Способ получения диметилового эфира высокой чистоты. Диметиловый эфир получение
способ получения диметилового эфира - патент РФ 2469017
Настоящее изобретение относится к способу получения продукта диметилового эфира каталитической конверсией синтез-газа в диметиловый эфир, предусматривающий контакт потока синтез-газа, содержащего двуокись углерода, на стадии синтеза диметилового эфира в одном или более реакторах и с одним или более катализаторами, активными в образовании метанола и дегидратации метанола до диметилового эфира, с получением смеси продукта, содержащей компоненты диметиловый эфир, метанол, двуокись углерода и непрореагировавший синтез-газ, промывание смеси продукта, содержащей двуокись углерода и непрореагировавший синтез-газ, в газопромывочной зоне жидким растворителем, обогащенным карбонатом калия или амином, тем самым селективно абсорбируя двуокись углерода в жидкий растворитель. Полученную таким образом обработанную смесь продукта подвергают стадии дистилляции для отделения метанола и воды от потока диметилового эфира и непрореагировавшего синтез-газа с пониженным содержанием двуокиси углерода и отделение непрореагировавшего синтез-газа от продукта диметилового эфира. Способ позволяет улучшить выход процесса и конечную очистку полученного диметилового эфира. 5 з.п. ф-лы, 1 пр., 3 табл., 1 ил.
Рисунки к патенту РФ 2469017
Данное изобретение относится к способу получения диметилового эфира из синтез-газа. В частности, данное изобретение относится к улучшенному способу синтеза диметилового эфира с применением химической промывки потока сырья со стадии синтеза эфира для удаления двуокиси углерода из сырья для улучшения выхода процесса и конечной очистки полученного диметилового эфира.
Предшествующий уровень техники
Способ в соответствии с данным изобретением относится к очистке диметилового эфира, полученного из оксидов углерода и водородсодержащего синтез-газа.
Превращение синтез-газа в диметиловый эфир осуществляют в одном или более реакторах, в которых синтез-газ каталитически превращают в метанол, как показано в уравнении (1), и диметиловый эфир, как показано в уравнении (2). Также происходит реакция смещения, показанная в уравнении (3).
Максимальной конверсии синтез-газа достигают при получении диметилового эфира при стехиометрическом соотношении водорода и окиси углерода, равном единице. При соотношении выше или ниже единицы получают меньшее количество диметилового эфира. При максимальной конверсии (Н2/СО 1) вся реакции проходит по существу в соответствии с уравнением (4):
Двуокись углерода растворима в диметиловом эфире, и для получения продукта диметилового эфира с требуемой чистотой необходимо удалять образовавшуюся двуокись углерода. Кроме того, при удалении двуокиси углерода состав непрореагировавшего синтез-газа, который рециркулируют в реактор синтеза дметилового эфира, приближен к тому, который имеет синтез-газ, применяемый для получения диметилового эфира, что также является дополнительным преимуществом. Удаление двуокиси углерода из диметилового эфира после реактора синтеза может стать очень дорогим.
Известны три основных метода удаления двуокиси углерода. В первом методе диметиловый эфир синтезируют согласно реакциям (1) - (3) выше. Смешанный выходящий поток, содержащий непрореагировавший синтез-газ вместе с присутствующей двуокисью углерода, затем отделяют от продукта диметилового эфира, который также содержит некоторое количество непрореагировавшего метанола. Отделенный поток синтез-газа и двуокиси углерода рециркулируют в технологический поток синтез-газа, входящий в реактор. Этот метод удобным образом может применяться для обогащенного водородом синтез-газа, имеющего, например, соотношение водорода и окиси углерода выше 5.
Во втором известном методе смешанный выходящий поток, содержащий непрореагировавший синтез-газ вместе с двуокисью углерода, отделяют из продукта диметилового эфира. Однако двуокись углерода затем далее отделяют от синтез-газа. Это может быть осуществлено промыванием этого потока, например, подходящим соединением амина, таким как метилдиэтаноламин, МДЭА. Поток синтез-газа, который не содержит двуокись углерода, затем рециркулируют в технологический поток синтез-газа, входящий в реактор. Полученная двуокись углерода может применяться в других процессах, например, для получения синтез-газа из природного газа автотермическим реформингом двуокиси углерода.
В третьем известном методе только синтез-газ отделяют от продукта диметилового эфира и двуокиси углерода. Продукт диметилового эфира, таким образом, содержит и метанол и двуокись углерода. Отделенный синтез-газ рециркулируют в технологический поток синтез-газа, входящий в реактор.
В данной области техники известны различные растворители для удаления двуокиси углерода из смесей с синтез-газом. Выбор растворителя зависит от способности растворять диметиловый эфир и двуокись углерода, и идеальный растворитель должен обладать высокой растворяющей способностью для двуокиси углерода и низкой летучестью.
В патенте США № 5908963 описан способ получения диметилового эфира из синтез-газа, в котором синтез-газ отделяют от продукта диметилового эфира и рециркулируют в технологический поток синтез-газа, входящий в цикл синтеза диметилового эфира. Присутствие избытка метанола в продукте диметилового эфира является объектом внимания в описанном способе, и удаление двуокиси углерода не рассматривается.
В патенте США № 6458856 описан одностадийный каталитический способ конверсии для получения диметилового эфира. После каталитической конверсии синтез-газа в диметиловый эфир выходящий из реактора поток разделяют на паровую смесь, содержащую диметиловый эфир, двуокись углерода и непрореагировавший синтез-газ. Паровую смесь промывают с применением газопромывающего растворителя для удаления диметилового эфира и двуокиси углерода от непрореагировавшего синтез-газа. Газопромывающий растворитель содержит смесь диметилового эфира и метанола. Непрореагировавший синтез-газ рециркулируют в диметиловый реактор.
В этой ссылке также описан известный уровень техники, в котором применяют газо-промывающие растворители, такие как метанол, вода, смеси метанола/воды, диметиловый эфир или этанол.
Диметиловый эфир является хорошим растворителем для двуокиси углерода, но является очень летучим, в то время как метанол является худшим растворителем для двуокиси углерода, чем диметиловый эфир, но обладает преимуществом меньшей летучести. Поэтому желателен способ получения диметилового эфира из синтез-газа, в котором возможно применение растворителя, обладающего высокой растворяющей способностью для двуокиси углерода и, одновременно, низкой летучестью.
Краткое содержание изобретения
В общем изобретение относится к улучшенному способу синтеза диметилового эфира с применением метода химической абсорбции двуокиси углерода и, при необходимости, последующего метода твердого адсорбента для удаления двуокиси углерода, присутствующей в синтез-газе и образованной во время превращения газа в диметиловый эфир.
Более конкретно, данное изобретение относится к способу получения продукта диметилового эфира каталитической конверсией синтез-газа в диметиловый эфир, предусматривающему контакт потока синтез-газа, содержащего двуокись углерода, на первой стадии синтеза диметилового эфира с одним или более катализаторами, активными в образовании метанола и дегидратации метанола до диметилового эфира, с получением смеси продукта, содержащей компоненты диметиловый эфир, метанол. двуокись углерода и непрореагировавший синтез-газ, промывание смеси продукта. содержащей двуокись углерода и непрореагировавший синтез-газ, в газопромывочной зоне жидким растворителем, обогащенным карбонатом калия или амином, тем самым селективно абсорбируя двуокись углерода в жидкий растворитель, подвергание таким образом обработанной смеси продукта стадии дистилляции для отделения метанола и воды от потока диметилового эфира и непрореагировавшего синтез-газа с пониженным содержанием двуокиси углерода и отделение непрореагировавшего синтез-газа от продукта диметилового эфира.
Жидкие растворители, особенно подходящие для применения в соответствии с данным изобретением, выбирают из водного растворителя, содержащего карбонат калия, употребляющегося в известных способах Benfield


В одном из вариантов осуществления данного изобретения смесь продукта, обработанную жидким растворителем, подвергают дальнейшему контакту с твердым адсорбентом двуокиси углерода для более тщательного удаления двуокиси углерода.
Подходящие твердые адсорбенты для селективного удаления двуокиси углерода выбирают из группы цеолитов и молекулярных сит, таких как 13-Х и активированный оксид алюминия.
В другом варианте осуществления непрореагировавший синтез-газ, отделенный от продукта диметилового эфира и обедненный двуокисью углерода, рециркулируют в синтез диметилового эфира.
В еще одном варианте осуществления данного изобретения метанол и воду, отделенные от продукта диметилового эфира, передают на вторую стадию синтеза диметилового эфира для дальнейшего превращения метанола в диметиловый эфир.
Краткое описание чертежей
На Фиг.1 показана упрощенная технологическая схема определенного варианта осуществления данного изобретения, в котором применяется одностадийный процесс синтеза диметилового эфира.
Подробное описание изобретения
На Фиг.1 показаны общие стадии способа получения диметилового эфира из синтез-газа.
Синтез-газ 1 подают в реактор 2 синтеза ДМЭ для каталитической конверсии в метанол и ДМЭ согласно реакциям (1) и (2). Реакция смещения также проходит согласно реакции (3). Выходящий поток из реактора 2 синтеза ДМЭ содержит смесь продукта 3, которая содержит смесь диметилового эфира, двуокиси углерода и непрореагировавшего синтез-газа. Смесь продукта 3 охлаждают и направляют в абсорбционную установку 4 и десорбируют водным раствором, содержащим от 20 до 40 мас.% карбоната калия для удаления двуокиси углерода. Обработка карбонатом калия основана на обратимой реакции (5).
Благодаря указанной выше операции десорбции содержание двуокиси углерода в выходящем потоке 5 из зоны десорбции ниже около 500 объем, чнм (частей на миллион). При необходимости, если желательны более низкие уровни двуокиси углерода, выходящий поток 5 может быть направлен в неподвижный слой твердого адсорбента 6, где двуокись углерода селективно адсорбируют в пористую систему адсорбента до содержания в интервале одной или менее объем. чнм. Подходящие твердые адсорбенты выбирают из группы молекулярных сит, как указано выше. Адсорбент предпочтительно распределяют в, по крайней мере, два слоя, работающих параллельно (не показаны) таким образом, что один слой работает в режиме адсорбции в то время как израсходованный абсорбент в другом слое регенерируют. Из адсорбента 6 получают выходящий поток 7, который значительно обеднен двуокисью углерода. Диметиловый эфир. метанол и воду, содержащиеся в выходящем потоке 7. разделяют в дистилляционной колонне 8 с применением обычных средств на верхний продукт 9, содержащий в основном диметиловый эфир, и обедненный двуокисью углерода синтез-газ. Из нижней части колонны 8 выводят жидкий нижний продукт 10, содержащий метанол и воду. Метанол в нижнем продукте 10 может быть рециркулирован в реактор 2 синтеза ДМЭ, или он может быть подвергнут превращению в диметиловый эфир в отдельном реакторе согласно указанной выше реакции (2), и таким образом полученный диметиловый эфир рециркулирует (не показано) в абсорбционную установку 4. Конечный продукт диметилового эфира 11 получают конденсацией верхнего продукта 9 в конденсаторе 14 и фазовым разделением конденсированного эфира 11 и оставшегося синтез-газа 12. Синтез-газ 12, обедненный двуокисью углерода, преимущественно может быть рециркулирован (не показано) в реактор окисления 2.
Пример
Эффект применения способа, описанного выше и показанного на Фиг.1, суммирован в таблицах 1-3 ниже.
Смесь продукта 3, охлажденная до температуры 130°С, имеет состав, показанный в таблице 1.
Таблица 1 | ||
Компонент | Нм 3/ч | объемн. % |
Н2 | 37361 | 17,53 |
Н2O | 1255 | 0,59 |
N2 | 19182 | 9,00 |
СО | 35582 | 16,69 |
СO2 | 69187 | 32,46 |
3173 | 1,49 | |
ДМЭ | 47386 | 22,23 |
После обработки промывкой на основе карбоната калия в абсорбционной установке 4 выходящий поток 5 имеет температуру 71°С при введении в твердый адсорбент 6. Состав выходящего потока 5 показан в таблице 2 и выходящего потока 7 из адсорбента 6 - в таблице 3.
Таблица 2 | ||
Компонент | Нм 3/ч | объемн. % |
Н2 | 37361 | 26,17 |
Н2O | 165 | 0,12 |
N2 | 19182 | 13,43 |
СО | 35582 | 24,92 |
СO2 | 71 | 0,05 |
Метанол | 3173 | 2,22 |
ДМЭ | 47386 | 33,19 |
Таблица 3 | ||
Компонент | Нм 3/ч | % объемн. |
Н2 | 37361 | 26,18 |
h3O | 165 | 0,12 |
N2 | 19182 | 13,43 |
СО | 35582 | 24,92 |
СO2 | 0,14 | 0,0001 |
Метанол | 3173 | 2,22 |
ДМЭ | 47386 | 33,21 |
ФОРМУЛА ИЗОБРЕТЕНИЯ
1. Способ получения продукта диметилового эфира каталитической конверсией синтез-газа в диметиловый эфир, предусматривающий контакт потока синтез-газа, содержащего двуокись углерода, на стадии синтеза диметилового эфира в одном или более реакторах и с одним или более катализаторами, активными в образовании метанола и дегидратации метанола до диметилового эфира, с получением смеси продукта, содержащей компоненты диметиловый эфир, метанол, двуокись углерода и непрореагировавший синтез-газ, промывание смеси продукта, содержащей двуокись углерода и непрореагировавший синтез-газ, в газопромывочной зоне жидким растворителем, обогащенным карбонатом калия или амином, тем самым селективно абсорбируя двуокись углерода в жидкий растворитель, подвергание таким образом обработанной смеси продукта стадии дистилляции для отделения метанола и воды от потока диметилового эфира и непрореагировавшего синтез-газа с пониженным содержанием двуокиси углерода и отделение непрореагировавшего синтез-газа от продукта диметилового эфира.
2. Способ по п.1, предусматривающий дополнительную стадию обработки смеси продукта, выходящей из газопромывочной зоны, твердым адсорбентом двуокиси углерода перед стадией дистилляции для дополнительного удаления двуокиси углерода из смеси.
3. Способ по п.2, где твердый адсорбент выбирают из группы, состоящей из цеолитов, молекулярных сит, активированных оксидов алюминия.
4. Способ по п.1 или 2, где поток синтез-газа, отделенный от продукта диметилового эфира, с пониженным содержанием двуокиси углерода рециркулируют в синтез диметилового эфира.
5. Способ по п.1 или 2, где метанол и воду, отделенные от диметилового эфира на стадии дистилляции, подают на вторую стадию синтеза диметилового эфира для дальнейшей конверсии метанола в диметиловый эфир.
6. Способ по п.5, где поток продукта диметилового эфира со второй стадии синтеза диметилового эфира рециркулируют на стадию дистилляции для отделения воды и метанола от диметилового эфира.
www.freepatent.ru
Способ получения диметилового эфира методом одностадийного синтеза и его выделения
Предлагаемое изобретение относится к способу получения диметилового эфира, который используют в газовых приборах бытового назначения и как пропеллент для аэрозолей, методом одностадийного синтеза и его выделения. Способ включает подачу синтез-газа, проведение реакции в реакторе адиабатического типа при повышенной температуре и давлении в присутствии бифункционального катализатора, охлаждение и сепарацию полученных контактных газов на газовую и жидкую фазы с выделением диметилового эфира из газовой фазы путем абсорбции метанолом с получением абсорбента, насыщенного оксидом углерода (IV) и диметиловым эфиром, и метанола из жидкой фазы путем ректификации. При этом синтез проводят в многоступенчатом реакторе в присутствии бифункционального катализатора двух типов, один из которых обладает более выраженной активностью в отношении синтеза метанола - тип 1, а другой - более выраженной активностью в отношении его дегидратации - тип 2; до подачи в реактор синтез-газ смешивают с газами рецикла, часть полученной смеси нагревают до 255-265°C, впрыскивают в нее метанол, выделенный из жидкой фазы, и подают на первую ступень реактора, другую часть - охлаждают и подают в виде квенчей на каждые последующие ступени реактора в основной газовый поток в количестве, обеспечивающем температуру газа на входе в слой катализатора, расположенного на этих ступенях, 240-250°С; весь поток газовой фазы, выделенный после сепарации, направляют на абсорбцию диметилового эфира, затем полученный насыщенный абсорбент направляют на стриппинг оксида углерода (IV) с получением смеси диметилового эфира и метанола, которую в свою очередь подвергают ректификации с получением дистиллята - диметилового эфира с содержанием примесей от 3,0 до 10,0% мас. и кубового остатка - метанола, который снова направляют на абсорбцию. Способ позволяет простым методом получить целевой продукт с высоким выходом и селективностью. 5 з.п. ф-лы, 1 ил., 6 табл., 5 пр.
Предлагаемое изобретение относится к области нефтехимии и нефтехимического синтеза и более конкретно к технологии получения диметилового эфира (ДМЭ) и выделения его как товарного продукта.
В настоящее время ДМЭ используется в основном в газовых приборах бытового назначения и как пропеллент для аэрозолей. В последние два десятилетия в связи с неуклонным ростом цен на нефтепродукты и связанное с этим изменение сырьевой базы для производства продуктов и полупродуктов нефтехимического синтеза на природный газ, наметилось еще несколько направлений использования ДМЭ - в качестве альтернативного экологически чистого топлива для двигателей внутреннего сгорания или исходного сырья для синтеза бензина и олефинов.
Для целей современной нефтехимической промышленности ДМЭ в ограниченных количествах получают из метанола путем его дегидратации с использованием активной гамма окиси алюминия, а так же как побочный продукт в синтезе метанола.
Наряду с этим, перспективным способом его получения является технология одностадийного синтеза диметилового эфира из синтез-газа с использованием бифункционального катализатора, которая с технической и экономической точек зрения по сравнению с технологией синтеза метанола является достаточно привлекательной, поскольку благоприятное положение термодинамического равновесия позволяет достигать больших конверсий синтез-газа за проход, что в результате приводит к снижению расхода рециркулирующего газа, и, следовательно, к снижению капитальных затрат примерно на 30% [D. Мао, J. Xia, В. Zhang // Energy Conversion and Management. 2010. V.51. PP. 1134-1139].
Особенностями одностадийного синтеза ДМЭ из синтез-газа, который может быть описан системой стехиометрических уравнений (1)-(3), являются неполная конверсия синтез-газа за проход, экзотермичность протекающих в системе реакций, образование наряду с ДМЭ в значительных количествах метанола и оксида углерода (IV):
CO2+3h3⇔Ch4OH+h3O+11.9ккал/моль (1)
2Ch4OH⇔(Ch4)2O+h3O+5.6ккал/моль (2)
CO+h3O⇔CO2+h3+9.8ккал/моль (3)
Наиболее оптимальным по составу для синтеза ДМЭ является синтез-газ с соотношением водород/оксид углерода (II), близким к 1,0, который получают в основном в процессе газификации угля.
Вместе с тем, в России синтез-газ из природного газа получают в основном методом парового риформинга, при этом состав синтез-газа (соотношение водород/оксид углерода (II) 4,5-5,0, модуль 2,6-3,0) является наименее благоприятным для синтеза ДМЭ. Увеличение спроса на ДМЭ приводит к необходимости поиска новых технических решений для проведения процесса одностадийного синтеза. В связи с этим задача разработки процесса синтеза ДМЭ из синтез-газа, полученного именно этим способом, и его выделения из контактных газов является актуальной.
Так, известен способ получения диметилового эфира из синтез-газа, описанный в патенте DE 4222655, согласно которому прямой синтез ДМЭ из синтез-газа с модулем 1,3 осуществляется при температуре 200-350°C, давлении 1,0-10,0 МПа и кратности циркуляции 1,0-5,0 на бифункциональном катализаторе, содержащем в своем составе компоненты синтеза метанола и его дегидратации. Выделение ДМЭ заданного качества осуществляется по схеме, включающей охлаждение и сепарацию при высоком давлении на газовую и жидкую фазы; абсорбцию ДМЭ и оксида углерода (IV), содержащихся в газовом потоке, метанолом; регенерацию абсорбента - метанола; выделение оксида углерода (IV), содержащегося в жидкой фазе после сепарации и газовой фазе после десорбции, методом экстрактивной ректификации, при этом в качестве экстрагента используют метанол или воду или 10-30% мас. водный раствор метанола; разделение эквимолярной смеси ДМЭ/метанол/вода методом ректификации по двухколонной схеме.
Недостатком способа является необходимость выделения наряду с ДМЭ побочного продукта - метанола (двухпродуктовая схема), и громоздкое аппаратурно-технологическое оформление процесса, которое предполагает использование как минимум пяти стадий для выделения товарного ДМЭ.
Наиболее близким техническим решением является способ получения диметилового эфира из синтез-газа с модулем 2,2-2,7 (соотношение водород/оксид углерода (II) 2,2-4,2), описанный в патенте фирмы Haldor Topse US5908963, согласно которому процесс осуществляется при температуре 240-290°C, давлении 42 бар и кратности циркуляции 4,0-5,0 на бифункциональном катализаторе. Разделение продуктов реакции включает стадии охлаждения и сепарации контактного газа; возврат части газового потока без выделения оксида углерода (IV) на синтез оксигенатов; выделение ДМЭ из газов сдувки абсорбцией метанолом; получение дополнительного количества ДМЭ дегидратацией насыщенного абсорбента; разделение жидкой фазы и продуктов реакции дегидратации, содержащих смесь ДМЭ/метанол/вода, методом ректификации по двухколонной схеме, при этом выделяемый метанол используется в качестве абсорбента на стадии выделения ДМЭ из газов сдувки, а водный конденсат выводится из системы. Выход и селективность ДМЭ по углероду в расчете на углерод оксидов углерода (II) и (IV) составляет 83,9-85,4% мас. и 89,6-90,3% мас. соответственно при степени использования углерода 93,7-94,6%.
Недостатком способа является недостаточно высокий выход и селективность образования ДМЭ, а также чистота продукта - получаемый ДМЭ содержит в своем составе до 20% мас. примесей - метанола и воды и может быть использован только в качестве топлива в двигателях внутреннего сгорания.
Вместе с тем, присутствие метанола в ДМЭ, использующемся в качестве исходного сырья для синтеза бензина и олефинов, нежелательно, поскольку метанол приводит к образованию побочных продуктов, таких как дурол и метан. Кроме того, присутствие метанола и оксида углерода (IV) в ДМЭ ухудшает эксплуатационные характеристики топлива.
Задачей настоящего изобретения является разработка одностадийного способа получения диметилового эфира из синтез-газа, полученного различными способами, в том числе синтез-газа парового риформинга, обеспечивающего высокий выход и селективность по ДМЭ при производительности, соответствующей известным из уровня техники техническим решениям или их превышающим, а также выделения ДМЭ как товарного продукта, соответствующего ТУ 2434-052-05761695-2007 «Эфир диметиловый жидкий», или как кондиционного продукта с содержанием примесей не более 10% мас., с целью его дальнейшего использования в качестве альтернативного экологически чистого топлива для двигателей внутреннего сгорания или исходного сырья для синтеза высокооктанового бензина и олефинов.
Поставленная задача решается тем, что предложен способ получения диметилового эфира методом одностадийного синтеза и его выделения, включающий подачу синтез-газа, проведение реакции в реакторе адиабатического типа при повышенной температуре и давлении в присутствии бифункционального катализатора, охлаждение и сепарацию полученных контактных газов на газовую и жидкую фазы с выделением диметилового эфира из газовой фазы путем абсорбции метанолом с получением абсорбента, насыщенного оксидом углерода (IV) и диметиловым эфиром, и метанола из жидкой фазы путем ректификации, в котором синтез проводят в многоступенчатом реакторе в присутствии бифункционального катализаторов двух типов, один из которых обладает более выраженной активностью в отношении синтеза метанола - тип 1, а другой - более выраженной активностью в отношении его дегидратации - тип 2; до подачи в реактор синтез-газ смешивают с газами рецикла, часть полученной смеси нагревают до 255-265°C, впрыскивают в нее метанол, выделенный из жидкой фазы, и подают на первую ступень реактора, другую часть - охлаждают и подают в виде квенчей на каждые последующие ступени реактора в основной газовый поток в количестве, обеспечивающем температуру газа на входе в слой катализатора, расположенного на этих ступенях, 240-250°C; весь поток газовой фазы, выделенный после сепарации, направляют на абсорбцию диметилового эфира, затем полученный насыщенный абсорбент направляют на стриппинг оксида углерода (IV) с получением смеси диметилового эфира и метанола, которую в свою очередь подвергают ректификации с получением дистиллята - диметилового эфира с содержанием примесей от 3,0 до 10,0% мас. и кубового остатка - метанола, который снова направляют на абсорбцию.
Реализация предложенного способа получения диметилового эфира возможна при использовании синтез-газа, соответствующего модулю 1,0-3,0 и соотношению водород/оксид углерода (II), равному 1,0-5,0.
В предложенном способе получения диметилового эфира в качестве катализатора типа 1 используют медь-цинковый катализатор, расположенный на всех ступенях реактора, а в качестве катализатора типа 2 - медь-цинк-хромовый катализатор, расположенный на последней ступени реактора послойно под катализатором типа 1 по ходу основного газового потока.
Неконденсирующиеся после абсорбции диметилового эфира газы, содержащие водород, оксиды углерода (II) и (IV), метан, азот, а также следы метанола и диметилового эфира, направляют на смешение с исходным синтез-газом как газ рецикла.
Газ после стриппинга, содержащий преимущественно оксид углерода (IV), направляют на смешение с исходным синтез-газом как газ рецикла.
Для получения диметилового эфира с содержанием примесей 3,0% мас. метанол, выделенный из жидкой фазы методом ректификации, возвращают на вход в реактор синтеза диметилового эфира в объеме не менее 42,5% или для получения диметилового эфира с содержанием примесей 10,0% мас. - не менее 20,7%.
Технический результат от использования предлагаемого изобретения заключается:
1) в увеличении выхода и селективности образования ДМЭ в расчете на углерод оксидов углерода (II) и (IV) по сравнению с прототипом за счет использования двухслойной загрузки катализатора на последней ступени реактора и рецикла метанола на вход первой секции реактора.
2) в увеличении чистоты получаемого ДМЭ с получением товарного продукта, соответствующего ТУ 2434-052-05761695-2007 «Эфир диметиловый жидкий», или кондиционного продукта с содержанием примесей не более 10% мас.;
3) в упрощении процесса за счет исключения отдельной стадии дегидратации метанола.
Принципиальная схема процесса для варианта использования в качестве аппаратурного оформления трехступенчатого адиабатического реактора с межступенчатым охлаждением контактного газа путем подачи холодного потока синтез-газа (квенча) на вход в каждую ступень представлена на фиг.1.
Схема получения и выделения ДМЭ работает следующим образом:
Свежий синтез-газ с помощью компрессора (1) компримируют до заданного давления 5,0-9,0 МПа, смешивают с газами рецикла - газами из абсорбера (8) и стриппинг-колонны (9). Смесь свежего синтез-газа и газов рецикла разделяют на два потока. Часть потока охлаждают и подают в реактор синтеза ДМЭ (3) в качестве холодных квенчей на вторую и третью ступени реактора перпендикулярно основному потоку. Температура газа на входе в слой катализатора на второй и третьей ступенях - 240-250°С. Основной поток подогревают до температуры 220-230°С за счет тепла контактных газов, отходящих из реактора синтеза ДМЭ (3), перегревают до температуры 255-265°С и направляют на вход в реактор (3) - на первую его ступень. Перед входом в реактор в горячий поток впрыскивают возвратный метанол.
Реактор синтеза ДМЭ (3) представляет собой секционированный адиабатический аппарат с холодными квенчами, в который загружено два типа бифункционального катализатора. На всех ступенях реактора расположен модифицированный активной гамма окисью алюминия промышленный медь-цинковый катализатор синтеза метанола (тип 1). На третьей ступени расположено два слоя катализатора: первый слой медь-цинковый катализатор (тип 1), второй слой, расположенный под первым по ходу основного газового потока, - медь-цинк-хромовый катализатор (тип 2). Характеристика катализаторов представлена в таблице 1.
Таблица 1 | ||
Характеристика используемых катализаторов синтеза ДМЭ. | ||
Состав: % масс. | Катализатор | |
медь-цинковый (тип 1) | медь-цинк-хромовый (тип 2) | |
СuО | 44,5±1,5 | 23,5±1,5 |
ZnO | 19,6±1,5 | 23,5±1,5 |
Сr2О3 | - | 16,5±1,5 |
Аl2О3 | 35,9±1,5 | 34,5±1,5 |
графит | до 1,5 | до 2 |
Размер гранул, мм | 6×4±0,5 | 6×4±0,5 |
Насыпная плотность, г/дм3 | 0,9-1,1 | 1,0-1,1 |
Содержание пыли и мелочи, % масс. | не более 1,5 | не более 1,5 |
Контактные газы из реактора охлаждают до 40°С, при этом пары метанола и воды конденсируются. Полученная паро-газо-жидкостная смесь поступает в сепаратор (5), где происходит разделение фаз.
Жидкую фазу из сепаратора (5) нагревают и направляют в ректификационную колонну (6). Дистиллятный пар из колонны (6), представляющий собой метанол с примесями воды, ДМЭ и оксида углерода (IV), направляют в конденсатор (11), из которого часть сконденсировавшегося потока возвращают в колонну (6) в качестве флегмы, а остальную часть - охлаждают и собирают в емкости (12), откуда подают на вход в реактор синтеза ДМЭ. В виде кубовой жидкости из колонны (6) выводят воду с небольшим содержанием метанола.
Газовую фазу из сепаратора (5) полностью направляют на очистку от ДМЭ и СO2 в абсорбер (8), орошаемый метанолом. Часть газового потока вместе с газами из абсорбера (8) подают на всас циркуляционного компрессора (4). Для предотвращения накопления инертов в системе часть газового потока из абсорбера (8) выводят в виде сдувки. Абсорбент, насыщенный ДМЭ и оксидом углерода (IV), из абсорбера (8) подают в стриппинг-колонну (9). Газы стриппинга - в основном оксид углерода (IV) с небольшим содержанием ДМЭ направляют на всас компрессора (2). Кубовый продукт стриппинг-колонны (9), представляющий собой раствор ДМЭ в метаноле, направляют в ректификационную колонну (10). Кубовый продукт - метанол охлаждают и собирают в емкости (7), откуда подают на орошение абсорбера (8).
С верха колонны (10) в виде дистиллята выводят ДМЭ с содержанием примесей от 3,0 до 10,0% мас.
Нижеследующие примеры иллюстрируют предлагаемое изобретение, но никоим образом не ограничивают его.
Номера потоков в таблицах материального баланса соответствуют позициям, приведенным на фиг.1. Принципиальная схема процесса получения диметилового эфира методом одностадийного синтеза и его выделения.
Пример 1.
Получение ДМЭ с содержанием примесей 3,0% мас. из синтез-газа с модулем 2,9.
В качестве сырья используют синтез-газ с модулем 2,9 и соотношением водород/оксид углерода (II), равным 4,7. Процесс проводят в реакторе синтеза ДМЭ (3), в который загружено два типа катализатора, при давлении 7,0 МПа, температуре 240-300°C и кратности циркуляции 5,0-5,5 по способу, описанному выше.
Метанол из жидкой фазы выделяют в ректификационной колонне (6), работающей при давлении 1,0 МПа и температуре в кубе колонны 170-180°C. Часть выделенного метанола - 42,5%об. - подают на вход в реактор синтеза ДМЭ (3) на первую ступень катализатора, другую часть метанола выводят вместе с товарным ДМЭ.
ДМЭ из контактных газов последовательно выделяют в абсорбере (8), стриппинг-колонне (9) и ректификационной колонне (10).
Абсорбцию проводят при температуре 40-50°C и давлении 5,5-6,5 МПа. В качестве абсорбента используют метанол с содержанием воды 20-30% мас. Степень извлечения ДМЭ в абсорбере (8) составляет 85-90%. Газовый поток из абсорбера частично подают на всас циркуляционного компрессора (4), частично сдувают.
Стриппинг оксида углерода (IV) из насыщенного абсорбента проводят при давлении 1,0-1,5 МПа и температуре в кубе колонны 100-120°C. Газ стриппинга, содержащий в своем составе в основном оксид углерода (IV), с помощью компрессора (2) компримируется до давления 7,0 МПа и направляется на смешение с газами из абсорбера (8) и далее со свежим синтез-газом.
Ректификацию смеси ДМЭ/метанол/вода проводят при давлении 1,0-2,0 МПа и температуре в кубе колонны 140-160°C. В качестве дистиллята с верха ректификационной колонны (10) выводят ДМЭ с содержанием примесей 3,0% мас.
Результаты, полученные при инженерных расчетах материального баланса описанного выше процесса, приведены в таблице 2.
Таблица 2 | |||||
Материальный баланс схемы, работающей по примеру 1. | |||||
Номера потоков | 1-свежий синтез-газ | 2-сдувка | 3-рецикл | 4-вода | 5-ДМЭ |
Расход, кмоль/ч | 1588 | 479 | 7913 | 270 | 167 |
Состав, % мас. | |||||
ДМЭ | 0,0 | 4,5 | 9,5 | 0,0 | 97,0 |
Метанол | 0,0 | 3,4 | 3,1 | 1,0 | 1,8 |
Вода | 1,0 | 0,4 | 0,4 | 99,0 | 0,2 |
Н2 | 15,1 | 26,5 | 24,6 | 0,0 | 0,0 |
СО | 44,6 | 6,7 | 6,3 | 0,0 | 0,0 |
СO2 | 31,3 | 15,9 | 16,2 | 0,0 | 1,0 |
СН4 | 6,9 | 36,7 | 34,5 | 0,0 | 0,0 |
N2 | 1,1 | 5,9 | 5,5 | 0,0 | 0,0 |
В выбранных условиях достигнут выход и селективность ДМЭ в расчете на углерод оксидов углерода (II) и (IV) 90,6% мас. и 97,8% мас. соответственно при степени использования углерода 92,6% масс. и производительности по ДМЭ 0,21 кг(ДМЭ)/нм3(синтез-газ).
Пример 2. Получение ДМЭ с содержанием примесей 10% мас. из синтез-газа с модулем 2,9.
Процесс проводят по методу и при условиях, описанных в примере 1. Отличается от примера 1 тем, что на вход в реактор синтеза ДМЭ возвращают 20,7%об. метанола, выделенного из жидкой фазы. В качестве продукта из схемы выводят ДМЭ с содержанием примесей 10,0% мас.
Результаты расчета материального баланса приведены в таблице 3.
Таблица 3 | |||||
Материальный баланс схемы, работающей по примеру 2. | |||||
Номера потоков | 1-свежи и синтез-газ | 2-сдувка | 3-рецикл | 4-вода | 5-ДМЭ |
Расход, кмоль/ч | 1588 | 478 | 7913 | 261 | 177 |
Состав, % мас. | |||||
ДМЭ | 0,0 | 4,1 | 9,1 | 0,0 | 90,0 |
Метанол | 0,0 | 3,4 | 3,1 | 1,0 | 8,5 |
Вода | 1,0 | 0,4 | 0,3 | 99,0 | 0,5 |
Н2 | 15,1 | 26,7 | 24,8 | 0,0 | 0,0 |
СО | 44,6 | 6,8 | 6,4 | 0,0 | 0,0 |
СO2 | 31,3 | 15,6 | 15,9 | 0,0 | 1,0 |
СН4 | 6,9 | 37,0 | 34,9 | 0,0 | 0,0 |
N2 | 1,1 | 6,0 | 5,6 | 0,0 | 0,0 |
В выбранных условиях достигнут выход и селективность ДМЭ в расчете на углерод оксидов углерода (II) и (IV) 86,2% мас. и 92,8% мас. соответственно при степени использования углерода 92,8% мас. и производительности по ДМЭ 0,22 кг(ДМЭ)/нм3(синтез-газ).
Пример 3. Получение ДМЭ с содержанием примесей 10% мас. из синтез-газа с модулем 2,2.
Процесс проводят по методу, описанному в примере 1. Отличается от примера 1 тем, что процесс проводят при температуре 230-320°C и в качестве сырья используют синтез-газ с модулем 2,2 и соотношением водород/оксид углерода (II), равным 2,2; на вход в реактор синтеза ДМЭ возвращают 17,5%об. метанола, выделенного из жидкой фазы. В качестве продукта из схемы выводят ДМЭ с содержанием примесей 10,0% мас. Результаты расчета материального баланса приведены в таблице 4.
Таблица 4 | |||||
Материальный баланс схемы, работающей по примеру 3. | |||||
Номера потоков | 1-свежий синтез-газ | 2-сдувка | 3-рецикл | 4-вода | 5-ДМЭ |
Расход, кмоль/ч | 1481 | 162 | 7913 | 199 | 238 |
Состав, % мас. | |||||
ДМЭ | 0,0 | 5,1 | 9,2 | 0,0 | 90,0 |
Метанол | 0,0 | 3,2 | 2,9 | 1,0 | 8,4 |
Вода | 1,0 | 0,4 | 0,3 | 99,0 | 0,6 |
Н2 | 13,1 | 17,8 | 16,6 | 0,0 | 0,0 |
СО | 82,5 | 16,7 | 15,6 | 0,0 | 0,0 |
СO2 | 1,7 | 25,7 | 26,1 | 0,0 | 1,0 |
СН4 | 1,8 | 20,1 | 19,0 | 0,0 | 0,0 |
N2 | 1,0 | 11,0 | 10,3 | 0,0 | 0,0 |
В выбранных условиях достигнут выход и селективность ДМЭ в расчете на углерод оксидов углерода (II) и (IV) 89,0% мас. и 93,1% мас. соответственно при степени использования углерода 95,6% мас. и производительности по ДМЭ 0,28 кг(ДМЭ)/нм3(синтез-газ).
Пример 4. Получение ДМЭ без возврата метанола на вход в реактор.
Процесс проводят по методу и при условиях, описанных в примере 1. Отличается от примера 1 тем, что в газовый поток, который подают на первую ступень реактора синтеза ДМЭ, не впрыскивают метанол, выделенный из жидкой фазы. Из схемы выводят либо два продукта - ДМЭ с содержанием примесей 10,0% мас. (поток 5) и метанол с содержанием примесей 5,0% мас. (поток 6), либо ДМЭ с содержанием примесей 16,1% мас. (поток 5а). Результаты расчета материального баланса для двух вариантов приведены в таблице 5.
Таблица 5 | |||||||
Материальный баланс схемы, работающей по примеру 4. | |||||||
№№ потоков | 1-свежий синтез-газ | 2-сдувка | 3-рецикл | 4-вода | 5-ДМЭ | 6-метанол | 5а-ДМЭ |
Расход, кмоль/ч | 1588 | 477 | 7913 | 252 | 169 | 18 | 186 |
Состав, % мас. | |||||||
ДМЭ | 0,0 | 3,9 | 8,9 | 0,0 | 90,0 | 0,5 | 83,9 |
Метанол | 0,0 | 3,3 | 3,1 | 1,0 | 8,5 | 95,0 | 14,4 |
Вода | 1,0 | 0,4 | 0,3 | 99,0 | 0,5 | 4,3 | 0,7 |
Н2 | 15,1 | 26,9 | 25,0 | 0,0 | 0,0 | 0,0 | 0,0 |
СО | 44,6 | 6,9 | 6,4 | 0,0 | 0,0 | 0,0 | 0,0 |
СO2 | 31,3 | 15,2 | 15,5 | 0,0 | 1,0 | 0,0 | 0,9 |
СН4 | 6,9 | 37,3 | 35,2 | 0,0 | 0,0 | 0,0 | 0,0 |
N2 | 1,1 | 6,0 | 5,6 | 0,0 | 0,0 | 0,0 | 0,0 |
Таким образом, без рецикла метанола на вход в реактор синтеза ДМЭ получают с низким выходом ДМЭ, не соответствующий заданным стандартам. Выход и селективность ДМЭ в расчете на углерод оксидов углерода (II) и (IV) составляет 72,6% мас. и 78,0% мас. соответственно при степени использования углерода 93,0% мас. и производительности по ДМЭ 0,18 кг(ДМЭ)/нм3(синтез-газ).
Пример 5. Получение ДМЭ с содержанием примесей 10% мас. без бифункционального катализатора типа (2).
Процесс проводят по методу и при условиях, описанных в примере 1. Отличается от примера 1 тем, что в реактор на всех ступенях загружен только катализатор типа (1). На вход в реактор синтеза ДМЭ возвращают 89,3%об. метанола, выделенного из жидкой фазы. В качестве продукта из схемы выводят ДМЭ с содержанием примесей 10,0% мас. Результаты расчета материального баланса приведены в таблице 6.
Таблица 6 | |||||
Материальный баланс схемы, работающей по примеру 5. | |||||
Номера потоков | 1-свежи и синтез-газ | 2-сдувка | 3-рецикл | 4-вода | 5-ДМЭ |
Расход, кмоль/ч | 1588 | 642 | 7913 | 213 | 152 |
Состав, % мас. | |||||
ДМЭ | 0,0 | 1,3 | 4,3 | 0,0 | 90,0 |
Метанол | 0,0 | 2,9 | 2,8 | 1,0 | 8,8 |
Вода | 1,0 | 0,2 | 0,2 | 99,0 | 0,2 |
Н2 | 15,1 | 20,9 | 19,2 | 0,0 | 0,0 |
СО | 44,6 | 15,3 | 14,2 | 0,0 | 0,0 |
СO2 | 31,3 | 33,7 | 35,3 | 0,0 | 1,0 |
СН4 | 6,9 | 22,1 | 20,7 | 0,0 | 0,0 |
N2 | 1,1 | 3,6 | 3,3 | 0,0 | 0,0 |
Таким образом, без использования катализатора типа (2) получают ДМЭ с низким выходом. Выход и селективность ДМЭ в расчете на углерод оксидов углерода (II) и (IV) составляет 74,2% мас. и 92,6% мас. соответственно при степени использования углерода 80,2% мас. и производительности по ДМЭ 0,17 кг(ДМЭ)/нм3(синтез-газ).
Предлагаемый способ одностадийного синтеза ДМЭ из синтез-газа, полученного различными способами, в том числе синтез-газа парового риформинга, позволяет достигать выход и селективность образования ДМЭ по углероду в расчете на углерод оксидов углерода (II) и (IV) на 5-10% мас. выше данных показателей, достигаемых в прототипе, при производительности, соответствующей уровню мировых стандартов, и выделять ДМЭ как товарный продукт, соответствующий ТУ 2434-052-05761695-2007 или как кондиционный продукт с содержанием примесей не более 10% мас. с целью его дальнейшего использования в качестве альтернативного экологически чистого топлива для двигателей внутреннего сгорания или исходного сырья для синтеза высокооктанового бензина и олефинов.
1. Способ получения диметилового эфира методом одностадийного синтеза и его выделения, включающий подачу синтез-газа, проведение реакции в реакторе адиабатического типа при повышенной температуре и давлении в присутствии бифункционального катализатора, охлаждение и сепарацию полученных контактных газов на газовую и жидкую фазы с выделением диметилового эфира из газовой фазы путем абсорбции метанолом с получением абсорбента, насыщенного оксидом углерода (IV) и диметиловым эфиром, и метанола из жидкой фазы путем ректификации, отличающийся тем, что синтез проводят в многоступенчатом реакторе в присутствии бифункционального катализатора двух типов, один из которых обладает более выраженной активностью в отношении синтеза метанола - тип 1, а другой - более выраженной активностью в отношении его дегидратации - тип 2; до подачи в реактор синтез-газ смешивают с газами рецикла, часть полученной смеси нагревают до 255-265°C, впрыскивают в нее метанол, выделенный из жидкой фазы, и подают на первую ступень реактора, другую часть - охлаждают и подают в виде квенчей на каждые последующие ступени реактора в основной газовый поток в количестве, обеспечивающем температуру газа на входе в слой катализатора, расположенного на этих ступенях, 240-250°С; весь поток газовой фазы, выделенный после сепарации, направляют на абсорбцию диметилового эфира, затем полученный насыщенный абсорбент направляют на стриппинг оксида углерода (IV) с получением смеси диметилового эфира и метанола, которую в свою очередь подвергают ректификации с получением дистиллята - диметилового эфира с содержанием примесей от 3,0 до 10,0% мас. и кубового остатка - метанола, который снова направляют на абсорбцию.
2. Способ получения диметилового эфира по п.1, отличающийся тем, что используют синтез-газ, характеризующийся модулем 1,0-3,0 и соотношением водород/оксид углерода (II), равным 1,0-5,0.
3. Способ получения диметилового эфира по п.1, отличающийся тем, что в качестве катализатора типа 1 используют медь-цинковый катализатор, расположенный на всех ступенях реактора, а в качестве катализатора типа 2 - медь-цинк-хромовый катализатор, расположенный на последней ступени реактора послойно под катализатором типа 1 по ходу основного газового потока.
4. Способ получения диметилового эфира по п.1, отличающийся тем, что неконденсирующиеся после абсорбции диметилового эфира газы, содержащие водород, оксиды углерода (II) и (IV), метан, азот, а также следы метанола и диметилового эфира, направляют на смешение с исходным синтез-газом как газ рецикла.
5. Способ получения диметилового эфира по п.1, отличающийся тем, что газ после стриппинга, содержащий преимущественно оксид углерода (IV), направляют на смешение с исходным синтез-газом как газ рецикла.
6. Способ получения диметилового эфира по п.1, отличающийся тем, что для получения диметилового эфира с содержанием примесей 3,0% мас. метанол, выделенный из жидкой фазы методом ректификации, возвращают на вход в реактор синтеза диметилового эфира в объеме не менее 42,5% или для получения диметилового эфира с содержанием примесей 10,0% мас. - не менее 20,7%.
www.findpatent.ru
Способ получения диметилового эфира из метанола
Настоящее изобретение относится к способу получения диметилового эфира, применяемого в качестве хладагента и газа вытеснителя аэрозольных упаковок, из метанола. Способ заключается в контактировании метанола с дегидратирующим катализатором в реакционной зоне и разделении компонентов реакционной смеси с помощью ректификации с возвращением непрореагировавшего метанола в реакционную зону, при котором дегидратацию метанола и образование эфира проводят в присутствии катализатора при повышенной температуре. При этом в качестве катализатора применяют молекулярные сита цеолитного типа с крупными порами, выбранные из группы, состоящей из цеолитов структуры FAU, являющихся цеолитами типа X и их модификациями, дегидратацию осуществляют в газообразном состоянии при температуре в реакционной зоне 280÷330°C и давлении 17÷22 атм, в первой ректификационной колонне отгоняют от воды фракцию, состоящую из метанола и диметилового эфира, во второй ректификационной колонне отгоняют от непрореагировавшего метанола диметиловый эфир и возвращают метанол в реакционную зону. Способ позволяет получить диметиловый эфир с высокими выходом и чистотой. 1 ил., 1 табл., 4 пр.
Область техники
Данное изобретение относится к химической промышленности, конкретно к области получения диметилового эфира (ДМЭ), применяемого в качестве хладагента и газа вытеснителя аэрозольных упаковок.
Качество очистки газа вытеснителя определяет его использование в тех отраслях, где очень высоки требования к газу по содержанию меркаптанов и влаги (парфюмерно-косметическая продукция, медицинские аэрозоли, производство автокосметики, монтажной пены, лакокрасочной продукции).
Уровень техники
Известно достаточно много процессов, в которых ДМЭ получают дегидратацией метанола с использованием различных катализаторов.
Согласно патенту [1] [патент RU 2459799, С2, дата публикации 27.08.2012 г.] в качестве катализаторов могут использоваться молекулярные сита цеолитного и/или нецеолитного типов. В качестве молекулярных сит используются одно или несколько сит, с FAU структурой, выбранных из группы, состоящей из цеолитов Y-типа, которые имеют большие поры. Молекулярное сито нецеолитного типа может быть силикоалюмофосфатным.
К недостаткам указанного способа следует отнести высокую склонность к косообразованию катализаторов при температуре реакции.
В патенте [2] [патент RU 2282613, С2, дата публикации 27.08.2006 г.] дегидратацию метанола проводят в присутствии сульфоионитного катализатора при повышенной температуре и давлении в совмещенном реакционно-ректификационном аппарате.
Наиболее близким по своей технической сущности и достигаемому техническому результату является изобретение «Способ получения диметилового эфира» [3], [патент RU №2256645, С2, дата публикации 20.07.2005 г.]. Согласно данному изобретению метанолсодержащий поток контактирует с дегидратирующим катализатором в одной или нескольких реакционных зонах. Компоненты реакционной смеси с помощью дистилляции и/или ректификации разделяют с возвращением непрореагировавшего метанола в реакционную зону. Дегидратацию метанола и образование эфира проводят в жидком и/или парожидкостном состоянии в присутствии кислого катионита при температуре 100-460°C и поддерживают концентрацию воды в возвращаемом реакционную зону метанольном потоке менее 12% масс, предпочтительно менее 5% масс.
Основными недостатками прототипа являются:
- применение двухреакторной схемы для дегидратации;
- применение водной отмывки выделенного потока диметилового эфира от метанола и подача воднометанольной смеси в зону ректификации от воды;
- применение реакционно-ректификационного аппарата приведет к усложнению технологической схемы.
Задача предлагаемого способа заключается в создании экологически чистой технологии получения ДМЭ дегидратацией метанола на молекулярном сите цеолитного типа, которая позволит получить продукцию необходимого качества для использования ее в качестве газа вытеснителя аэрозольных упаковок и значительно снизить эксплуатационные и капитальные затраты на реализацию и проведение процесса.
Раскрытие изобретения
Поставленная задача достигается тем, что в способе получения диметилового эфира из метанола, путем его контактирования с дегидратирующим катализатором в реакционной зоне и разделении компонентов реакционной смеси с помощью ректификации с возвращением непрореагировавшего метанола в реакционную зону, при котором дегидратацию метанола проводят в присутствии катализатора при повышенной температуре, в отличие от прототипа, в качестве катализатора применяют молекулярные сита цеолитного типа с крупными порами, выбранные из группы, состоящей из цеолитов структуры FAU, являющихся цеолитами типа X и их модификациями, дегидратацию осуществляют в газообразном состоянии при температуре в реакционной зоне 280÷380°C и давлении 17÷22 атм, в первой ректификационной колонне отгоняют от воды фракцию, состоящую из метанола и диметилового эфира, во второй ректификационной колонне отгоняют от непрореагировавшего метанола диметиловый эфир и возвращают метанол в реакционную зону. Предлагаемый способ получения диметилового эфира осуществляется на установке, которая представлена на чертеже, где приведена принципиальная схема установки.
Установка работает следующим образом.
Для получения ДМЭ используют метанол концентрации не менее 99,5%, массовая доля серы не более 0,0001%, массовая доля воды не более 0,05%, массовая доля альдегидов и кетонов не более 0,003%.
Согласно схемы установки на чертеже метанол поступает по линии 1. Его смешивают с рециркулируемым метанольным потоком 11, поступающим из куба колонны 14, подогревают в теплообменнике до температуры 300-350°C и по лини 2 направляют в реакционную зону реактора 12, содержащую цеолит типа X. Из реакционной зоны реактора 12 по линии 3 выводят реакционную смесь, которую подают в отгонную зону колонны 13 по линии 3. Отгонная зона колонны 13 представляет собой ректификационную колонну.
Сверху ректификационной колонны 13 по линии 5 выводят паровой поток, содержащий преимущественно ДМЭ и метанол. Далее поток охлаждается в конденсаторе дефлегматоре и поступает в колонну 14 по линии 7. Часть сконденсированного потока по линии 6 возвращают в колонну 13 в виде флегмы. Снизу колонны 13 по линии 4 выводят поток, содержащий преимущественно воду. Ректификационная колонна 14 предназначена для разделения ДМЭ от метанола. Сверху ректификационной колонны 14 по линии 8 выводят паровой поток, содержащий ДМЭ. Далее поток охлаждается в конденсаторе дефлегматоре и поступает по линии 10 на склад. Часть сконденсированного потока по линии 9 возвращают в колонну 14 в виде флегмы. Снизу колонны 14 по линии 11 выводят поток, содержащий преимущественно метанол.
Примеры 1-4 показывают реализацию настоящего изобретения по способу получения диметилового эфира, путем контактирования его с дегидратирующими катализаторами с использованием различных вариантов загрузки в реакционную зону молекулярных сит цеолитного типа с крупными порами, выбранных из группы, состоящей из цеолитов структуры FAU, являющихся цеолитами типа X.
Пример 1. Данный пример иллюстрирует реализацию по способу получения диметилового эфира с применением в качестве катализатора молекулярного сита цеолитного типа с крупными порами, выбранного из группы, состоящей из цеолитов структуры FAU, являющееся цеолитом NaX.
Способ получения ДМЭ реализован на установке см.чертеж.
Согласно схемы установки на чертеже метанол в количестве 463,3 кг/ч поступает по линии 1. Его смешивают с рециркулируемым метанольным потоком 11, поступающим из куба колонны 14, подогревают в теплообменнике преимущественно до температуры 310°C и по лини 2 направляют в реакционную зону реактора 12, содержащую цеолит типа NaX, размер гранул 1,8÷2,2 мм, в количестве 0,5 м3. Реактор представляет собой аппарат адиабатического типа. Реакция дегидратации осуществляется при температуре 300°C и давлении 2,0 МПа. Конверсия метанола за проход 90%. Из реакционной зоны по линии 3 выводят реакционную смесь. Реакционную смесь из реактора 12 в количестве 1000 кг/ч подают в ректификационную колонну 13 по линии 3. Поток 3 содержит 32,31% ДМЭ; 53,67% метанола и 14,02% воды. Процесс ректификации осуществляют при абсолютном давлении в кубе колонны 13 равном 0,37 МПа, верха колонны 13 равном 0,32 МПа. Температуры: куба - 140°C; тарелки питания - 55°C; верха - 40°C.
Сверху ректификационной колонны 13 по линии 5 выводят паровой поток, содержащий ДМЭ и метанол. Далее поток охлаждается в конденсаторе дефлегматоре и поступает в колонну 14, по линии 7 выводится 859,8 кг/ч продукта, содержащего 37,60% ДМЭ и 62,40% метанола. Часть сконденсированного потока по линии 6 возвращают в колонну 13 в виде флегмы. Снизу колонны 13 по линии 4 выводится поток, содержащий преимущественно воду в количестве 140,2 кг/ч. Ректификационная колонна 14 предназначена для разделения ДМЭ от метанола. Сверху ректификационной колонны 14 по линии 8 выводится паровой поток, содержащий ДМЭ. Далее поток охлаждается в конденсаторе дефлегматоре и поступает по линии 10 на склад в количестве 323,1 кг/ч. Часть сконденсированного потока по линии 9 возвращается в колонну 14 в виде флегмы. Снизу колонну 14 по линии 11 выводится поток, содержащий преимущественно метанол в количестве 536,7 кг/ч.
Пример 2. Данный пример иллюстрирует реализацию по способу получения диметилового эфира аналогично примеру 1, отличающемуся тем, что в качестве катализатора применяют молекулярное сито цеолитного типа с крупными порами, выбранное из группы, состоящей из цеолитов структуры FAU, являющееся цеолитом НХ.
Пример 3. Данный пример иллюстрирует реализацию по способу получения диметилового эфира аналогично примеру 1, отличающийся тем, что в качестве катализатора применяют молекулярное сито цеолитного типа с крупными порами, выбранное из группы, состоящей из цеолитов структуры FAU, являющихся цеолитом LiX.
Пример 4. Данный пример иллюстрирует реализацию по способу получения диметилового эфира аналогично примеру 1, отличающемуся тем, что в качестве катализатора применяют молекулярное сито цеолитного типа с крупными порами, выбранное из группы, состоящей из цеолитов структуры FAU, являющихся цеолитом HLiX.
Показатели качества полученных диметиловых эфиров приведены в таблице 1.
Достигаемый технический результат
Преимуществом заявляемой установки перед прототипом являются:
- получение ДМЭ высокой концентрации 99,99% и выше без постороннего запаха, что позволит его использовать в качестве газа вытеснителя аэрозольных упаковок;
- получение ДМЭ высокого качества с низким содержанием воды до 0,0001%;
- получение ДМЭ с низким содержанием сернистых соединений до 0,0001%;
- предложен катализатор дегидратации метанола в виде молекулярных сит цеолитного типа с крупными порами, выбранных из группы, состоящей из цеолитов структуры FAU, являющихся цеолитами типа X и их модификациями, который позволил увеличить конверсию ДМЭ до 90% и выше.
Способ получения диметилового эфира из метанола, путем его контактирования с дегидратирующим катализатором в реакционной зоне и разделении компонентов реакционной смеси с помощью ректификации с возвращением непрореагировавшего метанола в реакционную зону, при котором дегидратацию метанола и образование эфира проводят в присутствии катализатора при повышенной температуре, отличающийся тем, что в качестве катализатора применяют молекулярные сита цеолитного типа с крупными порами, выбранные из группы, состоящей из цеолитов структуры FAU, являющихся цеолитами типа X и их модификациями, дегидратацию осуществляют в газообразном состоянии при температуре в реакционной зоне 280÷330°C и давлении 17÷22 атм, в первой ректификационной колонне отгоняют от воды фракцию, состоящую из метанола и диметилового эфира, во второй ректификационной колонне отгоняют от непрореагировавшего метанола диметиловый эфир и возвращают метанол в реакционную зону.
www.findpatent.ru
Способ получения диметилового эфира высокой чистоты
Использование: нефтехимия. Сущность: проводят дегидратацию метанола в присутствии сульфоионитного катализатора при 110-150°С, давлении 4,9-13,2 ата в совмещенном реакционно-ректификационном аппарате, состоящем из трех зон: двух ректификационных и средней реакционной, заполненной катализатором. Метанол подают или в катализаторную зону, или в нижнюю ректификационную зону. Возможно размещение реакционной и ректификационной зон как внутри одного аппарата, так и раздельно в двух или трех аппаратах таким образом, что в них совокупно осуществляют единый реакционно-ректификационный процесс. Целевой эфир отводят с верха аппарата. Осуществляют боковой отбор части диметилового эфира, обогащенного примесями, из нижней части верхней ректификационной зоны в точке бокового отбора, соответствующей 1-10 теоретической тарелке (счет с низа указанной ректификационной зоны). Технический результат: повышение качества целевого продукта. 1 з.п. ф-лы, 3 ил.
Предлагаемое изобретение относится к области получения диметилового эфира, который находит применение в качестве хладоагента, экстрагента, как компонент дизельного топлива, бытовых и косметических средств.
Известно, что диметиловый эфир (ДМЭ) высокой чистоты является отличным пропеллентом, широко используемым в аэрозольных упаковках. Обязательным требованием для диметилового эфира, используемого в бытовых и косметических аэрозолях, является его высокая концентрация (выше 99,99%), присутствие метанола не более 0,0001% и в определенных случаях отсутствие любого постороннего запаха.
В настоящее время основным источником диметилового эфира являются производства метанола из синтез-газа, где диметиловый эфир образуется как побочный продукт в количестве 2-5% мас. Такие процессы описаны в патентах DE 2362944, DE 2757788 и DE 3220547.
Процессы очистки ДМЭ от метанола, воды и примесей путем ректификации описаны в патентах ЕР-А 0124078, ЕР-А 0270852, US 4802956, US 5037511.
Отсутствие постороннего запаха в очищенном ДМЭ является основным показателем его качества при использовании в изготовлении, например, косметических средств. Существует ряд примесей, присутствующих в ДМЭ на уровне одной десятитысячной процента, но придающих непригодный запах очищенному эфиру. Эти примеси имеют температуры кипения, близкие к температуре кипения ДМЭ, что в значительной степени затрудняет их отделение ректификацией. Так, в патенте US 5037511 отмечено присутствие в неочищенном ДМЭ таких примесей, как метилформиат, углеводороды, карбоновые кислоты, сложные эфиры, амиды, ацетали и др.
Известно достаточно много процессов, в которых диметиловый эфир получают дегидратацией метанола с использованием различных катализаторов. Согласно патенту DE 680328 алифатические эфиры получены путем нагревания спиртов в присутствии хлористого цинка.
В патентах GB 322756, GB 350010, GB 403402, US 1873537 и FR 701335 заявлен целый ряд катализаторов для получения эфиров из спиртов, а именно составы на основе хлорного железа, хлористого олова, хлорида марганца, хлористого алюминия и сульфата алюминия, квасцов, окиси алюминия, окиси титана, окиси бария, кремнезема и фосфорнокислого алюминия.
Применение перечисленных выше катализаторов имеет целый ряд недостатков, основными из которых являются:
- низкая технологичность процесса, связанная с необходимостью частой замены, добавления или регенерации катализаторов;
- применение высоких температур и давлений;
- необходимость использования дорогостоящего оборудования, рассчитанного на работу в условиях высоких температур и давлений.
В патентах DE 2818831, DE 3201155, ЕР-А 0124078, ЕР-А 0099676 заявлены более технологичные катализаторы на основе модифицированной окиси алюминия, легированных или нелегированных алюмосиликатов. Так, в патенте DE 2818831 указан алюмосиликатный катализатор для получения диметилового эфира из метанола. В патенте US 5037511 описан способ, согласно которому чистый ДМЭ получают каталитической дегидратацией в отдельном реакторе при температуре 140-500°С и давлении 1-50 ата с последующим выделением ДМЭ ректификацией.
К недостаткам указанных выше способов следует отнести необходимость иметь в реакторах синтеза ДМЭ высокую температуру (до 500°С) и давление (до 50 ата), а также склонность катализаторов к коксообразованию при рабочих температурах.
Описан способ получения диметилового эфира в реакционно-ректификационном реакторе (статья «Получение диметилового эфира с использованием совмещенной хеморектификационной технологии» Химическая технология, №2, 2004, с.34-41). Согласно способу для дегидратации метанола в ДМЭ используют низкотемпературные катализаторы типа Amberlyst-15W, составы на основе Al2О3 и соединений меди. Максимальное давление в колонном аппарате заявлено 3500 мм рт. столба (4,6 ата), что соответствует температуре куба 145-148°С, реакционной зоны 105-109°С, верха - около 15°С. Общее число ступеней разделения, включая катализаторную зону, не превышает 20, а флегмовое число - 2,6. Верхом отводят целевой продукт концентрации 97% мол. (98% мас.). Указанный продукт предназначен к использованию в качестве моторного топлива.
Недостатком способа является низкая чистота получаемого ДМЭ, что ограничивает области его применения.
Наиболее близким к предлагаемому техническому решению является способ получения диметилового эфира из метанолсодержащего потока путем контактирования его с дегидратирующим катализатором (Заявка РФ №2002132017, опубл. 10.07.2004 г.). Способ осуществляют в реакционно-ректификационной системе, в которой реакционная зона соединена противоточными потоками жидкости и пара с исчерпывающей и укрепляющей ректификационными зонами. Метанолсодержащий поток подают в реакционную зону, и/или в верхнюю часть исчерпывающей ректификационной зоны, и/или в нижнюю часть укрепляющей ректификационной зоны. Сверху указанной укрепляющей зоны выводят поток, содержащий преимущественно ДМЭ, а снизу указанной исчерпывающей зоны выводят поток, содержащий преимущественно воду. В качестве катализатора используют сульфоионитный катализатор с размером частиц не менее 3 мм, предпочтительно имеющий форму цилиндров или массообменной насадки, в частности колец. Дегидратацию ведут при температуре от 100 до 160°С и поддерживают концентрацию воды в возвращаемом в реакционную(ые) зону(ы) метанольном потоке менее 12% мас, предпочтительно менее 5%.
Недостатком способа является, как и в описанном выше способе, низкое содержание ДМЭ (не выше 99,5%) при содержании метанола 0,5%. Кроме того, указанный способ предполагает двухреактороную схему для дегидратации (фиг.3 и 4), выделенный поток диметилового эфира предполагается подвергать водной отмывке от метанола и водно-метанольную смесь подавать в зону ректификации от воды и/или в исчерпывающую ректификационную зону реакционно-ректификационной системы (п.13). Кубовый продукт реакционно-ректификационного аппарата, содержащий до 5-12% мас. метанола, потребует выделения из него метанола, что также приведет к усложнению технологической схемы.
Задачей настоящего изобретения является повышение качества ДМЭ, что позволит расширить область его использования: от моторных топлив до косметических средств. В последнем случае к ДМЭ предъявляются повышенные требования как по чистоте (выше 99,99%), так и по отсутствию посторонних непригодных запахов. Особенно жестко регламентируется содержание метанола - менее 0,0001%. Кроме того, достигается упрощение технологии при одновременном сохранении высокого качества целевого продукта.
Указанный результат достигается способом получения диметилового эфира высокой чистоты дегидратацией метанола в присутствии сульфоионитного катализатора при повышенной температуре и давлении в совмещенном реакционно-ректификационном аппарате, состоящем из трех зон: двух ректификационных и средней - реакционной, заполненной катализатором, и выводом целевого эфира сверху совмещенного реактора, согласно которому дегидратацию осуществляют с боковым отбором части диметилового эфира, обогащенной примесями, из нижней части верхней ректификационной зоны с 1-10 теоретической тарелки (счет с низа указанной ректификационной зоны), лучше с 3-5 теоретической тарелки.
На фиг.1 представлен концентрационный профиль реакционно-ректификационного аппарата по примесям. Для получения ДМЭ использовался метанол концентрации 99,96%, содержание «легких» примесей - 0,007773%, «тяжелых» - 0,001685%, воды - 0,03%. Результаты обследования концентрационного профиля реакционно-ректификационного аппарата указывают на концентрирование так называемых «легких» примесей, кипящих в интервале температур выше температуры кипения ДМЭ и ниже температуры кипения метанола, в нижней части верхней ректификационной зоны. «Тяжелые» примеси, выкипающие выше температуры кипения метанола, концентрируются в области, принадлежащей реакционной (катализаторной) зоне. Данные по распределению примесей по высоте реакционно-ректификационного аппарата позволяют определиться с позициями для вывода накапливающихся примесей, чтобы избежать их поступления в отбираемый ДМЭ и таким образом обеспечить его высокую чистоту и отсутствие запаха.
Заявляемый способ поясняется вариантом технологической схемы, представленной на фиг.2.
Исходный метанол подогревается в теплообменнике 1 и подается в аппарат 2. Реакционно-ректификационный аппарат 2 включает три зоны:
- верхнюю ректификационную зону для отделения диметилового эфира от метанола;
- среднюю реакционную зону, заполненную катализатором;
- нижнюю ректификационную зону для отделения метанола от образующейся в результате реакции воды.
В аппарате 2 происходит синтез диметилового эфира и выделение продуктов. С верха аппарата выводятся пары чистого ДМЭ, которые конденсируются в конденсаторе 3. Конденсат частично возвращается в аппарат 2 в качестве флегмы, а балансовый избыток выводится на склад. Боковой отбор части ДМЭ, обогащенной примесями, содержащимися в метаноле и образующимися в процессе, осуществляют по линии 4. Из куба аппарата 2 отбирается вода. Реакционно-ректификационный аппарат обогревается через выносной кипятильник 5.
Подача метанола осуществляется либо под слой катализатора, либо в верхнюю часть нижней ректификационной зоны.
Возможно размещение реакционной и ректификационных зон как внутри одного колонного аппарата, так и раздельно в двух или трех аппаратах таким образом, что в них совокупно осуществляется единый реакционно-ректификационный процесс.
Предлагаемый способ иллюстрируется следующими примерами.
Пример 1.
Синтез диметилового эфира проводился в непрерывном режиме в реакционно-ректификационном аппарате, выполненном в виде царговой колонны. Колонна состояла из 6 царг внутренним диаметром 32 мм и была снабжена обогреваемым кубом и дефлегматором. Две нижние и две верхние царги были заполнены нерегулярной насадкой в виде спирали диаметром 2 мм, выполненной из нихромовой проволоки. Эффективность каждой царги составляла около 10 теоретических тарелок. Две средние царги были заполнены катализатором КИФ, который является продуктом сульфирования формованной смеси полиэтилена и сополимера стирола с дивинилбензолом, взятых в соотношении 30 к 70. Катализатор был изготовлен в виде цилиндров диаметром 2 мм и длиной 2÷5 мм.
Количество загруженного катализатора - 250 мл. Количество подаваемого метанола определялось по наступлению состояния равновесия в колонне, не допуская его вывода с кубовым продуктом.
Метанол в количестве 60 мл/ч подавался в нижнюю часть третьей царги (счет от куба). Синтез проводился при следующих условиях:
- давление верха - 8,7 ата;
- температура верха - 39°С;
- температура слоев катализатора - 133÷127°С;
- температура куба - 174°С.
С верха колонны отбирался чистый диметиловый эфир с концентрацией основного вещества более 99,99% мас., содержанием метанола менее 0,0001% мас. в количестве 41,6 мл/ч. Из куба колонны отбиралась вода в количестве 13,5 мл/ч. Из нижней части шестой царги (счет с куба) осуществлялся боковой отбор ДМЭ, обогащенного нежелательными примесями. Количество отбора составляло 10 мл/ч. Боковой отбор содержал следующие примеси (% мас.): ацетон - 0,00126; метилэтилкетон - 0,00070; метанол - 0,0010; метилизопропилкетон - 0,00040; этанол - 0,00017.
Срок службы катализатора около 5000 часов.
Пример 2.
Синтез диметилового эфира проводился в реакционно-ректификационной системе, описанной в примере 1. В качестве катализатора использовался сульфокатионит Amberlyst-15. Количество загруженного катализатора - 250 мл.
Метанол в количестве 60 мл/ч подавался в нижнюю часть второй царги (счет от куба). Синтез проводился при следующих условиях:
- давление верха - 8,7 ата;
- температура верха - 39°С;
- температура слоев катализатора -133÷127°С;
- температура куба -174°С.
С верха колонны отбирался диметиловый эфир с концентрацией основного вещества более 99,99% мас. и отсутствием постороннего запаха (содержание метанола менее 0,0001% мас.) в количестве 41,6 мл/ч. Из куба колонны отбиралась вода в количестве 13,5 мл/ч. Из нижней части шестой царги (счет с куба) осуществлялся боковой отбор ДМЭ, обогащенного нежелательными примесями. Точка бокового отбора соответствовала десятой теоретической тарелке верхней ректификационной зоны. Количество отбора составляло 10 мл/ч. Боковой отбор содержал следующие примеси, % мас.: ацетон - 0,00128; метилэтилкетон - 0,00065; метанол - 0,0098; метилизопропилкетон - 0,00039; этанол - 0,00018.
Срок службы катализатора около 5000 часов.
Пример 3.
Синтез диметилового эфира проводился в реакционно-ректификационной системе, описанной в примере 1. В качестве катализатора использовался сульфокатионит Amberlyst - 15. Количество загруженного катионита - 250 мл.
Метанол в количестве 40 мл/ч подавался в верхнюю часть второй царги (счет от куба). Синтез проводился при следующих условиях:
- давление верха - 4,9-5,0 ата;
- температура верха - 20°С;
- температура слоев катализатора -115÷110°С;
- температура куба - 157°С.
С верха колонны отбирался диметиловый эфир с концентрацией основного вещества более 99,99% мас., содержанием метанола менее 0,0001% мас. в количестве 29,4 мл/ч. Из куба колонны отбиралась вода в количестве 9 мл/ч. Из нижней части пятой царги (счет с куба) осуществлялся боковой отбор ДМЭ, обогащенного нежелательными примесями. Точка бокового отбора соответствовала первой теоретической тарелке верхней ректификационной зоны. Количество отбора составляло 5 мл/ч. Боковой отбор содержал следующие примеси, % мас.: ацетон - 0,00214; метилэтилкетон - 0,00126; метанол - 1,58; метилизопропилкетон - 0,00097; танол - 0,00032.
Срок службы катализатора около 5000 часов.
Пример 4.
Синтез диметилового эфира проводился в реакционно-ректификационной системе, размещенной в трех отдельных аппаратах, соединенных так, что они составляли единую реакционно-ректификационную систему. Технологическая схема представлена на фиг.3. Каждый из аппаратов состоял из двух царг. Два аппарата (1 и 3) использовались в качестве нижней и верхней ректификационных зон и были заполнены нерегулярной насадкой в виде спирали диаметром 2 мм, выполненной из нихромовой проволоки. Третий аппарат (2) использовался в качестве реакционной зоны. В качестве катализатора использовался сульфокатионит Purolite С-275. Количество загруженного катионита - 250 мл.
Метанол в количестве 70 мл/ч подавался в среднюю часть второй царги (счет от куба). Синтез проводился при следующих условиях:
- давление верха - 13,2 ата;
- температура верха - 50°С;
- температура слоев катализатора -140÷150°С;
- температура куба - 190-192°С.
С верха колонны отбирался чистый диметиловый эфир с концентрацией основного вещества более 99,99% мас., содержанием метанола менее 0,0001% мас. в количестве 61 мл/ч. Из куба колонны отбиралась вода в количестве 16 мл/ч. Из средней части пятой царги (счет с куба) осуществлялся боковой отбор ДМЭ, обогащенного нежелательными примесями. Точка бокового отбора соответствовала четвертой теоретической тарелке верхней ректификационной зоны. Количество отбора составляло 7 мл/ч. Боковой отбор содержал следующие примеси, % мас.: ацетон - 0,00263; метилэтилкетон - 0,001264; метанол - 0,0687; метилизопропилкетон - 0,00042; этанол - 0,00022.
Срок службы катализатора около 3000 часов.
Как видно из приведенных примеров, заявленные условия проведения процесса позволяют получать ДМЭ высокой концентрации 99,99% и выше и без постороннего непригодного запаха (содержание метанола менее 0,0001% мас.), что значительно расширяет области применения ДМЭ, по более простой технологии.
Следует также отметить, что использование в процессе крупногранулированного сульфоионитного формованного катализатора позволит легко реализовать процесс в промышленном масштабе.
1. Способ получения диметилового эфира высокой чистоты дегидратацией метанола в присутствии сульфоионитного катализатора при повышенных температуре и давлении в совмещенном реакционно-ректификационном аппарате, состоящем из трех зон: двух ректификационных и средней реакционной, заполненной катализатором, и выводом целевого эфира сверху аппарата с подачей метанола или в катализаторную зону, или в нижнюю ректификационную зону, при этом возможно размещение реакционной и ректификационной зон как внутри одного аппарата, так и раздельно в двух или трех аппаратах таким образом, что в них совокупно осуществляют единый реакционно-ректификационный процесс, отличающийся тем, что дегидратацию осуществляют при температуре 110-150°С, давлении 4,9-13,2 ата при боковом отборе части диметилового эфира, обогащенного примесями, из нижней части верхней ректификационной зоны в точке бокового отбора, соответствующей 1-10 теоретическим тарелкам (счет с низа указанной ректификационной зоны).
2. Способ по п.1, отличающийся тем, что боковой отбор проводят в точке бокового отбора, соответствующей 3-5 теоретическим тарелкам.
www.findpatent.ru
Способ производства диметилового эфира
Изобретение относится к способу получения диметилового эфира из синтез-газа и может быть использовано в нефтехимической промышленности.
Сущность: проводят каталитическую конверсию последовательно синтез-газа в реакторе(ах) синтеза метанола и продуктов синтеза в реакторе(ах) дегидратации метанола. Полученную жидкую фазу, содержащую метанол, диметиловый эфир и воду, подвергают разделению на двух ступенях дистилляции с получением на первой диметилового эфира и смеси метанол-вода, на второй метанола. Смесь метанол-вода разделяют на два потока, один из которых используют в качестве абсорбента при промывке продувочного газа, второй подают на вторую ступень дистилляции. Газовая фаза содержит непревращенный синтез-газ и диметиловый эфир. Часть газовой фазы смешивают с исходным синтез-газом, часть - продувочный газ - промывают от диметилового эфира. Абсорбент, обогащенный диметиловым эфиром, подают на первую ступень дистилляции. Метанол второй ступени дистилляции возвращают в цикл между реактором(ами) синтеза метанола и реактором(ами) дегидратации метанола. Предпочтительно абсорбент при промывке продувочного газа используют в количестве 20-100 мас.% от жидкой фазы.
Способ позволяет повысить степень превращения синтез-газа в диметиловый эфир, снизить содержание диметилового эфира в продувочном газе, упростить технологическую схему процесса. 1 з.п. ф-лы, 1 ил., 3 табл.
Изобретение относится к области химической технологии, в частности к способу получения диметилового эфира (ДМЭ) конверсией синтез-газа. ДМЭ имеет широкое применение при синтезе различных продуктов, а также при получении топлив, в частности при производстве высокооктанового бензина. Данная технология получения ДМЭ может быть применена в различных технологических линиях, в частности на заводах, производящих метанол.
Известен способ производства диметилового эфира (ЕР 1026141, А1, 2001), в котором используется синтез-газ, состоящий из водорода и оксидов углерода.
Синтез осуществляют по циркуляционной схеме в двух последовательных реакторах. Первый загружен катализатором синтеза метанола, а второй - катализатором дегидратации метанола.
Выделение жидкой смеси, состоящей из смеси метанола, диметилового эфира и воды, проводят после конденсации в сепараторе, из которого смесь подают на ректификацию с получением диметилового эфира и метанола. Часть полученного в результате сепарации газа циркулируют на смешение с исходным синтез-газом.
Для поддержания высокого парциального давления реагирующих компонентов в циркуляционном газе часть его выводят из цикла синтеза в виде продувочного газа, содержащего диметиловый эфир.
Известный способ не позволяет добиться максимальной производительности по диметиловому эфиру, т.к. значительная часть его выводится из цикла синтеза с продувочным газом, а полученный метанол после первой ступени не превращается полностью в диметиловый эфир.
Наиболее близким к изобретению по технической сущности является способ, описанный в патенте (РФ 2144912, 2000). В данном способе каталитическую конверсию синтез-газа осуществляют путем синтеза метанола и его дегидратации с получением диметилового эфира по циркуляционной схеме в нескольких реакторах, загруженных комбинированным катализатором для получения метанола/ДМЭ. Продукты конверсии направляют в рекуперативный теплообменник, конденсатор и сепаратор с получением жидкой фазы и газовой фазы - циркуляционного газа.
Для поддержания высокого парциального давления реагирующих компонентов в циркуляционном газе часть его выводят из цикла синтеза в виде продувочного газа, содержащего диметиловый эфир.
Жидкую фазу, содержащую метанол, воду и диметиловый эфир, подвергают двухступенчатой дистилляции. На первой ступени выделяют диметиловый эфир, а на второй разделяют смесь метанол-вода. Выделенный из водно-метанольной смеси метанол используют для промывки продувочного газа в абсорбере с целью утилизации имеющегося в нем диметилового эфира. Смесь метанол-диметиловый эфир подают в отдельно стоящий дополнительный реактор - реактор дегидратации метанола, с получением дополнительного количества диметилового эфира. В результате процесса получают эфир в смеси с метанолом (до 20%) и водой (до 20%).
К недостаткам указанного способа применительно к производству диметилового эфира следует отнести:
- сложность процесса регулирования процесса очистки продувочного газа от диметилового эфира вследствие ограниченного количества получаемого в результате второй ступени дистилляции метанола, используемого в качестве абсорбента;
- необходимость использования дополнительного реактора дегидратации, что приводит к повышенным затратам;
- невозможность полного превращения метанола в диметиловый эфир вследствие дегидратации из-за обратимости реакции дегидратации;
- неэффективное использование катализатора и оборудования реактора дегидратации вследствие уменьшения степени превращения метанола за счет содержания диметилового эфира в смеси, поступающей в реактор дегидратации из абсорбера.
Технической задачей данного изобретения является создание более эффективного процесса получения диметилового эфира, в котором:
- степень превращения оксидов углерода в диметиловый эфир достигает максимального значения;
- достигается максимальный выход диметилового эфира, так как полученный в установке метанол полностью продегидратирован;
- потери диметилового эфира с продувочным газом сведены к минимуму.
- упрощена технологическая схема проведения способа.
Поставленная задача достигается описываемым способом получения диметилового эфира, включающим проведение каталитической конверсии синтез-газа в метанол и дегидратацию метанола в реакторах, охлаждение образовавшихся продуктов с получением жидкой фазы, содержащей метанол, диметиловый эфир и воду, и газовой фазы, содержащей непревращенный синтез-газ и диметиловый эфир, разделение жидкой фазы на первой ступени дистилляции с получением диметилового эфира и смеси метанол-вода, направление смеси метанол-вода на вторую ступень дистилляции с получением метанола, возвращаемого в цикл, направление одной части газовой фазы на смешение с исходным синтез-газом, другой части - продувочного газа - на промывку от диметилового эфира с использованием абсорбента и получением абсорбента, обогащенного диметиловьм эфиром, при котором проводят последовательно каталитическую конверсию синтез-газа в реакторе(ах) синтеза метанола и затем продуктов синтеза в реакторе(ах) дегидратации метанола, смесь метанол-вода первой ступени дистилляции перед направлением на вторую ступень дистилляции предварительно разделяют на два потока, один из которых используют в качестве абсорбента при промывке продувочного газа, абсорбент, обогащенный диметиловым эфиром, подают на первую ступень дистилляции и метанол второй ступени дистилляции возвращают в цикл между реактором(ами) синтеза метанола и реактором(ами) дегидратации метанола. Предпочтительно абсорбент при промывке продувочного газа используют в количестве 20-100 мас.% от жидкой фазы.
Способ получения диметилового эфира проводят следующим образом.
Синтез-газ направляют в реактор(ы) синтеза метанола. При синтезе метанола возможно использовать различные общеизвестные катализаторы синтеза метанола, такие как катализаторы на основе оксидов меди, цинка, хрома, в частности низкотемпературный медьсодержащий катализатор.
Продукты синтеза направляют в реактор(ы) дегидратации метанола. При дегидратации метанола возможно использовать различные общеизвестные катализаторы дегидратации метанола, в частности катализаторы на основе окиси алюминия, алюмосиликатов.
При проведении синтеза метанола и его дегидратации применимы различные типы реакторов, в том числе реакторы с фиксированным или псевдоожиженным слоями катализаторов, возможно использовать один реактор или систему реакторов.
Далее проводят охлаждение образовавшихся продуктов с получением жидкой и газовой фаз. Жидкую фазу, содержащую метанол, диметиловый эфир и воду, подвергают разделению на первой ступени дистилляции с получением диметилового эфира и смеси метанол-вода. Газовая фаза содержит непревращенный синтез-газ и часть полученного диметилового эфира. Часть газовой фазы направляют на смешение с исходным синтез-газом, другую часть - продувочный газ - направляют на промывку от диметилового эфира с использованием абсорбента. При этом получают абсорбент, обогащенный диметиловым эфиром. Указанный абсорбент подают на первую ступень дистилляции. Смесь метанол-вода разделяют на два потока, один из которых используют в качестве абсорбента при промывке продувочного газа, второй направляют на вторую ступень дистилляции с получением метанола.
На ступенях дистилляции возможно использовать различные схемы разделения, в том числе, например, с использованием ректификационных колонн.
Метанол второй ступени дистилляции возвращают в цикл между реактором(ами) синтеза метанола и реактором(ами) дегидратации метанола. Указанный метанол возможно направлять на реакцию дегидратации различным образом, например смешать с продуктами синтеза метанола, направляемыми в реактор (в систему реакторов) дегидратации метанола, ввести непосредственно в реактор (в систему реакторов) и другими путями.
Предпочтительно абсорбент при промывке продувочного газа используют в количестве 20-100 мас.% от жидкой фазы.
На чертеже представлена принципиальная схема проведения способа.
Поток 1 свежего синтез-газа подают в цикл синтеза, где смешивают с потоком 2 циркуляционного газа (содержащего в основном непревращенный синтез-газ и ДМЭ) и после нагрева в рекуперативном теплообменнике 3 объединенный поток 4 подают в реактор синтеза метанола 5, где на низкотемпературном медьсодержащем катализаторе происходит синтез метанола по реакциям (I, II).
В горячий поток 6, после реактора синтеза метанола 5, впрыскивают жидкий поток 7 метанола, полученного на второй ступени дистилляции. Смесь потоков 6 и 7 подают в реактор дегидратации 8, содержащий неподвижный слой катализатора на основе окиси алюминия, где происходит образование диметилового эфира по реакции (III).
Поток 9, выходящий из реактора 8, проходит рекуперативный холодильник 3, холодильник-конденсатор 10, где происходит отделение жидкой фазы, поток 11, от газовой фазы - сухого циркуляционного газа, поток 12. После отвода продувочного газа, поток 13, оставшийся поток 2 направляют на смешение с потоком 1 свежего синтез-газа. Продувочный газ, поток 13, направляют на очистку от диметилового эфира в абсорбере 14, в котором в качестве абсорбента используют смесь метанол-вода, поток 15. Расход абсорбента регулируют таким образом, чтобы обеспечить максимальную очистку продувочного газа от диметилового эфира. Обогащенный ДМЭ абсорбент - смесь метанол - вода - ДМЭ, поток 16, после очистки продувочного газа смешивают с конденсатом, поток 11. Затем смесь направляют на первую ступень дистилляции 17. Полученный при перегонке диметиловый эфир, поток 18, с чистотой более 99%, является целевым продуктом. Кубовый остаток перегонки (смесь метанол-вода) разделяют на два потока. Первый из них, поток 15, используют в качестве абсорбента для очистки продувочного газа, а второй, поток 19, направляют на вторую стадию дистилляции 20, в результате которой получают обезвоженный метанол, поток 7. Этот поток возвращают на переработку в цикл получения ДМЭ после реактора синтеза метанола 5 перед дегидратацией метанола до диметилового эфира в реакторе 8. Продувочный газ отводят по линии 21.
Обеспечение глубокой очистки продувочного газа от остатков диметилового эфира достигают варьированием количества рециркулируемой смеси метанол-вода.
Изобретение иллюстрируется следующими примерами.
Результаты, полученные в примерах, приведены ниже в таблицах. Номера потоков в таблицах соответствуют позициям, приведенным на чертеже.
Пример 1 (таблица 1).
Свежий синтез-газ (поток 1) под давлением 8,5 МПа в количестве 5902 нм3/час подают в цикл синтеза, где смешивают с потоком циркуляционного газа (поток 2), содержащим, в том числе, 2,5% ДМЭ и 0,07% метанола, в количестве 14991 нм3/час. После нагрева в рекуперативном теплообменнике 3 до температуры 190-210°С эту смесь (поток 4) подают в реактор синтеза метанола 5, где на низкотемпературном катализаторе медьсодержащем катализаторе происходит синтез метанола. Температура на выходе из реактора синтеза составляет 265-280°С, содержание метанола 3,66% и 1,92% ДМЭ. В горячий циркуляционный газ (поток 6) после реактора синтеза метанола впрыскивают 270 кг/час метанола-ректификата (поток 7), полученного после второй ступени дистилляции. С температурой 260-265°С эту смесь подают в реактор дегидратации 8, где происходит образование диметилового эфира. Концентрация ДМЭ на выходе из реактора увеличивается до 3,68%, а метанола снижается до 1,03%. После рекуперативного холодильника полученную смесь (поток 9) охлаждают в холодильнике - конденсаторе 10. Далее проводят отделение жидкой фазы из циркуляционного газа. Жидкая фаза - конденсат (поток 11) в количестве 1404 кг/час, содержит ДМЭ 38,34 мас.%, метанола 19,23 мас.% и воды 40,81 мас.%. Сухой циркуляционный газ (поток 12) с содержанием метанола 0,07% и 2,5% ДМЭ разделяют на два потока - 2 и 13. Поток 2 направляют на смешение со свежим синтез-газом. Поток 13, как продувочный газ, в количестве 3506 нм3/час направляют на очистку от диметилового эфира в абсорбере 14, в котором в качестве абсорбента используют смесь метанол-вода (поток 15) с расходом 571 кг/час, содержанием ДМЭ 0,84 мас.%, метанола 31,75 мас.% и воды 67,41 мас.%. Абсорбент на выходе (поток 16) в количестве 742 кг/час содержит ДМЭ 23,70 мас.%, метанола 24,43 мас.% и воды 51,87 мас.%, при этом абсорбент поглощает 171 кг/час ДМЭ. Это количество соответствует степени очистки продувочного газа от диметилового эфира 95%. Продувочный газ после абсорбера (поток 21) в количестве 3422 нм3/час содержит 0,13% ДМЭ. Поток 16 смешивают с конденсатом (поток 11) и подают на первую ступень дистилляции 17, где происходит отгон диметилового эфира. Полученный диметиловый эфир (поток 18) в количестве 683 кг/час с чистотой 99.51% является целевым продуктом. Кубовый остаток - смесь метанол-вода, разделяют на два потока. Первый из них, поток 15, в количестве 571 кг/час используют в качестве абсорбента для очистки продувочного газа, а второй, поток 19, в количестве 850 кг/час направляют на вторую ступень дистилляции 20. Поток 15 составляет от потока 11 40,7%. Обезвоженный метанол-ректификат (поток 7) в количестве 270 кг/час после второй ступени дистилляции возвращают на переработку в цикл синтеза.
Пример 2 (таблица 2).
Пример 2 отличается от примера 1 параметрами стадий абсорбции и дистилляции. Продувочный газ (поток 13), в количестве 3506 нм3/час направляют на очистку от диметилового эфира в абсорбере 14, в котором в качестве абсорбента используют смесь метанол-вода (поток 15) с расходом 287 кг/час, содержанием ДМЭ 0,84 мас.%, метанола 31,75 мас.% и воды 67,41 мас.%. Абсорбент на выходе (поток 16) в количестве 422 кг/час содержит ДМЭ 32,56 мас.%, метанола 21,60 мас.% и воды 45,85 мас.%, при этом абсорбент поглощает 135 кг/час ДМЭ. Это количество соответствует степени очистки продувочного газа от диметилового эфира 75%. Продувочный газ после абсорбера (поток 21) в количестве 3440 кг/час содержит 0,64% ДМЭ. Поток 10 смешивают с конденсатом (поток 11) и подают на первую ступень дистилляции 17, где происходит отгон диметилового эфира. Полученный отгонкой диметиловый эфир (поток 18) в количестве 648 кг/час с чистотой 99,50% является целевым продуктом. Кубовый остаток - смесь метанол-вода разделяют на два потока. Первый из них, поток 15, в количестве 287 кг/час используют в качестве абсорбента для очистки продувочного газа, а второй, поток 19, в количестве 850 кг/час направляют на вторую ступень дистилляции 20. Поток 15 составляет от потока 11 20,4%. Обезвоженный метанол (поток 7) в количестве 270 кг/час после второй ступени дистилляции возвращают на переработку в цикл процесса.
Пример 3 (таблица 3).
Пример 3 отличается от примера 1 и 2 параметрами стадий абсорбции и дистилляции.
Продувочный газ (поток 13), в количестве 3506 нм3/час направляют на очистку от диметилового эфира в абсорбере 14, в котором в качестве абсорбента используют смесь метанол-вода (поток 15) с расходом 1198 кг/час, с содержанием ДМЭ 0,84 мас.%, метанола 31,75 мас.% и воды 67,41 мас.%. Абсорбент на выходе (поток 16) в количестве 1399 кг/час содержит ДМЭ 13,52 мас.%, метанола 27,19 мас.% и воды 57,74 мас.%, при этом абсорбент поглощает 179,1 кг/час ДМЭ. Это количество соответствует степени очистки продувочного газа от диметилового эфира 99,5%. Продувочный газ после абсорбера (поток 21) в количестве 3419 кг/час содержит 0,01% ДМЭ. Поток 10 смешивают с конденсатом (поток 11) и подают на первую ступень дистилляции 17. Полученный при перегонке диметиловый эфир (поток 18) в количестве 689 кг/час с чистотой 99,52% является целевым продуктом. Кубовый остаток перегонки - смесь метанол-вода, разделяют на два потока. Первый из них, поток 15, в количестве 287 кг/час используют в качестве абсорбента для очистки продувочного газа, а второй, поток 19, в количестве 850 кг/час направляют на вторую ступень дистилляции 20. Поток 15 составляет от потока 11 85,3%. Обезвоженный метанол (поток 7) в количестве 270 кг/час после второй ступени дистилляции возвращают на переработку в цикл процесса.
Как видно из примеров и данных таблиц в описываемом процессе:
- диметиловый эфир является одним целевым продуктом с концентрацией 99,51 мас.%, метанол - как побочный продукт полностью отсутствует, за счет чего повышается выход целевого продукта;
- потери диметилового эфира с продувочным газом сведены к минимуму, содержание диметилового эфира в продувочном газе достигает 0,01 об.%, что также приводит к повышению выхода целевого продукта;
- способ проводят по более простой технологической схеме.
ПРИМЕР 1
ТАБЛИЦА 1 | ||||||||||||||
№ потока | 1 | 2 | 3 | 4 | 5 | 6 | 7 | 8 | 9 | 10 | 11 | 12 | 13 | 14 |
Состав, об.% | мас.% | мас.% | мас.% | мас.% | мас.% | об.% | ||||||||
Диоксид углерода | 13.42 | 11.87 | 12.31 | 11.32 | 11.21 | 11.87 | 11.87 | 1.50 | 0.49 | 12.16 | ||||
Оксид углерода | 8.68 | 4.98 | 6.02 | 4.72 | 4.68 | 4.97 | 4.97 | 0.02 | 0.00 | 5.10 | ||||
Водород | 59.84 | 50.17 | 59.90 | 47.63 | 47.18 | 50.17 | 50.17 | 0.01 | 0.00 | 51.39 | ||||
Азот | 8.00 | 13.46 | 11.920 | 12.78 | 12.65 | 13.46 | 13.46 | 0.04 | 0.00 | 13.78 | ||||
Аргон | 2.27 | 3.82 | 3.38 | 3.62 | 3.59 | 3.82 | 3.82 | 0.03 | 0.00 | 3.91 | ||||
Метан | 7.79 | 13.09 | 11.59 | 12.43 | 12.31 | 13-09 | 13.09 | 0.05 | 0.00 | 13.41 | ||||
Вода | 0.00 | 0.06 | 0.04 | 1.92 | 3.68 | 0.06 | 0.06 | 40.81 | 51.87 | 67.41 | 67.41 | 0.00 | 0.06 | |
Метанол | 0.00 | 0.07 | 0.05 | 3.66 | 100.00 | 1.03 | 0.07 | 0.07 | 19.23 | 24.43 | 31.75 | 31.75 | 0.00 | 0.07 |
Диметиловый эфир | 0.00 | 2.50 | 1.79 | 1.92 | 3.68 | 2.50 | 2.50 | 38.34 | 23.70 | 0.84 | 0.84 | 99.51 | 0.13 | |
Расход | 5902 нм3/ч | 14991 нм3/ч | 20893 нм3/ч | 19487 нм3/ч | 270 кг/ч | 19674 нм3/ч | 18497 нм3/ч | 3506 нм3/ч | 1404 кг/ч | 742 кг/ч | 571 кг/ч | 850 кг/ч | 683 кг/ч | 3422 нм3/ч |
Давление, МПа | 8.5 | 8.5 | 8.4 | 8.4 | 8.4 | 8.4 | 8.3 | 8.3 | 1.2 | 1.2 | 1.2 | 1.2 | 1.2 | 1.2 |
ПРИМЕР 2
ТАБЛИЦА 2 | ||||||||||||||
№ потока | 1 | 2 | 3 | 4 | 5 | 6 | 7 | 8 | 9 | 10 | 11 | 12 | 13 | 14 |
Состав, об.% | мас.% | мас.% | мас.% | мас.% | мас.% | об.% | ||||||||
Диоксид углерода | 13.42 | 11.87 | 12.31 | 11.32 | 11.21 | 11.87 | 11.87 | 1.50 | 0.50 | 12.09 | ||||
Оксид углерода | 8.68 | 4.98 | 6.02 | 4.72 | 4.68 | 4.97 | 4.97 | 0.02 | 0.00 | 5.07 | ||||
Водород | 59.84 | 50.17 | 59.90 | 47.63 | 47.18 | 50.17 | 50.17 | 0.01 | 0.00 | 51.13 | ||||
Азот | 8.00 | 13.46 | 11.920 | 12.78 | 12.65 | 13.46 | 13.46 | 0.04 | 0.00 | 13.71 | ||||
Аргон | 2.27 | 3.82 | 3.38 | 3.62 | 3.59 | 3.82 | 3.82 | 0.03 | 0.00 | 3.89 | ||||
Метан | 7.79 | 13.09 | 11.59 | 12.43 | 12.31 | 13.09 | 13.09 | 0.05 | 0.00 | 13.34 | ||||
Вода | 0.00 | 0.06 | 0.04 | 1.92 | 3.68 | 0.06 | 0.06 | 40.81 | 45.85 | 67.41 | 67.41 | 0.00 | 0.06 | |
Метанол | 0.00 | 0.07 | 0.05 | 3.66 | 100.00 | 1.03 | 0.07 | 0.07 | 19.23 | 21.60 | 31.75 | 31.75 | 0.00 | 0.07 |
Диметиловый эфир | 0.00 | 2.50 | 1.79 | 1.92 | 3.68 | 2.50 | 2.50 | 38.34 | 32.56 | 0.84 | 0.84 | 99.5 | 0.64 | |
Расход | 5902 нм3/ч | 14991 нм3/ч | 20893 нм3/ч | 19487 нм3/ч | 270 кг/ч | 19674 нм3/ч | 18497 нм3/ч | 3506 нм3/ч | 1404 кг/ч | 422 кг/ч | 287 кг/ч | 850 кг/ч | 648 кг/ч | 3440 нм3/ч |
Давление, МПа | 8.5 | 8.5 | 8.4 | 8.4 | 8.4 | 8.4 | 8.3 | 8.3 | 1.2 | 1.2 | 1.2 | 1.2 | 1.2 | 1.2 |
ПРИМЕР 3
ТАБЛИЦА 3 | ||||||||||||||
№ потока | 1 | 2 | 3 | 4 | 5 | 6 | 7 | 8 | 9 | 10 | 11 | 12 | 13 | 14 |
Состав, об.% | мас.% | мас.% | мас.% | мас.% | мас.% | об.% | ||||||||
Диоксид углерода | 13.42 | 11.87 | 12.31 | 11.32 | 11.21 | 11.87 | 11.87 | 1.50 | 0.48 | 12.17 | ||||
Оксид углерода | 8.68 | 4.98 | 6.02 | 4.72 | 4.68 | 4.97 | 4.97 | 0.02 | 0.00 | 5.10 | ||||
Водород | 59.84 | 50.17 | 59.90 | 47.63 | 47.18 | 50.17 | 50.17 | 0.01 | 0.00 | 51.45 | ||||
Азот | 8.00 | 13.46 | 11.920 | 12.78 | 12.65 | 13.46 | 13.46 | 0.04 | 0.00 | 13.80 | ||||
Аргон | 2.27 | 3.82 | 3.38 | 3.62 | 3.59 | 3.82 | 3.82 | 0.03 | 0.00 | 3.91 | ||||
Метан | 7.79 | 13.09 | 11.59 | 12.43 | 12.31 | 13.09 | 13.09 | 0.05 | 0.00 | 13.42 | ||||
Вода | 0.00 | 0.06 | 0.04 | 1.92 | 3.68 | 0.06 | 0.06 | 40.81 | 57.74 | 67.41 | 67.41 | 0.00 | 0.06 | |
Метанол | 0.00 | 0.07 | 0.05 | 3.66 | 100.00 | 1.03 | 0.07 | 0.07 | 19.23 | 27.19 | 31.75 | 31.75 | 0.00 | 0.07 |
Диметиловый эфир | 0.00 | 2.50 | 1.79 | 1.92 | 3.68 | 2.50 | 2.50 | 38.34 | 13.52 | 0.84 | 0.84 | 99.52 | 0.01 | |
Расход | 5902 нм3/ч | 14991 нм3/ч | 20893 нм3/ч | 19487 нм3/ч | 270 кг/ч | 19674 нм3/ч | 18497 нм3/ч | 3506 нм3/ч | 1404 кг/ч | 1399 кг/ч | 1198 кг/ч | 850 кг/ч | 689 кг/ч | 3419 нм3/ч |
Давление, МПа | 8.5 | 8.5 | 8.4 | 8.4 | 8.4 | 8.4 | 8.3 | 8.3 | 1.2 | 1.2 | 1.2 | 1.2 | 1.2 | 1.2 |
1. Способ производства диметилового эфира, включающий проведение каталитической конверсии синтез-газа в метанол и дегидратацию метанола в реакторах, охлаждение образовавшихся продуктов с получением жидкой фазы, содержащей метанол, диметиловый эфир и воду, и газовой фазы, содержащей непревращенный синтез-газ и диметиловый эфир, разделение жидкой фазы на первой ступени дистилляции с получением диметилового эфира и смеси метанол-вода, направление смеси метанол-вода на вторую ступень дистилляции с получением метанола, возвращаемого в цикл, направление одной части газовой фазы на смешение с исходным синтез-газом, другой части - продувочного газа на промывку от диметилового эфира с использованием абсорбента и получением абсорбента, обогащенного диметиловым эфиром, отличающийся тем, что проводят последовательно каталитическую конверсию синтез-газа в реакторе(ах) синтеза метанола и затем продуктов синтеза в реакторе(ах) дегидратации метанола, смесь метанол-вода первой ступени дистилляции перед направлением на вторую ступень дистилляции предварительно разделяют на два потока, один из которых используют в качестве абсорбента при промывке продувочного газа, абсорбент, обогащенный диметиловым эфиром, подают на первую ступень дистилляции, и метанол второй ступени дистилляции возвращают в цикл между реактором(ами) синтеза метанола и реактором(ами) дегидратации метанола.
2. Способ по п.1, отличающийся тем, что абсорбент при промывке продувочного газа используют в количестве 20-100 мас.% от жидкой фазы.
www.findpatent.ru
СПОСОБ ПОЛУЧЕНИЯ ДИМЕТИЛОВОГО ЭФИРА
Изобретение относится к способу получения диметилового эфира из синтез-газа и может быть использовано в нефтехимической промышленности.
Известен способ производства продукта, содержащего диметиловый эфир, метанол до 20% по массе и воды до 20% по массе, каталитической конверсией синтез-газа, включающей стадии: получения метанола в реакторе синтеза метанола и его дегидратации в реакторе синтеза диметилового эфира с последующим выделением смеси продуктов, который разделяют на жидкую и газовую фазы. Из жидкой фазы, содержащей диметиловый эфир, метанол и воду, выделяют диметиловый эфир, с последующим разделением жидкой фазы на метанол и воду, при этом метанол после отделения направляют в реактор синтеза диметилового эфира, а газовую фазу, содержащую непрореагировавший синтез-газ и несконденсированный диметиловый эфир, направляют в реактор синтеза метанола, RU Патент №2144912 МПК C07С 43/04 (2006.01), C07C 41/01 (2006.01), C07C 41/42 (2006.01), 2000.
Недостатками указанного способа являются сложность технологического процесса, необходимость использования дополнительного реактора синтеза диметилового эфира, низкий выход продукта в результате не полного превращения метанола в диметиловый эфир.
Известен способ производства диметилового эфира каталитической конверсией синтез-газа, содержащего двуокись углерода, азот, метан и др., включающий стадии получения метанола в реакторе синтеза метанола и дегидратацию метанола в реакторе синтеза диметилового эфира с получением смеси продуктов с последующим ее разделением на газовую и жидкую фазы. Из жидкой фазы, содержащей метанол, диметиловый эфир и воду, выделяют диметиловый эфир, после чего жидкую фазу разделяют на метанол и воду, метанол направляют в реактор синтеза диметилового эфира. Газовую фазу, содержащую непрореагировавший синтез-газ и диметиловый эфир, делят на два потока, один из которых рециркулируют в реактор синтеза метанола, а второй поток направляют в абсорбер для выделения диметилового эфира, см. RU Патент №2277528, МПК C07C 43/04 (2006.01), C07C 41/09 (2006.01), C07C 41/01 (2006.01), 2006.
Недостатком данного способа является сложность технологического процесса за счет наличия большого количества операций, необходимость использования дополнительного реактора и катализатора, приводящих к повышенным затратам.
Наиболее близким к изобретению является способ получения диметилового эфира каталитической конверсией синтез-газа, содержащего двуокись углерода, в реакторе синтеза диметилового эфира с получением смеси продуктов, содержащей диметиловый эфир, метанол, двуокись углерода и непрореагировавший синтез-газ, и последующей ее десорбцией водным раствором, обогащенным карбонатом калия, обедненную двуокисью углерода смесь продуктов подвергают разделению на газовую и жидкую фазы. Жидкую фазу, метанол и воду, направляют в реактор синтеза диметилового эфира, из газовой фазы путем конденсации выделяют целевой продукт - диметиловый эфир, а непрореагировавший синтез-газ и двуокись углерода газовой фазы направляют в реактор синтеза диметилового эфира, см. RU Патент №2469017, МПК C07C 43/04 (2006.01), C07C 41/09 (2006.01), C07C 31/04 (2006.01), C07C 29/151 (2006.01), 2012.
Недостатком данного способа является низкий выход диметилового эфира (33,21 об.%) вследствие наличия двуокиси углерода в синтез-газе и его накопления в смеси продуктов.
Задачей изобретения является создание способа, позволяющего повысить выход диметилового эфира.
Техническая задача решается способом получения диметилового эфира каталитической конверсией синтез-газа в реакторе синтеза диметилового эфира с получением смеси продуктов, содержащей диметиловый эфир, метанол, двуокись углерода и непрореагировавший синтез-газ, с последующим разделением смеси продуктов и получением целевого продукта конденсацией из газовой фазы, в котором каталитической конверсии подвергают синтез-газ, полученный паровой газификацией древесного угля, образующегося при пиролизе предварительно высушенных древесных отходов, а жидкую фазу после разделения смеси продуктов направляют в ректификационную колонну для отделения метанола, после чего метанол и очищенный от двуокиси углерода непрореагировавший синтез-газ направляют в реактор синтеза диметилового эфира.
Решение технологической задачи позволяет увеличить выход диметиловго эфира до 60 об.%.
Способ осуществляют следующим образом, см. фиг.1: древесные отходы поступают в камеру конвективной сушки 1, предварительно высушенные древесные отходы направляют шнековым транспортером 25 в камеру пиролиза 5, где происходит разложение древесных отходов на уголь и пиролизные газы. Пиролизные газы поступают в топку 20, полученные топочные газы подают в рубашку камеры пиролиза 5, далее топочные газы направляют на сушку древесных отходов в камеру конвективной сушки 1. С помощью дымососа 3, эжектора 4 и задвижки 2 организуется рециркуляция сушильного агента с заданной кратностью. Отработанные топочные газы отводятся в дымовую трубу 6. Древесный уголь из камеры пиролиза 5 шнековым транспортером 24 подается в камеру газогенерации 23, в которой подвергается паровой газификации за счет прохождения высокотемпературного перегретого пара через слои угля, в результате чего образуется синтез-газ и зола. Полученный синтез-газ, содержащий монооксид углерода 47-50 об.%, водород 44-47 об.% и золу 3-9 об.%, поступает в циклон 18 и фильтр 7 для очистки от золы и охлаждения, а зола удаляется с помощью шнекого транспортера 22. Очищенный и охлажденный синтез-газ газодувкой 8 накапливают в газгольдере 9. Газ смешивается с потоком непрореагировавшего синтез-газа и сжимается компрессором 10 до давления до 5 МПа и направляется в реактор синтеза диметилового эфира 11 для каталитической конверсии синтез-газа при температуре 250-300 °C. Выходящая из реактора синтеза диметилового эфира 11 смесь продуктов, содержит диметиловый эфир, метанол, двуокись углерода и непрореагировавший синтез-газ. Указанную смесь продуктов охлаждают и после дросселирования в устройстве 13 направляют в сепаратор 15, где подвергают разделению на газовую и жидкую фазы. Жидкая фаза, содержащая метанол и воду, поступает в ректификационную колонну 16, где происходит разделение на метанол и воду. Метанол рециркулируют в газгольдер 9, после чего направляют в реактор синтеза диметилового эфира 11. Воду из нижней части ректификационной колонны 16 используют для конденсации диметилового эфира и направляют в нагревательный элемент 19 в топке 20.
Целевой продукт - диметиловый эфир получают конденсацией из газовой фазы в поверхностном конденсаторе 14. Непрореагировавший синтез-газ и двуокись углерода газовой фазы поступает в конденсатор 12, где двуокись углерода за счет оборотного охлаждения хладоагентом конденсируется и поступает в теплообменник 17 для охлаждения смеси продуктов, после чего отводится в дымовую трубу 6, а очищенный от двуокиси углерода непрореагировавший синтез-газ рециркулируют в реактор синтеза диметилового эфира 11.
Вода, нагреваемая в рубашке 21 за счет теплообмена с золой, подается в нагревательный элемент 19 в топке 20, где испаряется, превращается в перегретый пар и подается в камеру газогенерации 23. Выход диметилового эфира составляет 58,65 - 59,89%.
Как видно из примера конкретного выполнения, заявляемый способ позволяет повысить выход диметилового эфира до 60 об.%.
Способ получения диметилового эфира каталитической конверсией синтез-газа в реакторе синтеза диметилового эфира с получением смеси продуктов, содержащей диметиловый эфир, метанол, двуокись углерода и непрореагировавший синтез-газ, с последующим ее разделением и получением целевого продукта конденсацией из газовой фазы, отличающийся тем, что каталитической конверсии подвергают синтез-газ, полученный паровой газификацией древесного угля, образующегося при пиролизе предварительно высушенных древесных отходов, а жидкую фазу после разделения смеси продуктов направляют в ректификационную колонну для отделения метанола, после чего метанол и очищенный от двуокиси углерода непрореагировавший синтез-газ газовой фазы направляют в реактор синтеза диметилового эфира.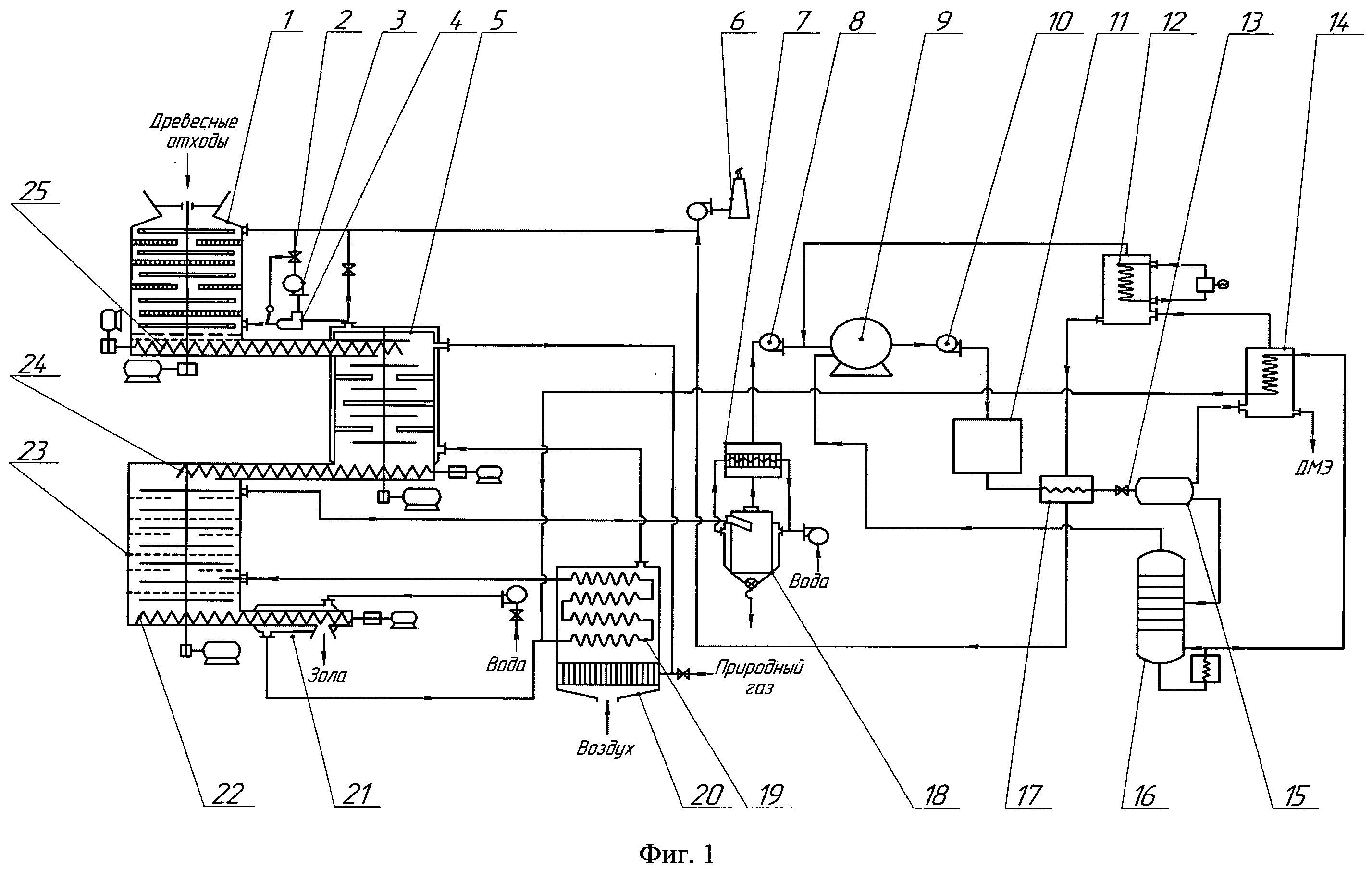
edrid.ru
Способ получения диметилового эфира
Ь = 0,1-10; с = 2,5,9-30; d = 11-15
1 = 10; х — число удовлетворяющее всем валентностям, Процесс ведут при
220-240 С, давлении 7000-1100 кПа и объемной скорости 2000-2500 ч .
Способ позволяет вести процесс при конверсии 58-69Х селективности 61,864,IX при меньшем нагревании, чем в известном случае (56-62Х и 6063,2Х при 260-330 С), при большей длительности работи катализатора (810 ч против 264 ч, т.е. когда конверсия снижается с 62 до 57X).1 табл, ! 3296 !4
Изобретение относится к усовершенствованному способу получения диметилового эфира, который находит применение в качестве растворителя, а также в качестне промежуточного соединения при получении полимеров, гербицидов и других продуктов органического синтеза.
Цель изобретения — упрощение процесса.
Пример I. В !О л воды растворяют 676 г Сы(МО ) 3Н О> 327 r
Zn(N0 )> (Н О и 57 г алюмината натрия. Раствор нагревают до 85 С и при перемешивании добавляют 10/-ный раствор йаОН в воде до тех пор, пока не установится рН 7,5.
Раствор охлаждают, выпавший осадок отделяют от жидкости декантацией. Осадок несколько раз промывают водой. При этом отделение жидкости осуществляют декантацией, а последний раз — фильтрованием.
Осадок сушат в ток» воздуха в печи при 120 С. Высушенный материал измельчают до получения частиц 20 меш
АЬТИ (0,84 мм). Размолотый материал смешивают с 325 г окиси кремния, модифицированной --окисью алюминия.
Полученный порошок прессуют в таблетки диаметром 4 мм и толщиной 6 мм.
Приготовленный таким образом катализатор содержит металлы при атомном соотношении Cu:Zn:ßI:Si= 28:ll:7:54.
100 r укаэанного катализатора помещают в трубчатый реактор диаметром
2,54 см, в середину которого аксиально помещают термопару в оболочке диаметром 8 мм. В реактор подают смесь Н и М и температуру постепенно увеличивают до 230 С. При этом происходит восстановление катализатора. Когда температура достигает
230 С, носстановление катализатора о прекращается.
В реакторе устанавливают давление
7000 КПа и смесь Н и и постепенно заменяют смесью СО и Н (молярное сой отношение 1: 1) и ведут процесс при объемной скорости подачи смеси 2100 ч
Полученную реакционную массу, содержащую воду, метанол и диметиловый эфир (ДМЭ), направляют в холодильник, расположенный на выходе из реактора, В холодильнике происходит конденсация воды, метанола и части
ДМЭ.
Газ из реактора отбирают через клапан для отбора проб и анализируют методом ГЖХ, затем газ направляют в суммирующий расходомер.
При коннерсии 697. достигается селективность превращения СО в ДМЭ
63,4Х, селективность по метанолу
З,OX по углекислому газу 33,6Х
Прочие продукты, образующиеся в количестве менее 17, не учитываются.
Пример 2. Приготовление катализатора и проведение процесса осуществляют аналогично примеру I.
Атомное соотношение Си 2п:Al Si=
28:ll:7:54, Скорость подачи сырья
250С.ч, молярное соотношение Н
СО = 2:1. При конверсии 60Х достигается селективность превращения СО в ДМЭ 63,07; селективность по метанолу 4,2Х; по углекислому газу 32,87., Пример 3. Приготовление катализатора и проведение процесса осуществляют аналогично прииеру 2.
Температура процесса 240 С, давление
9000 КПа, молярное соотношение Н>
СО = 3:l, При конверсии 617 достигается селективность превращения СО в ДИЭ
62,8Х; селективность по метанолу
3,5Х; по углекислому газу 33,77., Пример 4. Приготонление катализатора и проведение процесса осуществляют аналогично примеру 2, Скорость подачи сырья 2000 ч, молярное соотношение Н1 . СО = 1:I В качестве сырья используют синтезгаз, содержащий Н> 47Х; СО 477., СО 67.
При конверсии 587 достигается селективность превращения СО в ДМЭ
62,57.; селективность по метанолу
3,47.; селектинность по углекислому газу 34,IX, Пример 5. Приготовление катализатора и проведение процесса осуществляют аналогично примеру 1, Атомное соотношение Cu:Zn:Àl:S1 = 30:15:
:10:45, Давление 8000 кПа.
При конверсии 677 достигается селективность превращения СО в ДМЭ
62,6Х; селективность по метанолу 4,4Х; селектинность по углекислому газу 33.
Пример 6. Приготовление катализатора и проведение процесса осущес-.вляют аналогично примеру 5.
Атомное соотношение CU 2n:Àl:Si Cr — 25,9:14:0,1:50:10. Скорость подачи сырья 2000 ч, давление 11000 кПа, з
132961
Прн конверсии 59% достигается селективность превращения С0 в ЛМЭ
63,6Х; селективность по метанолу 3,5Х селективность по углекислому газу
32,9Х.
Процент ДМЭ молярной
Селективности по отношению,к
Продолжительность испытания, ч
СН ОН со конверсии
СО
220
32,8
63,5
220
32,7
63
220
33,5
220
33,9
186
225
33,9
352
225
33,7
34,7
528
230
230
685
33,4
230
810
60,5
33,8 повышенной температуре и давлении
7000 — 11000 кПа, в присутствии
35 катализатора, включающего окислы кремния, алюминия, меди и цинка, отличающийся тем, что, с целью упрощения процесса, в качестве катализатора используют ката40 лизатор формулы
S | Al
51,AII,Cu Zn CråО у где x = количество кислорода, удовлетворяющее все валентности: а = 45-54
b= 0,1 — 10;
50 с = 25,9-30; д = 11-15; е = 10, и процесс ведут при температуре 220
240 С и объемной скорости подачи
55 сырья 2000 — 2500 ч
ВНИИПИ Заказ 3499/58 Тираж 371 Подписное
Произв.-полигр. пр-тие, г. Ужгород, ул. Проектная, 4
Таким образом, предлагаемый способ позволяет вести процесс при конверсии 58 — 69% при селективности, превращения СО в ДМЭ 61,8 — 64,IX и температуре 220 — 240 С, тогда как в известном способе при конверсии 5662Х и селективности превращения СО в
ДМЭ 60,8 — 63,2Х процесс ведут при
260 — 330 С. 11ри этом в предлагаемом способе катализатор стабильно работает длительное время — не менее
810 ч. Конверсия CO за этот период снижается с 64 до 60,5Х, Тогда как в известном способе уже через 264 ч конверсия СО снижается с 62 до
57Х.
Формула изобретения
Способ получения диметилового эфира взаимодействием водорода и окиси углерода, взятых при молярном соотношении, равном 1-3 :1, при
Пример 7. В условиях примера вели процесс в течение 810 ч.
Результаты получения ДМЭ из СО и
Н представлены в таблице.
63,5 3,7
64,1 3,2
62,4 . 4,1
61,8 4,3
62,2 3,9
62,4 3,9
61,3 4,0
62,5 4,1
62,0 4,2



www.findpatent.ru
- Эфир hd 600ru
- Эфир криптовалюта прогноз
- На латинском эфир
- Последний эфир трахтенберга
- H1 прямой эфир
- Сложные эфиры строение
- Луна прямой эфир
- Стрим казино эфир
- Название простых эфиров
- Прямой эфир ермак
- Ермак прямой эфир