие сбросов сточных вод.
Если вы хотите приобрести наш современный и высокоэффективный завод по синтезу диметилового эфира, пожалуйста, сообщите нам свои особые требования и параметры окружающей среды, и мы подготовим для вас технический проект и коммерческое предложение. Когда вы присылаете нам запрос, пожалуйста, сообщите: 1. Требования по качеству (чистота) и количеству (кг/ч) диметилового эфира. 2.Цель использования ДМЭ. 3. Есть ли локальный доступный источник поставок сырьевого метанола. 4. Основные параметры местонахождения (высота над уровнем моря, атмосферное давление, температура окружающей среды, сейсмическая активность, максимально возможная скорость ветра и т.д.). 5. Доступные инженерные параметры (источник питания, требования для стартера мотора, есть ли доступный источник воды для охлаждения).
www.etwinternational.ru
способ производства диметилового эфира - патент РФ 2277528
Изобретение относится к способу получения диметилового эфира из синтез-газа и может быть использовано в нефтехимической промышленности.
Сущность: проводят каталитическую конверсию последовательно синтез-газа в реакторе(ах) синтеза метанола и продуктов синтеза в реакторе(ах) дегидратации метанола. Полученную жидкую фазу, содержащую метанол, диметиловый эфир и воду, подвергают разделению на двух ступенях дистилляции с получением на первой диметилового эфира и смеси метанол-вода, на второй метанола. Смесь метанол-вода разделяют на два потока, один из которых используют в качестве абсорбента при промывке продувочного газа, второй подают на вторую ступень дистилляции. Газовая фаза содержит непревращенный синтез-газ и диметиловый эфир. Часть газовой фазы смешивают с исходным синтез-газом, часть - продувочный газ - промывают от диметилового эфира. Абсорбент, обогащенный диметиловым эфиром, подают на первую ступень дистилляции. Метанол второй ступени дистилляции возвращают в цикл между реактором(ами) синтеза метанола и реактором(ами) дегидратации метанола. Предпочтительно абсорбент при промывке продувочного газа используют в количестве 20-100 мас.% от жидкой фазы.
Способ позволяет повысить степень превращения синтез-газа в диметиловый эфир, снизить содержание диметилового эфира в продувочном газе, упростить технологическую схему процесса. 1 з.п. ф-лы, 1 ил., 3 табл.
Рисунки к патенту РФ 2277528
Изобретение относится к области химической технологии, в частности к способу получения диметилового эфира (ДМЭ) конверсией синтез-газа. ДМЭ имеет широкое применение при синтезе различных продуктов, а также при получении топлив, в частности при производстве высокооктанового бензина. Данная технология получения ДМЭ может быть применена в различных технологических линиях, в частности на заводах, производящих метанол.
Известен способ производства диметилового эфира (ЕР 1026141, А1, 2001), в котором используется синтез-газ, состоящий из водорода и оксидов углерода.
Синтез осуществляют по циркуляционной схеме в двух последовательных реакторах. Первый загружен катализатором синтеза метанола, а второй - катализатором дегидратации метанола.
Выделение жидкой смеси, состоящей из смеси метанола, диметилового эфира и воды, проводят после конденсации в сепараторе, из которого смесь подают на ректификацию с получением диметилового эфира и метанола. Часть полученного в результате сепарации газа циркулируют на смешение с исходным синтез-газом.
Для поддержания высокого парциального давления реагирующих компонентов в циркуляционном газе часть его выводят из цикла синтеза в виде продувочного газа, содержащего диметиловый эфир.
Известный способ не позволяет добиться максимальной производительности по диметиловому эфиру, т.к. значительная часть его выводится из цикла синтеза с продувочным газом, а полученный метанол после первой ступени не превращается полностью в диметиловый эфир.
Наиболее близким к изобретению по технической сущности является способ, описанный в патенте (РФ 2144912, 2000). В данном способе каталитическую конверсию синтез-газа осуществляют путем синтеза метанола и его дегидратации с получением диметилового эфира по циркуляционной схеме в нескольких реакторах, загруженных комбинированным катализатором для получения метанола/ДМЭ. Продукты конверсии направляют в рекуперативный теплообменник, конденсатор и сепаратор с получением жидкой фазы и газовой фазы - циркуляционного газа.
Для поддержания высокого парциального давления реагирующих компонентов в циркуляционном газе часть его выводят из цикла синтеза в виде продувочного газа, содержащего диметиловый эфир.
Жидкую фазу, содержащую метанол, воду и диметиловый эфир, подвергают двухступенчатой дистилляции. На первой ступени выделяют диметиловый эфир, а на второй разделяют смесь метанол-вода. Выделенный из водно-метанольной смеси метанол используют для промывки продувочного газа в абсорбере с целью утилизации имеющегося в нем диметилового эфира. Смесь метанол-диметиловый эфир подают в отдельно стоящий дополнительный реактор - реактор дегидратации метанола, с получением дополнительного количества диметилового эфира. В результате процесса получают эфир в смеси с метанолом (до 20%) и водой (до 20%).
К недостаткам указанного способа применительно к производству диметилового эфира следует отнести:
- сложность процесса регулирования процесса очистки продувочного газа от диметилового эфира вследствие ограниченного количества получаемого в результате второй ступени дистилляции метанола, используемого в качестве абсорбента;
- необходимость использования дополнительного реактора дегидратации, что приводит к повышенным затратам;
- невозможность полного превращения метанола в диметиловый эфир вследствие дегидратации из-за обратимости реакции дегидратации;
- неэффективное использование катализатора и оборудования реактора дегидратации вследствие уменьшения степени превращения метанола за счет содержания диметилового эфира в смеси, поступающей в реактор дегидратации из абсорбера.
Технической задачей данного изобретения является создание более эффективного процесса получения диметилового эфира, в котором:
- степень превращения оксидов углерода в диметиловый эфир достигает максимального значения;
- достигается максимальный выход диметилового эфира, так как полученный в установке метанол полностью продегидратирован;
- потери диметилового эфира с продувочным газом сведены к минимуму.
- упрощена технологическая схема проведения способа.
Поставленная задача достигается описываемым способом получения диметилового эфира, включающим проведение каталитической конверсии синтез-газа в метанол и дегидратацию метанола в реакторах, охлаждение образовавшихся продуктов с получением жидкой фазы, содержащей метанол, диметиловый эфир и воду, и газовой фазы, содержащей непревращенный синтез-газ и диметиловый эфир, разделение жидкой фазы на первой ступени дистилляции с получением диметилового эфира и смеси метанол-вода, направление смеси метанол-вода на вторую ступень дистилляции с получением метанола, возвращаемого в цикл, направление одной части газовой фазы на смешение с исходным синтез-газом, другой части - продувочного газа - на промывку от диметилового эфира с использованием абсорбента и получением абсорбента, обогащенного диметиловьм эфиром, при котором проводят последовательно каталитическую конверсию синтез-газа в реакторе(ах) синтеза метанола и затем продуктов синтеза в реакторе(ах) дегидратации метанола, смесь метанол-вода первой ступени дистилляции перед направлением на вторую ступень дистилляции предварительно разделяют на два потока, один из которых используют в качестве абсорбента при промывке продувочного газа, абсорбент, обогащенный диметиловым эфиром, подают на первую ступень дистилляции и метанол второй ступени дистилляции возвращают в цикл между реактором(ами) синтеза метанола и реактором(ами) дегидратации метанола. Предпочтительно абсорбент при промывке продувочного газа используют в количестве 20-100 мас.% от жидкой фазы.
Способ получения диметилового эфира проводят следующим образом.
Синтез-газ направляют в реактор(ы) синтеза метанола. При синтезе метанола возможно использовать различные общеизвестные катализаторы синтеза метанола, такие как катализаторы на основе оксидов меди, цинка, хрома, в частности низкотемпературный медьсодержащий катализатор.
Продукты синтеза направляют в реактор(ы) дегидратации метанола. При дегидратации метанола возможно использовать различные общеизвестные катализаторы дегидратации метанола, в частности катализаторы на основе окиси алюминия, алюмосиликатов.
При проведении синтеза метанола и его дегидратации применимы различные типы реакторов, в том числе реакторы с фиксированным или псевдоожиженным слоями катализаторов, возможно использовать один реактор или систему реакторов.
Далее проводят охлаждение образовавшихся продуктов с получением жидкой и газовой фаз. Жидкую фазу, содержащую метанол, диметиловый эфир и воду, подвергают разделению на первой ступени дистилляции с получением диметилового эфира и смеси метанол-вода. Газовая фаза содержит непревращенный синтез-газ и часть полученного диметилового эфира. Часть газовой фазы направляют на смешение с исходным синтез-газом, другую часть - продувочный газ - направляют на промывку от диметилового эфира с использованием абсорбента. При этом получают абсорбент, обогащенный диметиловым эфиром. Указанный абсорбент подают на первую ступень дистилляции. Смесь метанол-вода разделяют на два потока, один из которых используют в качестве абсорбента при промывке продувочного газа, второй направляют на вторую ступень дистилляции с получением метанола.
На ступенях дистилляции возможно использовать различные схемы разделения, в том числе, например, с использованием ректификационных колонн.
Метанол второй ступени дистилляции возвращают в цикл между реактором(ами) синтеза метанола и реактором(ами) дегидратации метанола. Указанный метанол возможно направлять на реакцию дегидратации различным образом, например смешать с продуктами синтеза метанола, направляемыми в реактор (в систему реакторов) дегидратации метанола, ввести непосредственно в реактор (в систему реакторов) и другими путями.
Предпочтительно абсорбент при промывке продувочного газа используют в количестве 20-100 мас.% от жидкой фазы.
На чертеже представлена принципиальная схема проведения способа.
Поток 1 свежего синтез-газа подают в цикл синтеза, где смешивают с потоком 2 циркуляционного газа (содержащего в основном непревращенный синтез-газ и ДМЭ) и после нагрева в рекуперативном теплообменнике 3 объединенный поток 4 подают в реактор синтеза метанола 5, где на низкотемпературном медьсодержащем катализаторе происходит синтез метанола по реакциям (I, II).
В горячий поток 6, после реактора синтеза метанола 5, впрыскивают жидкий поток 7 метанола, полученного на второй ступени дистилляции. Смесь потоков 6 и 7 подают в реактор дегидратации 8, содержащий неподвижный слой катализатора на основе окиси алюминия, где происходит образование диметилового эфира по реакции (III).
Поток 9, выходящий из реактора 8, проходит рекуперативный холодильник 3, холодильник-конденсатор 10, где происходит отделение жидкой фазы, поток 11, от газовой фазы - сухого циркуляционного газа, поток 12. После отвода продувочного газа, поток 13, оставшийся поток 2 направляют на смешение с потоком 1 свежего синтез-газа. Продувочный газ, поток 13, направляют на очистку от диметилового эфира в абсорбере 14, в котором в качестве абсорбента используют смесь метанол-вода, поток 15. Расход абсорбента регулируют таким образом, чтобы обеспечить максимальную очистку продувочного газа от диметилового эфира. Обогащенный ДМЭ абсорбент - смесь метанол - вода - ДМЭ, поток 16, после очистки продувочного газа смешивают с конденсатом, поток 11. Затем смесь направляют на первую ступень дистилляции 17. Полученный при перегонке диметиловый эфир, поток 18, с чистотой более 99%, является целевым продуктом. Кубовый остаток перегонки (смесь метанол-вода) разделяют на два потока. Первый из них, поток 15, используют в качестве абсорбента для очистки продувочного газа, а второй, поток 19, направляют на вторую стадию дистилляции 20, в результате которой получают обезвоженный метанол, поток 7. Этот поток возвращают на переработку в цикл получения ДМЭ после реактора синтеза метанола 5 перед дегидратацией метанола до диметилового эфира в реакторе 8. Продувочный газ отводят по линии 21.
Обеспечение глубокой очистки продувочного газа от остатков диметилового эфира достигают варьированием количества рециркулируемой смеси метанол-вода.
Изобретение иллюстрируется следующими примерами.
Результаты, полученные в примерах, приведены ниже в таблицах. Номера потоков в таблицах соответствуют позициям, приведенным на чертеже.
Пример 1 (таблица 1).
Свежий синтез-газ (поток 1) под давлением 8,5 МПа в количестве 5902 нм3/час подают в цикл синтеза, где смешивают с потоком циркуляционного газа (поток 2), содержащим, в том числе, 2,5% ДМЭ и 0,07% метанола, в количестве 14991 нм3/час. После нагрева в рекуперативном теплообменнике 3 до температуры 190-210°С эту смесь (поток 4) подают в реактор синтеза метанола 5, где на низкотемпературном катализаторе медьсодержащем катализаторе происходит синтез метанола. Температура на выходе из реактора синтеза составляет 265-280°С, содержание метанола 3,66% и 1,92% ДМЭ. В горячий циркуляционный газ (поток 6) после реактора синтеза метанола впрыскивают 270 кг/час метанола-ректификата (поток 7), полученного после второй ступени дистилляции. С температурой 260-265°С эту смесь подают в реактор дегидратации 8, где происходит образование диметилового эфира. Концентрация ДМЭ на выходе из реактора увеличивается до 3,68%, а метанола снижается до 1,03%. После рекуперативного холодильника полученную смесь (поток 9) охлаждают в холодильнике - конденсаторе 10. Далее проводят отделение жидкой фазы из циркуляционного газа. Жидкая фаза - конденсат (поток 11) в количестве 1404 кг/час, содержит ДМЭ 38,34 мас.%, метанола 19,23 мас.% и воды 40,81 мас.%. Сухой циркуляционный газ (поток 12) с содержанием метанола 0,07% и 2,5% ДМЭ разделяют на два потока - 2 и 13. Поток 2 направляют на смешение со свежим синтез-газом. Поток 13, как продувочный газ, в количестве 3506 нм3/час направляют на очистку от диметилового эфира в абсорбере 14, в котором в качестве абсорбента используют смесь метанол-вода (поток 15) с расходом 571 кг/час, содержанием ДМЭ 0,84 мас.%, метанола 31,75 мас.% и воды 67,41 мас.%. Абсорбент на выходе (поток 16) в количестве 742 кг/час содержит ДМЭ 23,70 мас.%, метанола 24,43 мас.% и воды 51,87 мас.%, при этом абсорбент поглощает 171 кг/час ДМЭ. Это количество соответствует степени очистки продувочного газа от диметилового эфира 95%. Продувочный газ после абсорбера (поток 21) в количестве 3422 нм3 /час содержит 0,13% ДМЭ. Поток 16 смешивают с конденсатом (поток 11) и подают на первую ступень дистилляции 17, где происходит отгон диметилового эфира. Полученный диметиловый эфир (поток 18) в количестве 683 кг/час с чистотой 99.51% является целевым продуктом. Кубовый остаток - смесь метанол-вода, разделяют на два потока. Первый из них, поток 15, в количестве 571 кг/час используют в качестве абсорбента для очистки продувочного газа, а второй, поток 19, в количестве 850 кг/час направляют на вторую ступень дистилляции 20. Поток 15 составляет от потока 11 40,7%. Обезвоженный метанол-ректификат (поток 7) в количестве 270 кг/час после второй ступени дистилляции возвращают на переработку в цикл синтеза.
Пример 2 (таблица 2).
Пример 2 отличается от примера 1 параметрами стадий абсорбции и дистилляции. Продувочный газ (поток 13), в количестве 3506 нм3/час направляют на очистку от диметилового эфира в абсорбере 14, в котором в качестве абсорбента используют смесь метанол-вода (поток 15) с расходом 287 кг/час, содержанием ДМЭ 0,84 мас.%, метанола 31,75 мас.% и воды 67,41 мас.%. Абсорбент на выходе (поток 16) в количестве 422 кг/час содержит ДМЭ 32,56 мас.%, метанола 21,60 мас.% и воды 45,85 мас.%, при этом абсорбент поглощает 135 кг/час ДМЭ. Это количество соответствует степени очистки продувочного газа от диметилового эфира 75%. Продувочный газ после абсорбера (поток 21) в количестве 3440 кг/час содержит 0,64% ДМЭ. Поток 10 смешивают с конденсатом (поток 11) и подают на первую ступень дистилляции 17, где происходит отгон диметилового эфира. Полученный отгонкой диметиловый эфир (поток 18) в количестве 648 кг/час с чистотой 99,50% является целевым продуктом. Кубовый остаток - смесь метанол-вода разделяют на два потока. Первый из них, поток 15, в количестве 287 кг/час используют в качестве абсорбента для очистки продувочного газа, а второй, поток 19, в количестве 850 кг/час направляют на вторую ступень дистилляции 20. Поток 15 составляет от потока 11 20,4%. Обезвоженный метанол (поток 7) в количестве 270 кг/час после второй ступени дистилляции возвращают на переработку в цикл процесса.
Пример 3 (таблица 3).
Пример 3 отличается от примера 1 и 2 параметрами стадий абсорбции и дистилляции.
Продувочный газ (поток 13), в количестве 3506 нм3 /час направляют на очистку от диметилового эфира в абсорбере 14, в котором в качестве абсорбента используют смесь метанол-вода (поток 15) с расходом 1198 кг/час, с содержанием ДМЭ 0,84 мас.%, метанола 31,75 мас.% и воды 67,41 мас.%. Абсорбент на выходе (поток 16) в количестве 1399 кг/час содержит ДМЭ 13,52 мас.%, метанола 27,19 мас.% и воды 57,74 мас.%, при этом абсорбент поглощает 179,1 кг/час ДМЭ. Это количество соответствует степени очистки продувочного газа от диметилового эфира 99,5%. Продувочный газ после абсорбера (поток 21) в количестве 3419 кг/час содержит 0,01% ДМЭ. Поток 10 смешивают с конденсатом (поток 11) и подают на первую ступень дистилляции 17. Полученный при перегонке диметиловый эфир (поток 18) в количестве 689 кг/час с чистотой 99,52% является целевым продуктом. Кубовый остаток перегонки - смесь метанол-вода, разделяют на два потока. Первый из них, поток 15, в количестве 287 кг/час используют в качестве абсорбента для очистки продувочного газа, а второй, поток 19, в количестве 850 кг/час направляют на вторую ступень дистилляции 20. Поток 15 составляет от потока 11 85,3%. Обезвоженный метанол (поток 7) в количестве 270 кг/час после второй ступени дистилляции возвращают на переработку в цикл процесса.
Как видно из примеров и данных таблиц в описываемом процессе:
- диметиловый эфир является одним целевым продуктом с концентрацией 99,51 мас.%, метанол - как побочный продукт полностью отсутствует, за счет чего повышается выход целевого продукта;
- потери диметилового эфира с продувочным газом сведены к минимуму, содержание диметилового эфира в продувочном газе достигает 0,01 об.%, что также приводит к повышению выхода целевого продукта;
- способ проводят по более простой технологической схеме.
ПРИМЕР 1
ТАБЛИЦА 1 | ||||||||||||||
№ потока | 1 | 2 | 3 | 4 | 5 | 6 | 7 | 8 | 9 | 10 | 11 | 12 | 13 | 14 |
Состав, об.% | мас.% | мас.% | мас.% | мас.% | мас.% | об.% | ||||||||
Диоксид углерода | 13.42 | 11.87 | 12.31 | 11.32 | 11.21 | 11.87 | 11.87 | 1.50 | 0.49 | 12.16 | ||||
Оксид углерода | 8.68 | 4.98 | 6.02 | 4.72 | 4.68 | 4.97 | 4.97 | 0.02 | 0.00 | 5.10 | ||||
Водород | 59.84 | 50.17 | 59.90 | 47.63 | 47.18 | 50.17 | 50.17 | 0.01 | 0.00 | 51.39 | ||||
Азот | 8.00 | 13.46 | 11.920 | 12.78 | 12.65 | 13.46 | 13.46 | 0.04 | 0.00 | 13.78 | ||||
Аргон | 2.27 | 3.82 | 3.38 | 3.62 | 3.59 | 3.82 | 3.82 | 0.03 | 0.00 | 3.91 | ||||
Метан | 7.79 | 13.09 | 11.59 | 12.43 | 12.31 | 13-09 | 13.09 | 0.05 | 0.00 | 13.41 | ||||
Вода | 0.00 | 0.06 | 0.04 | 1.92 | 3.68 | 0.06 | 0.06 | 40.81 | 51.87 | 67.41 | 67.41 | 0.00 | 0.06 | |
Метанол | 0.00 | 0.07 | 0.05 | 3.66 | 100.00 | 1.03 | 0.07 | 0.07 | 19.23 | 24.43 | 31.75 | 31.75 | 0.00 | 0.07 |
Диметиловый эфир | 0.00 | 2.50 | 1.79 | 1.92 | 3.68 | 2.50 | 2.50 | 38.34 | 23.70 | 0.84 | 0.84 | 99.51 | 0.13 | |
Расход | 5902 нм3/ч | 14991 нм3/ч | 20893 нм 3/ч | 19487 нм3/ч | 270 кг/ч | 19674 нм 3/ч | 18497 нм3/ч | 3506 нм3/ч | 1404 кг/ч | 742 кг/ч | 571 кг/ч | 850 кг/ч | 683 кг/ч | 3422 нм3/ч |
Давление, МПа | 8.5 | 8.5 | 8.4 | 8.4 | 8.4 | 8.4 | 8.3 | 8.3 | 1.2 | 1.2 | 1.2 | 1.2 | 1.2 | 1.2 |
ПРИМЕР 2
ТАБЛИЦА 2 | ||||||||||||||
№ потока | 1 | 2 | 3 | 4 | 5 | 6 | 7 | 8 | 9 | 10 | 11 | 12 | 13 | 14 |
Состав, об.% | мас.% | мас.% | мас.% | мас.% | мас.% | об.% | ||||||||
Диоксид углерода | 13.42 | 11.87 | 12.31 | 11.32 | 11.21 | 11.87 | 11.87 | 1.50 | 0.50 | 12.09 | ||||
Оксид углерода | 8.68 | 4.98 | 6.02 | 4.72 | 4.68 | 4.97 | 4.97 | 0.02 | 0.00 | 5.07 | ||||
Водород | 59.84 | 50.17 | 59.90 | 47.63 | 47.18 | 50.17 | 50.17 | 0.01 | 0.00 | 51.13 | ||||
Азот | 8.00 | 13.46 | 11.920 | 12.78 | 12.65 | 13.46 | 13.46 | 0.04 | 0.00 | 13.71 | ||||
Аргон | 2.27 | 3.82 | 3.38 | 3.62 | 3.59 | 3.82 | 3.82 | 0.03 | 0.00 | 3.89 | ||||
Метан | 7.79 | 13.09 | 11.59 | 12.43 | 12.31 | 13.09 | 13.09 | 0.05 | 0.00 | 13.34 | ||||
Вода | 0.00 | 0.06 | 0.04 | 1.92 | 3.68 | 0.06 | 0.06 | 40.81 | 45.85 | 67.41 | 67.41 | 0.00 | 0.06 | |
Метанол | 0.00 | 0.07 | 0.05 | 3.66 | 100.00 | 1.03 | 0.07 | 0.07 | 19.23 | 21.60 | 31.75 | 31.75 | 0.00 | 0.07 |
Диметиловый эфир | 0.00 | 2.50 | 1.79 | 1.92 | 3.68 | 2.50 | 2.50 | 38.34 | 32.56 | 0.84 | 0.84 | 99.5 | 0.64 | |
Расход | 5902 нм3/ч | 14991 нм3/ч | 20893 нм 3/ч | 19487 нм3/ч | 270 кг/ч | 19674 нм 3/ч | 18497 нм3/ч | 3506 нм3/ч | 1404 кг/ч | 422 кг/ч | 287 кг/ч | 850 кг/ч | 648 кг/ч | 3440 нм3/ч |
Давление, МПа | 8.5 | 8.5 | 8.4 | 8.4 | 8.4 | 8.4 | 8.3 | 8.3 | 1.2 | 1.2 | 1.2 | 1.2 | 1.2 | 1.2 |
ПРИМЕР 3
ТАБЛИЦА 3 | ||||||||||||||
№ потока | 1 | 2 | 3 | 4 | 5 | 6 | 7 | 8 | 9 | 10 | 11 | 12 | 13 | 14 |
Состав, об.% | мас.% | мас.% | мас.% | мас.% | мас.% | об.% | ||||||||
Диоксид углерода | 13.42 | 11.87 | 12.31 | 11.32 | 11.21 | 11.87 | 11.87 | 1.50 | 0.48 | 12.17 | ||||
Оксид углерода | 8.68 | 4.98 | 6.02 | 4.72 | 4.68 | 4.97 | 4.97 | 0.02 | 0.00 | 5.10 | ||||
Водород | 59.84 | 50.17 | 59.90 | 47.63 | 47.18 | 50.17 | 50.17 | 0.01 | 0.00 | 51.45 | ||||
Азот | 8.00 | 13.46 | 11.920 | 12.78 | 12.65 | 13.46 | 13.46 | 0.04 | 0.00 | 13.80 | ||||
Аргон | 2.27 | 3.82 | 3.38 | 3.62 | 3.59 | 3.82 | 3.82 | 0.03 | 0.00 | 3.91 | ||||
Метан | 7.79 | 13.09 | 11.59 | 12.43 | 12.31 | 13.09 | 13.09 | 0.05 | 0.00 | 13.42 | ||||
Вода | 0.00 | 0.06 | 0.04 | 1.92 | 3.68 | 0.06 | 0.06 | 40.81 | 57.74 | 67.41 | 67.41 | 0.00 | 0.06 | |
Метанол | 0.00 | 0.07 | 0.05 | 3.66 | 100.00 | 1.03 | 0.07 | 0.07 | 19.23 | 27.19 | 31.75 | 31.75 | 0.00 | 0.07 |
Диметиловый эфир | 0.00 | 2.50 | 1.79 | 1.92 | 3.68 | 2.50 | 2.50 | 38.34 | 13.52 | 0.84 | 0.84 | 99.52 | 0.01 | |
Расход | 5902 нм3/ч | 14991 нм3/ч | 20893 нм 3/ч | 19487 нм3/ч | 270 кг/ч | 19674 нм 3/ч | 18497 нм3/ч | 3506 нм3/ч | 1404 кг/ч | 1399 кг/ч | 1198 кг/ч | 850 кг/ч | 689 кг/ч | 3419 нм3/ч |
Давление, МПа | 8.5 | 8.5 | 8.4 | 8.4 | 8.4 | 8.4 | 8.3 | 8.3 | 1.2 | 1.2 | 1.2 | 1.2 | 1.2 | 1.2 |
ФОРМУЛА ИЗОБРЕТЕНИЯ
1. Способ производства диметилового эфира, включающий проведение каталитической конверсии синтез-газа в метанол и дегидратацию метанола в реакторах, охлаждение образовавшихся продуктов с получением жидкой фазы, содержащей метанол, диметиловый эфир и воду, и газовой фазы, содержащей непревращенный синтез-газ и диметиловый эфир, разделение жидкой фазы на первой ступени дистилляции с получением диметилового эфира и смеси метанол-вода, направление смеси метанол-вода на вторую ступень дистилляции с получением метанола, возвращаемого в цикл, направление одной части газовой фазы на смешение с исходным синтез-газом, другой части - продувочного газа на промывку от диметилового эфира с использованием абсорбента и получением абсорбента, обогащенного диметиловым эфиром, отличающийся тем, что проводят последовательно каталитическую конверсию синтез-газа в реакторе(ах) синтеза метанола и затем продуктов синтеза в реакторе(ах) дегидратации метанола, смесь метанол-вода первой ступени дистилляции перед направлением на вторую ступень дистилляции предварительно разделяют на два потока, один из которых используют в качестве абсорбента при промывке продувочного газа, абсорбент, обогащенный диметиловым эфиром, подают на первую ступень дистилляции, и метанол второй ступени дистилляции возвращают в цикл между реактором(ами) синтеза метанола и реактором(ами) дегидратации метанола.
2. Способ по п.1, отличающийся тем, что абсорбент при промывке продувочного газа используют в количестве 20-100 мас.% от жидкой фазы.
www.freepatent.ru
Переработка попутного нефтяного газа в диметиловый эфир
biofilter.narod.ru
Способ производства диметилового эфира | Банк патентов
Изобретение относится к области химической технологии, в частности к способу получения диметилового эфира (ДМЭ) конверсией синтез-газа. ДМЭ имеет широкое применение при синтезе различных продуктов, а также при получении топлив, в частности при производстве высокооктанового бензина. Данная технология получения ДМЭ может быть применена в различных технологических линиях, в частности на заводах, производящих метанол.
Известен способ производства диметилового эфира (ЕР 1026141, А1, 2001), в котором используется синтез-газ, состоящий из водорода и оксидов углерода.
Синтез осуществляют по циркуляционной схеме в двух последовательных реакторах. Первый загружен катализатором синтеза метанола, а второй - катализатором дегидратации метанола.
Выделение жидкой смеси, состоящей из смеси метанола, диметилового эфира и воды, проводят после конденсации в сепараторе, из которого смесь подают на ректификацию с получением диметилового эфира и метанола. Часть полученного в результате сепарации газа циркулируют на смешение с исходным синтез-газом.
Для поддержания высокого парциального давления реагирующих компонентов в циркуляционном газе часть его выводят из цикла синтеза в виде продувочного газа, содержащего диметиловый эфир.
Известный способ не позволяет добиться максимальной производительности по диметиловому эфиру, т.к. значительная часть его выводится из цикла синтеза с продувочным газом, а полученный метанол после первой ступени не превращается полностью в диметиловый эфир.
Наиболее близким к изобретению по технической сущности является способ, описанный в патенте (РФ 2144912, 2000). В данном способе каталитическую конверсию синтез-газа осуществляют путем синтеза метанола и его дегидратации с получением диметилового эфира по циркуляционной схеме в нескольких реакторах, загруженных комбинированным катализатором для получения метанола/ДМЭ. Продукты конверсии направляют в рекуперативный теплообменник, конденсатор и сепаратор с получением жидкой фазы и газовой фазы - циркуляционного газа.
Для поддержания высокого парциального давления реагирующих компонентов в циркуляционном газе часть его выводят из цикла синтеза в виде продувочного газа, содержащего диметиловый эфир.
Жидкую фазу, содержащую метанол, воду и диметиловый эфир, подвергают двухступенчатой дистилляции. На первой ступени выделяют диметиловый эфир, а на второй разделяют смесь метанол-вода. Выделенный из водно-метанольной смеси метанол используют для промывки продувочного газа в абсорбере с целью утилизации имеющегося в нем диметилового эфира. Смесь метанол-диметиловый эфир подают в отдельно стоящий дополнительный реактор - реактор дегидратации метанола, с получением дополнительного количества диметилового эфира. В результате процесса получают эфир в смеси с метанолом (до 20%) и водой (до 20%).
К недостаткам указанного способа применительно к производству диметилового эфира следует отнести:
- сложность процесса регулирования процесса очистки продувочного газа от диметилового эфира вследствие ограниченного количества получаемого в результате второй ступени дистилляции метанола, используемого в качестве абсорбента;
- необходимость использования дополнительного реактора дегидратации, что приводит к повышенным затратам;
- невозможность полного превращения метанола в диметиловый эфир вследствие дегидратации из-за обратимости реакции дегидратации;
- неэффективное использование катализатора и оборудования реактора дегидратации вследствие уменьшения степени превращения метанола за счет содержания диметилового эфира в смеси, поступающей в реактор дегидратации из абсорбера.
Технической задачей данного изобретения является создание более эффективного процесса получения диметилового эфира, в котором:
- степень превращения оксидов углерода в диметиловый эфир достигает максимального значения;
- достигается максимальный выход диметилового эфира, так как полученный в установке метанол полностью продегидратирован;
- потери диметилового эфира с продувочным газом сведены к минимуму.
- упрощена технологическая схема проведения способа.
Поставленная задача достигается описываемым способом получения диметилового эфира, включающим проведение каталитической конверсии синтез-газа в метанол и дегидратацию метанола в реакторах, охлаждение образовавшихся продуктов с получением жидкой фазы, содержащей метанол, диметиловый эфир и воду, и газовой фазы, содержащей непревращенный синтез-газ и диметиловый эфир, разделение жидкой фазы на первой ступени дистилляции с получением диметилового эфира и смеси метанол-вода, направление смеси метанол-вода на вторую ступень дистилляции с получением метанола, возвращаемого в цикл, направление одной части газовой фазы на смешение с исходным синтез-газом, другой части - продувочного газа - на промывку от диметилового эфира с использованием абсорбента и получением абсорбента, обогащенного диметиловьм эфиром, при котором проводят последовательно каталитическую конверсию синтез-газа в реакторе(ах) синтеза метанола и затем продуктов синтеза в реакторе(ах) дегидратации метанола, смесь метанол-вода первой ступени дистилляции перед направлением на вторую ступень дистилляции предварительно разделяют на два потока, один из которых используют в качестве абсорбента при промывке продувочного газа, абсорбент, обогащенный диметиловым эфиром, подают на первую ступень дистилляции и метанол второй ступени дистилляции возвращают в цикл между реактором(ами) синтеза метанола и реактором(ами) дегидратации метанола. Предпочтительно абсорбент при промывке продувочного газа используют в количестве 20-100 мас.% от жидкой фазы.
Способ получения диметилового эфира проводят следующим образом.
Синтез-газ направляют в реактор(ы) синтеза метанола. При синтезе метанола возможно использовать различные общеизвестные катализаторы синтеза метанола, такие как катализаторы на основе оксидов меди, цинка, хрома, в частности низкотемпературный медьсодержащий катализатор.
Продукты синтеза направляют в реактор(ы) дегидратации метанола. При дегидратации метанола возможно использовать различные общеизвестные катализаторы дегидратации метанола, в частности катализаторы на основе окиси алюминия, алюмосиликатов.
При проведении синтеза метанола и его дегидратации применимы различные типы реакторов, в том числе реакторы с фиксированным или псевдоожиженным слоями катализаторов, возможно использовать один реактор или систему реакторов.
Далее проводят охлаждение образовавшихся продуктов с получением жидкой и газовой фаз. Жидкую фазу, содержащую метанол, диметиловый эфир и воду, подвергают разделению на первой ступени дистилляции с получением диметилового эфира и смеси метанол-вода. Газовая фаза содержит непревращенный синтез-газ и часть полученного диметилового эфира. Часть газовой фазы направляют на смешение с исходным синтез-газом, другую часть - продувочный газ - направляют на промывку от диметилового эфира с использованием абсорбента. При этом получают абсорбент, обогащенный диметиловым эфиром. Указанный абсорбент подают на первую ступень дистилляции. Смесь метанол-вода разделяют на два потока, один из которых используют в качестве абсорбента при промывке продувочного газа, второй направляют на вторую ступень дистилляции с получением метанола.
На ступенях дистилляции возможно использовать различные схемы разделения, в том числе, например, с использованием ректификационных колонн.
Метанол второй ступени дистилляции возвращают в цикл между реактором(ами) синтеза метанола и реактором(ами) дегидратации метанола. Указанный метанол возможно направлять на реакцию дегидратации различным образом, например смешать с продуктами синтеза метанола, направляемыми в реактор (в систему реакторов) дегидратации метанола, ввести непосредственно в реактор (в систему реакторов) и другими путями.
Предпочтительно абсорбент при промывке продувочного газа используют в количестве 20-100 мас.% от жидкой фазы.
На чертеже представлена принципиальная схема проведения способа.
Поток 1 свежего синтез-газа подают в цикл синтеза, где смешивают с потоком 2 циркуляционного газа (содержащего в основном непревращенный синтез-газ и ДМЭ) и после нагрева в рекуперативном теплообменнике 3 объединенный поток 4 подают в реактор синтеза метанола 5, где на низкотемпературном медьсодержащем катализаторе происходит синтез метанола по реакциям (I, II).
В горячий поток 6, после реактора синтеза метанола 5, впрыскивают жидкий поток 7 метанола, полученного на второй ступени дистилляции. Смесь потоков 6 и 7 подают в реактор дегидратации 8, содержащий неподвижный слой катализатора на основе окиси алюминия, где происходит образование диметилового эфира по реакции (III).
Поток 9, выходящий из реактора 8, проходит рекуперативный холодильник 3, холодильник-конденсатор 10, где происходит отделение жидкой фазы, поток 11, от газовой фазы - сухого циркуляционного газа, поток 12. После отвода продувочного газа, поток 13, оставшийся поток 2 направляют на смешение с потоком 1 свежего синтез-газа. Продувочный газ, поток 13, направляют на очистку от диметилового эфира в абсорбере 14, в котором в качестве абсорбента используют смесь метанол-вода, поток 15. Расход абсорбента регулируют таким образом, чтобы обеспечить максимальную очистку продувочного газа от диметилового эфира. Обогащенный ДМЭ абсорбент - смесь метанол - вода - ДМЭ, поток 16, после очистки продувочного газа смешивают с конденсатом, поток 11. Затем смесь направляют на первую ступень дистилляции 17. Полученный при перегонке диметиловый эфир, поток 18, с чистотой более 99%, является целевым продуктом. Кубовый остаток перегонки (смесь метанол-вода) разделяют на два потока. Первый из них, поток 15, используют в качестве абсорбента для очистки продувочного газа, а второй, поток 19, направляют на вторую стадию дистилляции 20, в результате которой получают обезвоженный метанол, поток 7. Этот поток возвращают на переработку в цикл получения ДМЭ после реактора синтеза метанола 5 перед дегидратацией метанола до диметилового эфира в реакторе 8. Продувочный газ отводят по линии 21.
Обеспечение глубокой очистки продувочного газа от остатков диметилового эфира достигают варьированием количества рециркулируемой смеси метанол-вода.
Изобретение иллюстрируется следующими примерами.
Результаты, полученные в примерах, приведены ниже в таблицах. Номера потоков в таблицах соответствуют позициям, приведенным на чертеже.
Пример 1 (таблица 1).
Свежий синтез-газ (поток 1) под давлением 8,5 МПа в количестве 5902 нм3/час подают в цикл синтеза, где смешивают с потоком циркуляционного газа (поток 2), содержащим, в том числе, 2,5% ДМЭ и 0,07% метанола, в количестве 14991 нм3/час. После нагрева в рекуперативном теплообменнике 3 до температуры 190-210°С эту смесь (поток 4) подают в реактор синтеза метанола 5, где на низкотемпературном катализаторе медьсодержащем катализаторе происходит синтез метанола. Температура на выходе из реактора синтеза составляет 265-280°С, содержание метанола 3,66% и 1,92% ДМЭ. В горячий циркуляционный газ (поток 6) после реактора синтеза метанола впрыскивают 270 кг/час метанола-ректификата (поток 7), полученного после второй ступени дистилляции. С температурой 260-265°С эту смесь подают в реактор дегидратации 8, где происходит образование диметилового эфира. Концентрация ДМЭ на выходе из реактора увеличивается до 3,68%, а метанола снижается до 1,03%. После рекуперативного холодильника полученную смесь (поток 9) охлаждают в холодильнике - конденсаторе 10. Далее проводят отделение жидкой фазы из циркуляционного газа. Жидкая фаза - конденсат (поток 11) в количестве 1404 кг/час, содержит ДМЭ 38,34 мас.%, метанола 19,23 мас.% и воды 40,81 мас.%. Сухой циркуляционный газ (поток 12) с содержанием метанола 0,07% и 2,5% ДМЭ разделяют на два потока - 2 и 13. Поток 2 направляют на смешение со свежим синтез-газом. Поток 13, как продувочный газ, в количестве 3506 нм3/час направляют на очистку от диметилового эфира в абсорбере 14, в котором в качестве абсорбента используют смесь метанол-вода (поток 15) с расходом 571 кг/час, содержанием ДМЭ 0,84 мас.%, метанола 31,75 мас.% и воды 67,41 мас.%. Абсорбент на выходе (поток 16) в количестве 742 кг/час содержит ДМЭ 23,70 мас.%, метанола 24,43 мас.% и воды 51,87 мас.%, при этом абсорбент поглощает 171 кг/час ДМЭ. Это количество соответствует степени очистки продувочного газа от диметилового эфира 95%. Продувочный газ после абсорбера (поток 21) в количестве 3422 нм3 /час содержит 0,13% ДМЭ. Поток 16 смешивают с конденсатом (поток 11) и подают на первую ступень дистилляции 17, где происходит отгон диметилового эфира. Полученный диметиловый эфир (поток 18) в количестве 683 кг/час с чистотой 99.51% является целевым продуктом. Кубовый остаток - смесь метанол-вода, разделяют на два потока. Первый из них, поток 15, в количестве 571 кг/час используют в качестве абсорбента для очистки продувочного газа, а второй, поток 19, в количестве 850 кг/час направляют на вторую ступень дистилляции 20. Поток 15 составляет от потока 11 40,7%. Обезвоженный метанол-ректификат (поток 7) в количестве 270 кг/час после второй ступени дистилляции возвращают на переработку в цикл синтеза.
Пример 2 (таблица 2).
Пример 2 отличается от примера 1 параметрами стадий абсорбции и дистилляции. Продувочный газ (поток 13), в количестве 3506 нм3/час направляют на очистку от диметилового эфира в абсорбере 14, в котором в качестве абсорбента используют смесь метанол-вода (поток 15) с расходом 287 кг/час, содержанием ДМЭ 0,84 мас.%, метанола 31,75 мас.% и воды 67,41 мас.%. Абсорбент на выходе (поток 16) в количестве 422 кг/час содержит ДМЭ 32,56 мас.%, метанола 21,60 мас.% и воды 45,85 мас.%, при этом абсорбент поглощает 135 кг/час ДМЭ. Это количество соответствует степени очистки продувочного газа от диметилового эфира 75%. Продувочный газ после абсорбера (поток 21) в количестве 3440 кг/час содержит 0,64% ДМЭ. Поток 10 смешивают с конденсатом (поток 11) и подают на первую ступень дистилляции 17, где происходит отгон диметилового эфира. Полученный отгонкой диметиловый эфир (поток 18) в количестве 648 кг/час с чистотой 99,50% является целевым продуктом. Кубовый остаток - смесь метанол-вода разделяют на два потока. Первый из них, поток 15, в количестве 287 кг/час используют в качестве абсорбента для очистки продувочного газа, а второй, поток 19, в количестве 850 кг/час направляют на вторую ступень дистилляции 20. Поток 15 составляет от потока 11 20,4%. Обезвоженный метанол (поток 7) в количестве 270 кг/час после второй ступени дистилляции возвращают на переработку в цикл процесса.
Пример 3 (таблица 3).
Пример 3 отличается от примера 1 и 2 параметрами стадий абсорбции и дистилляции.
Продувочный газ (поток 13), в количестве 3506 нм3 /час направляют на очистку от диметилового эфира в абсорбере 14, в котором в качестве абсорбента используют смесь метанол-вода (поток 15) с расходом 1198 кг/час, с содержанием ДМЭ 0,84 мас.%, метанола 31,75 мас.% и воды 67,41 мас.%. Абсорбент на выходе (поток 16) в количестве 1399 кг/час содержит ДМЭ 13,52 мас.%, метанола 27,19 мас.% и воды 57,74 мас.%, при этом абсорбент поглощает 179,1 кг/час ДМЭ. Это количество соответствует степени очистки продувочного газа от диметилового эфира 99,5%. Продувочный газ после абсорбера (поток 21) в количестве 3419 кг/час содержит 0,01% ДМЭ. Поток 10 смешивают с конденсатом (поток 11) и подают на первую ступень дистилляции 17. Полученный при перегонке диметиловый эфир (поток 18) в количестве 689 кг/час с чистотой 99,52% является целевым продуктом. Кубовый остаток перегонки - смесь метанол-вода, разделяют на два потока. Первый из них, поток 15, в количестве 287 кг/час используют в качестве абсорбента для очистки продувочного газа, а второй, поток 19, в количестве 850 кг/час направляют на вторую ступень дистилляции 20. Поток 15 составляет от потока 11 85,3%. Обезвоженный метанол (поток 7) в количестве 270 кг/час после второй ступени дистилляции возвращают на переработку в цикл процесса.
Как видно из примеров и данных таблиц в описываемом процессе:
- диметиловый эфир является одним целевым продуктом с концентрацией 99,51 мас.%, метанол - как побочный продукт полностью отсутствует, за счет чего повышается выход целевого продукта;
- потери диметилового эфира с продувочным газом сведены к минимуму, содержание диметилового эфира в продувочном газе достигает 0,01 об.%, что также приводит к повышению выхода целевого продукта;
- способ проводят по более простой технологической схеме.
ПРИМЕР 1
ТАБЛИЦА 1 | ||||||||||||||
№ потока | 1 | 2 | 3 | 4 | 5 | 6 | 7 | 8 | 9 | 10 | 11 | 12 | 13 | 14 |
Состав, об.% | мас.% | мас.% | мас.% | мас.% | мас.% | об.% | ||||||||
Диоксид углерода | 13.42 | 11.87 | 12.31 | 11.32 | 11.21 | 11.87 | 11.87 | 1.50 | 0.49 | 12.16 | ||||
Оксид углерода | 8.68 | 4.98 | 6.02 | 4.72 | 4.68 | 4.97 | 4.97 | 0.02 | 0.00 | 5.10 | ||||
Водород | 59.84 | 50.17 | 59.90 | 47.63 | 47.18 | 50.17 | 50.17 | 0.01 | 0.00 | 51.39 | ||||
Азот | 8.00 | 13.46 | 11.920 | 12.78 | 12.65 | 13.46 | 13.46 | 0.04 | 0.00 | 13.78 | ||||
Аргон | 2.27 | 3.82 | 3.38 | 3.62 | 3.59 | 3.82 | 3.82 | 0.03 | 0.00 | 3.91 | ||||
Метан | 7.79 | 13.09 | 11.59 | 12.43 | 12.31 | 13-09 | 13.09 | 0.05 | 0.00 | 13.41 | ||||
Вода | 0.00 | 0.06 | 0.04 | 1.92 | 3.68 | 0.06 | 0.06 | 40.81 | 51.87 | 67.41 | 67.41 | 0.00 | 0.06 | |
Метанол | 0.00 | 0.07 | 0.05 | 3.66 | 100.00 | 1.03 | 0.07 | 0.07 | 19.23 | 24.43 | 31.75 | 31.75 | 0.00 | 0.07 |
Диметиловый эфир | 0.00 | 2.50 | 1.79 | 1.92 | 3.68 | 2.50 | 2.50 | 38.34 | 23.70 | 0.84 | 0.84 | 99.51 | 0.13 | |
Расход | 5902 нм3/ч | 14991 нм3/ч | 20893 нм 3/ч | 19487 нм3/ч | 270 кг/ч | 19674 нм 3/ч | 18497 нм3/ч | 3506 нм3/ч | 1404 кг/ч | 742 кг/ч | 571 кг/ч | 850 кг/ч | 683 кг/ч | 3422 нм3/ч |
Давление, МПа | 8.5 | 8.5 | 8.4 | 8.4 | 8.4 | 8.4 | 8.3 | 8.3 | 1.2 | 1.2 | 1.2 | 1.2 | 1.2 | 1.2 |
ПРИМЕР 2
ТАБЛИЦА 2 | ||||||||||||||
№ потока | 1 | 2 | 3 | 4 | 5 | 6 | 7 | 8 | 9 | 10 | 11 | 12 | 13 | 14 |
Состав, об.% | мас.% | мас.% | мас.% | мас.% | мас.% | об.% | ||||||||
Диоксид углерода | 13.42 | 11.87 | 12.31 | 11.32 | 11.21 | 11.87 | 11.87 | 1.50 | 0.50 | 12.09 | ||||
Оксид углерода | 8.68 | 4.98 | 6.02 | 4.72 | 4.68 | 4.97 | 4.97 | 0.02 | 0.00 | 5.07 | ||||
Водород | 59.84 | 50.17 | 59.90 | 47.63 | 47.18 | 50.17 | 50.17 | 0.01 | 0.00 | 51.13 | ||||
Азот | 8.00 | 13.46 | 11.920 | 12.78 | 12.65 | 13.46 | 13.46 | 0.04 | 0.00 | 13.71 | ||||
Аргон | 2.27 | 3.82 | 3.38 | 3.62 | 3.59 | 3.82 | 3.82 | 0.03 | 0.00 | 3.89 | ||||
Метан | 7.79 | 13.09 | 11.59 | 12.43 | 12.31 | 13.09 | 13.09 | 0.05 | 0.00 | 13.34 | ||||
Вода | 0.00 | 0.06 | 0.04 | 1.92 | 3.68 | 0.06 | 0.06 | 40.81 | 45.85 | 67.41 | 67.41 | 0.00 | 0.06 | |
Метанол | 0.00 | 0.07 | 0.05 | 3.66 | 100.00 | 1.03 | 0.07 | 0.07 | 19.23 | 21.60 | 31.75 | 31.75 | 0.00 | 0.07 |
Диметиловый эфир | 0.00 | 2.50 | 1.79 | 1.92 | 3.68 | 2.50 | 2.50 | 38.34 | 32.56 | 0.84 | 0.84 | 99.5 | 0.64 | |
Расход | 5902 нм3/ч | 14991 нм3/ч | 20893 нм 3/ч | 19487 нм3/ч | 270 кг/ч | 19674 нм 3/ч | 18497 нм3/ч | 3506 нм3/ч | 1404 кг/ч | 422 кг/ч | 287 кг/ч | 850 кг/ч | 648 кг/ч | 3440 нм3/ч |
Давление, МПа | 8.5 | 8.5 | 8.4 | 8.4 | 8.4 | 8.4 | 8.3 | 8.3 | 1.2 | 1.2 | 1.2 | 1.2 | 1.2 | 1.2 |
ПРИМЕР 3
ТАБЛИЦА 3 | ||||||||||||||
№ потока | 1 | 2 | 3 | 4 | 5 | 6 | 7 | 8 | 9 | 10 | 11 | 12 | 13 | 14 |
Состав, об.% | мас.% | мас.% | мас.% | мас.% | мас.% | об.% | ||||||||
Диоксид углерода | 13.42 | 11.87 | 12.31 | 11.32 | 11.21 | 11.87 | 11.87 | 1.50 | 0.48 | 12.17 | ||||
Оксид углерода | 8.68 | 4.98 | 6.02 | 4.72 | 4.68 | 4.97 | 4.97 | 0.02 | 0.00 | 5.10 | ||||
Водород | 59.84 | 50.17 | 59.90 | 47.63 | 47.18 | 50.17 | 50.17 | 0.01 | 0.00 | 51.45 | ||||
Азот | 8.00 | 13.46 | 11.920 | 12.78 | 12.65 | 13.46 | 13.46 | 0.04 | 0.00 | 13.80 | ||||
Аргон | 2.27 | 3.82 | 3.38 | 3.62 | 3.59 | 3.82 | 3.82 | 0.03 | 0.00 | 3.91 | ||||
Метан | 7.79 | 13.09 | 11.59 | 12.43 | 12.31 | 13.09 | 13.09 | 0.05 | 0.00 | 13.42 | ||||
Вода | 0.00 | 0.06 | 0.04 | 1.92 | 3.68 | 0.06 | 0.06 | 40.81 | 57.74 | 67.41 | 67.41 | 0.00 | 0.06 | |
Метанол | 0.00 | 0.07 | 0.05 | 3.66 | 100.00 | 1.03 | 0.07 | 0.07 | 19.23 | 27.19 | 31.75 | 31.75 | 0.00 | 0.07 |
Диметиловый эфир | 0.00 | 2.50 | 1.79 | 1.92 | 3.68 | 2.50 | 2.50 | 38.34 | 13.52 | 0.84 | 0.84 | 99.52 | 0.01 | |
Расход | 5902 нм3/ч | 14991 нм3/ч | 20893 нм 3/ч | 19487 нм3/ч | 270 кг/ч | 19674 нм 3/ч | 18497 нм3/ч | 3506 нм3/ч | 1404 кг/ч | 1399 кг/ч | 1198 кг/ч | 850 кг/ч | 689 кг/ч | 3419 нм3/ч |
Давление, МПа | 8.5 | 8.5 | 8.4 | 8.4 | 8.4 | 8.4 | 8.3 | 8.3 | 1.2 | 1.2 | 1.2 | 1.2 | 1.2 | 1.2 |
bankpatentov.ru
Получение диметилового эфира дегидратацией метанола на Аlpo4 sio2 катализаторах
0,15 | - | 0,17 | - | 3-5 | |
Температура воспламенения, 0С | 235 | 650 | 504 | 470 | 250 |
Предел взрываемости, % | 3,4-17 | 5-15 | 2,1- 9,4 | 5,5-26 | 0,6-7,5 |
Цетановое число | 55-60 | 0 | 5 | 5 | 40-55 |
Низшая теплота сгорания, кДж/кг | 28 900 | 50 300 | 46 500 | 21 100 | 42 500 |
* плотность СПГ определена при температуре минус 161,50С |
Таким образом, химическое превращение природного газа в ДМЭ непосредственно на газовом месторождении позволяет значительно сэкономить средства, связанные с транспортированием углеводородного топлива от мест добычи, и получить продукт, являющийся перспективным дизельным топливом (альтернативным нефтяному).
Из возможных направлений использования ДМЭ (топливо для бытовых нужд, моторное топливо, сырье для теплоэлектростанций) для европейского рынка наиболее вероятен транспорт. Несмотря на то, что в настоящее время ДМЭ используется исключительно в качестве пропелента и ежегодное мировое потребление не превышает 150 тыс. тонн, ожидается, что в ближайшие годы сформируется рынок ДМЭ как моторного топлива.
10.3. Выбор технологии переработки
В основе существующего процесса промышленного синтеза ДМЭ лежит экзотермическая реакция дегидратации метанола. Это относительно простой процесс, который целесообразен только для установок небольшой мощности и капиталоемкости. Синтез проводят при давлении около 1,0 МПа, температуре 290-4000С в адиабатическом реакторе в присутствии катализатора (оксид алюминия). Конверсия метанола за один проход составляет около 80%.
Рекомендовать данную технологию для крупнотоннажного производства ДМЭ нельзя, так как себестоимость ДМЭ, образующегося при дегидратации метанола, существенно (в 2 раза) выше, чем метанола. Так как получение ДМЭ в любом случае проходит стадию образования метанола, то все предлагаемые к реализации технологии синтеза ДМЭ из природного газа являются, в общем случае, развитием метанольного производства и включают в себя ряд общих стадий: стадию риформинга природного газа в синтез-газ (смесь водорода и окиси углерода), на которую приходится до 70% общего объема затрат на процесс; стадию каталитического превращения синтез-газа в смесь метанола и ДМЭ, на которую приходится 20-25% капитальных затрат на процесс; стадию разделения метанола и ДМЭ.
В Российских академических институтах (ИНХС им. А.В.Топчиева, ИОХ им. А.Д.Зелинского) также проводятся работы по созданию технологии производства ДМЭ из природного газа. Исследования носят преимущественно академический характер, направлены на создание новых катализаторов получения ДМЭ из синтез-газа. Исследования, проводимые в ГНЦ НИФХИ им Л.Я.Карпова, направлены на разработку технологической схемы и конструктивного оформления процесса.
По-нашему мнению, ключевой стадией процесса химической конверсии природного газа в ДМЭ является стадия превращения метана в синтез-газ. Поэтому основной акцент при разработке технологий следует сделать на получение более дешевого синтез-газа по сравнению с существующими способами.
Технология "Тандем" (двухступенчатая парокислородная конверсия природного газа с трубчатым реактором), разработанная ГИАП (Россия) и фирмой Linde (Германия), в настоящее время является одной из самых эффективных технологий получения метанола из природного газа. В промышленном масштабе она реализована на ПО "Азот" (Беларусь). Производительность установки по перерабатываемому газу - 130 млн м3/год. По данной технологии проектируется установка производства метанола на АО "Нитроферт" (Эстония) производительностью по природному газу 400 млн м3/год.
Процесс "Тандем" имеет ряд очевидных преимуществ по сравнению с паровой конверсией природного газа в шахтном реакторе.
К ним следует отнести автотермичность процесса и замкнутый энергетический цикл, минимальный удельный расход природного газа на 1 тонну вырабатываемого продукта (расходный коэффициент получения 1 тонны метанола из природного газа составляет 85% от потенциально возможного, т.е. только 15% или 150 м3 природного газа из взятых 1 000 м3 потребляется для обеспечения энергетики процесса "Тандем"). Кроме того, обеспечивается низкий уровень выбросов вредных веществ (NOx, SO2, CO) в атмосферу.
В отличие от западных технологий конверсию синтез-газа в ДМЭ можно осуществлять без стадии ректификации. Общая рециркуляционная схема, характерная для синтеза метанола, остается без изменений. Реактор, как и в синтезе метанола, состоит из адиабатических слоев (полок), но отличается способом размещения катализатора дегидратации метанола и используемым циркулирующим агентом для охлаждения образующихся продуктов.
Конденсация состоит из трех ступеней: конденсатора влаги, конденсатора метанола и конденсатора ДМЭ. Предлагаемый способ позволяет получить ДМЭ без примесей метанола.
Процесс "Тандем" обеспечивает необходимый для последующей стадии состав синтез-газа при давлении в реакторе 30-90 атм. Это определяет благоприятные условия для создания агрегата производства ДМЭ без компрессора синтез-газа, что, безусловно, значительно повысит его технико-экономические показатели.
Предварительный анализ процесса показывает возможность создания агрегата производительностью 500-800 тыс. тонн в год по ДМЭ, оборудование которого имеет промышленные аналоги и может быть создано в однолинейном исполнении транспортабельных габаритов.
В настоящее время ВНИИГАЗ совместно с ГНЦ НИФХИ, ИВТАН, РГУНГ им. И.М.Губкина разрабатывает ТЭО по созданию завода производства ДМЭ единичной мощности 500 тыс. тонн в год. Работа проводится в рамках научно-технической подпрограммы "Прогрессивные технологии комплексного освоения топливно-энергетических ресурсов недр России" федеральной целевой научно-технической программы "Исследования и разработки по приоритетным направлениям развития науки и техники гражданского назначения" Министерства науки и технологий Российской Федерации. [27]
11. Производство ДМЭ из угля
Речь идет, прежде всего, о применении на угледобывающих предприятиях технологий и установок по переработке угля в особо ценные виды высокоэффективных и экологически чистых синтетических моторных топлив, таких например, как диметиловый эфир (ДМЭ). Тем более что именно сжиженный природный газ и синтетические моторные топлива, как известно, являются одним из приоритетов уже в только что принятой Энергетической стратегии России.
Применение этого высококачественного дизельного и энергетического топлива, альтернативного нефтяному, является настолько перспективным, что не только многие зарубежные компании и фирмы (BP, Marubeni, NKK, Air Products & Chemicals Inc.), но и ряд российских предприятий ведут работы по промышленному освоению этого весьма привлекательного в коммерческом отношении направления. Это обусловлено тем, что ДМЭ, как моторное топливо, в частности, имеет более высокое цетановое число (55-60 в отличие от 40-55 для нефтяного дизельного топлива), а при его сгорании в выхлопных газах практически отсутствуют сажа и оксиды азота.
Независимо от технологии промышленного синтеза ДМЭ получение этого топлива проходит стадию образования метанола путем риформинга природного газа в синтез-газ (смесь водорода и окиси углерода), на которую приходится почти две трети общих энергетических затрат на процесс. Последующие же стадии каталитического превращения синтез-газа в смесь метанола и ДМЭ, а затем их разделения требуют значительно более низких энергозатрат, но являются достаточно капиталоемкими.
Сегодня некоторые зарубежные фирмы (NKK, Air Products & Chemicals Inc.) уже имеют опытно-промышленные технологии и установки производства ДМЭ из угля в шламовых реакторах, работающих при соотношениях h3/CO от 0,7 до 1. По данным корпорации NKK (Япония) установка по производству 2500 т/сут ДМЭ будет перерабатывать 4000 т угля в сутки. Синтез ДМЭ осуществляется при температуре 250-2700С и давлении 30-70 атм., процент конверсии за один цикл прохода метанола составляет 55-60 и на выходе реактора ДМЭ составляет 95-99%. Минимальная стоимость такой установки составляет 365 млн долл. США.
Ориентировочный расчет экономической эффективности работы такой установки по специально разработанной Excel-программе, выполненный при следующих исходных данных:
- производительность установки по ДМЭ, млн. т/год - 0,83
- стоимость 1т у.т., $/т – 50
- стоимость установки, млн $ - 365
- дополнительные капиталовложения, $/т ДМЭ - 18,5
- прочие переменные издержки, $/т ДМЭ - 5,5
- транспортные расходы по доставке ДМЭ, $/т ДМЭ - 2,5
- длительность эксплуатации установки, год - 20подтверждает достаточно высокую экономическую эффективность осуществления такого проекта.
При расчетах определялись стандартные показатели, характеризующие эффективность проекта: чистый дисконтированный доход NPV = 359,85 млн $; внутренняя норма доходности IRR = 26%; индекс доходности PI = 0,95 и tд = 6 лет.
Как видим, при принятых исходных данных не все критерии эффективности, строго говоря, свидетельствуют в пользу реализации данного проекта. Так, индекс доходности проекта является несколько меньшим единицы, хотя другие показатели, такие как IRR и дисконтированный срок окупаемости являются достаточно высокими.
Ситуация в этом смысле изменяется существенным образом при изменении таких параметров, как ставка дисконтирования, цена исходного топлива, ставка налогообложения, стоимость реализации (поставки) одной тонны ДМЭ и пр. В частности, только при снижении ставки дисконтирования с 12 до 10 % индекс доходности проекта уже становится равным 1,21, а дисконтированный срок окупаемости снижается с 6 до 5 лет. Если же принять стоимость исходного топлива на уровне 30 $/т, что находится даже несколько выше существующих сегодня цен на уголь, то рассматриваемый проект становится “эффективным” по всем показателям и при ставке дисконтирования 12%.
Еще большие возможности для перспективного развития угольной промышленности открываются на путях комплексного энергохимического использования (сжигания) каменного угля, при котором в значительной мере снижаются и выбросы в окружающую среду инертного газа СО2, являющегося, как известно (в силу парникового эффекта), своего рода барьером на пути развития угольной энергетики.[28]
продолжениеcoolreferat.com
- Прямой эфир жена кержакова
- Жена кержакова прямой эфир
- Прямой эфир facebook android
- Генгам лион прямой эфир
- Перевод эфира в биткоин
- Реакция переэтерификации сложных эфиров
- Прямой эфир одесса дерибасовская
- Диэтиловый эфир малеиновой кислоты
- Прямой эфир анна лисовская
- Реал мю прямой эфир
- Прямой эфир мю реал