Получение диметилового эфира из синтез-газа на базе метанольного производства – часть 1. Диметилового эфира получение
Получение диметилового эфира из синтез-газа на базе метанольного производства – часть 1
На правах рукописи
ЛЯХИН Дмитрий Владимирович
ПОЛУЧЕНИЕ ДИМЕТИЛОВОГО ЭФИРА ИЗ СИНТЕЗ-ГАЗА
НА БАЗЕ МЕТАНОЛЬНОГО ПРОИЗВОДСТВА
Специальность 05. 17. 01
Технология неорганических веществ
АВТОРЕФЕРАТ
диссертации на соискание учёной степени
кандидата технических наук
Иваново 2008
Работа выполнена в Государственном образовательном учреждении
высшего профессионального образования Ивановский государственный химико-технологический университет на кафедре «Технология неорганических веществ»
и в ОАО «Новомосковская акционерная компании «Азот»
Научный руководитель: | доктор технических наук, профессор Морозов Лев Николаевич |
Официальные оппоненты: | доктор технических наук, профессор Липин Александр Геннадьевич, Ивановский государственный химико-технологический университет |
доктор технических наук, профессор Савостьянов Александр Петрович Южно-Российский государственный технический университет (Новочеркасский политехнический институт) |
Ведущая организация: | ООО «НИАП – Катализатор», г. Новомосковск |
Защита состоится 9 февраля 2009 г. в 10 час. на заседании Совета по защите докторских и кандидатских диссертаций Д. 212.063.02 при Государственном образовательном учреждении высшего профессионального образования Ивановский государственный химико-технологический университет по адресу:
153000, г. Иваново, пр. Энгельса, 7, ауд. Г – 205.
С диссертацией можно ознакомиться в библиотеке ГОУ ВПО ИГХТУ по адресу: 153000, г. Иваново, пр. Энгельса, 10.
Автореферат диссертации разослан 23 декабря 2008 г.
Ученый секретарь Совета по защите докторских и кандидатских диссертаций, д. т.н., ст. н.с. | Гришина Е. П. |
Общая характеристика работы
Актуальность темы диссертации. Синтез-газ (оксиды углерода и водород) является исходным сырьём для ценных химических продуктов, в том числе метанола. Технология синтетического метанола хорошо отработана, а его производство получило значительное распространение из-за широкого использования метилового спирта в промышленности. В последнее время становится актуальным получение и использование диметилового эфира (ДМЭ), производство которого может быть основано или на реакции дегидратации метанола, или на прямом получении его из синтез-газа.
ДМЭ позволяет решить приобретающие все большую остроту ряд проблем ухудшения окружающей среды, включающие атмосферное загрязнение и истощение ресурсов. ДМЭ относится к хладагентам, обладающим нулевым значением потенциала озоноразрушения (ODP). Использование ДМЭ в качестве моторного топлива позволяет радикально улучшить качество выхлопа дизельных двигателей с уменьшением выброса вредных компонентов. ДМЭ, в качестве полупродукта, легко превращается в бензин, характеризующийся улучшенными экологическими характеристиками (преобладание разветвленных углеводородов) и минимальным содержанием нежелательных примесей.
В настоящее время, как в России, так и за рубежом имеются разработки технологии прямого получения ДМЭ из синтез-газа, минуя стадию синтеза и очистки метанола, что является наиболее прогрессивным и экономичным решением. Для получения ДМЭ возможно использовать оборудование метанольного производства, имеющего близкую технологию, что позволяет существенно снизить капитальные затраты на новое строительство. В тоже время, практический опыт эксплуатации промышленных установок синтеза ДМЭ почти отсутствует. Нет готовых технических решений и хорошо отработанных технологий. Серийный выпуск промышленного катализатора синтеза ДМЭ не налажен, также как и отсутствует опыт его эксплуатации. Кроме того, необходима разработка технологии выделения и очистки ДМЭ. Отсутствуют разработки методов анализа состава ДМЭ, полученного по промышленной технологии из синтез-газа. Поэтому работы, направленные на усовершенствование технологической схемы получения ДМЭ из синтез-газа на базе метанольного производства и последующей его очистки является актуальными.
Цель работы. На основе изучения процессов каталитического синтеза и выделения чистого ДМЭ разработать мероприятия, позволяющие улучшить технологию получения диметилового эфира из синтез-газа. Для решения поставленной задачи необходимо:
1. Исследовать свойства различных каталитических систем, в том числе гибридных катализаторов, в процессе дегидратации метанола и прямого синтеза ДМЭ из синтез-газа;
2. Идентифицировать параметры кинетического уравнения каталитической реакции дегидратации метанола;
3. Разработать математическую модель каталитического процесса получения ДМЭ и провести численное моделирование для промышленного реактора с целью выбора рациональных режимов работы;
4. Провести промышленные испытания катализатора прямого синтеза ДМЭ из синтез-газа;
5. Исследовать процесс выделения и очистки ДМЭ в промышленных условиях и разработать мероприятия по усовершенствованию данной технологии;
6. Разработать методику выполнения измерений состава ДМЭ для контроля качества продукта.
Научная новизна работы заключается в том, что, научный подход к решению производственной задачи получения диметилового эфира использован на основных стадиях действующего метанольного производства:
- исследованы нанесённые катализаторы и их комбинации с промышленным катализатором синтеза метанола, обеспечивающие получение диметилового эфира из метанола и синтез-газа;
- методом математического моделирования установлены рациональные режимы эксплуатации и способы загрузки катализаторов в реактор для получения метанола и диметилового эфира;
- на основании теоретических расчетов и экспериментальных данных по состоянию гетерогенной системы «жидкий диметиловый эфир – диоксид углерода» предложены технические решения по улучшению технологической схемы ректификации для получения чистого ДМЭ.
Практическая значимость работы
- Проведена апробация процесса совместного получения метанола и диметилового эфира на действующем оборудовании метанольного производства, установлены режимы его промышленного получения из синтез-газа и направления усовершенствования технологии.
- Усовершенствована технологическая схема ректификации метанола-сырца с выделением чистого ДМЭ, что позволило снизить содержание примесей в продукте и сократить его потери со сдувками.
- Разработана методика анализа диметилового эфира, которая включена в технические условия на ДМЭ: ТУ 2434-059-05761643-2001 «Эфир диметиловый жидкий», аттестована в соответствии с требованиями ГОСТ Р 8.563-96 и зарегистрирована в ФГУП «ВНИИМС».
Достоверность результатов основывается на применении современных методов исследования, воспроизводимостью данных в пределах заданной точности анализа и проверкой адекватности моделей по результатам промышленных испытаний гибридного катализатора и системы разделения продуктов синтеза.
Личный вклад автора заключается:
- в проведении экспериментальных исследований по изучению активности нанесённых и гибридных катализаторов в процессах получения ДМЭ;
- в постановке и решению технической задачи по математическому моделированию процесса синтеза ДМЭ в реакторе;
- в разработке программы и участии в проведении промышленных испытаний бифункционального катализатора получения ДМЭ, анализе и обобщении результатов обследования промышленного агрегата синтеза ДМЭ;
- в расчёте процесса и разработке технических решений по совершенствованию технологической схемы ректификации;
- в постановке задачи и участии в разработке методики анализа жидкого ДМЭ.
Апробация работы. Основные положения и результаты работы докладывались и обсуждались на следующих конференциях:
II Украинской научно-технической конференции по катализу, Северодонецк, 2000г., Всероссийской научно-технической конференции по технологии неорганических веществ, Казань, 2001г., Международной научной конференции «Математические методы в технике и технологии», Казань, 2005г., V международной научно-технической конференции по катализу «Укркатализ – V», Киев, 2006г., VI Российской конференции «Научные основы приготовления и технологии катализаторов», г. Туапсе, 2008г.
Публикации. По теме диссертации опубликовано 10 печатных работ из них 3 статьи в периодических научных изданиях и 7 тезисов докладов на научно-технических конференциях.
Структура и объём диссертации. Диссертация состоит из введения, 6 глав, выводов, списка использованной литературы из 106 наименований и приложений. Работа изложена на 156 страницах, содержит 41 рисунок и 31 таблицу.
Содержание работы
Во введении обосновывается актуальность темы диссертации, формулируются цели и задачи исследования, научная новизна и практическая значимость работы.
В первой главе приводится литературный обзор. Рассматриваются различные каталитические системы в процессе дегидратации метанола с получением ДМЭ, а также синтеза ДМЭ или совместного синтеза метанола и ДМЭ в процессах гидрирования СО и СО2, при этом образование ДМЭ происходит на сложных катализаторах, включающих кислотные центры, образованные оксидом алюминия и другими модифицированными носителями. Рассмотрены различные схемы получения метилформиата. Представлены результаты исследования различных каталитических систем в процессе дегидрирования метанола с образованием метилформиата. Описаны результаты исследований по изучению оксидных и серебросодержащих каталитических систем в процессах переработки метанола в формальдегид. Представлены предлагаемые исследователями механизмы процессов получения ДМЭ как дегидратацией метанола, так и его синтезом из СО-содержащего газа. Описан механизм бифункционального катализа ДМЭ из синтез-газа. Также рассмотрен механизм получения метилформиата и формальдегида из метанола. Рассмотрены технологические схемы и условия проведения процесса получения и выделения ДМЭ.
Во второй главе представлена методика проведения эксперимента и расчета основных характеристик для оценки активности катализаторов. Изучены каталитические свойства оксида алюминия в процессе дегидратации метанола с получением диметилового эфира. Исследовано влияние на степень конверсии метанола размера зерен катализатора, начальной концентрации метанола, навески катализатора. С увеличением размера зёрен катализатора степень конверсии уменьшается (рис.1), что объясняется уменьшением степени использования внутренней поверхности зерна и влиянием процесса переноса реагентов в порах катализатора.
Сравнение активности мелкой фракции катализатора при различной начальной концентрации метанола в исходной смеси показывает, что скорость реакции не подчиняется уравнению первого порядка, так как степень конверсии выше при более низкой концентрации метанола на входе в реактор. Поэтому далее, при математическом моделировании процесса, использовалось кинетическое уравнение, приводимое в соответствующей научной литературе.
Для идентификации параметров кинетического уравнения реакции дегидратации метанола на оксиде алюминия, а именно: предэкспоненциального множителя и энергии активации, проведён эксперимент с варьированием концентрации метанола в исходном газе и объёма загрузки мелкой фракции катализатора в отсутствие диффузионного торможения. Представлен соответствующий алгоритм расчета и определены ки-
Рис.1. Зависимости степени конверсии метанола от температуры реакции при различном фракционном составе катализатора g-Al2O3 (начальная концентрация метанола в смеси от 4,3 до 5,1 об. %): 1 – фракция 1,0 – 2,0 мм, mк=1,5 г; 2 – фракция 0,31 – 0,50 мм, mк =1,5 г; 3 – фракция 0,16 – 0,25 мм, mк=1,55 г. |
нетические параметры уравнения, которые далее использовали при численном моделировании процесса в промышленном реакторе. Представлены подходы к определению параметров процесса при работе с крупной фракцией катализатора (dгран > 0,3 мм), где учитывается скорость переноса реагентов в порах.
С целью улучшения свойств катализаторов переработки метанола исследованы каталитические свойства модельных образцов, полученных нанесением на g-Al2O3 оксидов меди и цинка, с концентрациями от 1 до 10 мас.%. При относительно низких температурах (175-250 0С) на данных катализаторах наряду с ДМЭ образуется метилформиат (МФ), а при более высоких температурах выход диметилового эфира резко снижается и в продуктах появляется метан. Показано, что с увеличением содержания меди в катализаторе наблюдается рост удельной производительности по диметиловому эфиру и метилформиату при невысоких температурах. Наряду с этим происходит разложение метанола на более лёгкие газы – СО, СО2, Н2. Эксперименты по определению каталитической активности образцов с разной загрузкой катализатора, подтверждают, что диметиловый эфир и метилформиат являются промежуточными веществами в ряду реакций разложения метанола на более простые вещества. С уменьшением объёма загрузки катализатора удельная производительность его по диметиловому эфиру и метилформиату возрастает, то есть данные продукты не успевают разлагаться из-за малого времени контакта веществ с катализатором.
Проведенные исследования в среде с повышенным содержанием водорода показали, что общая скорость химической реакции на данных катализаторах существенно ниже, т. е. в присутствии водорода подавляются некоторые маршруты переработки метанола. Так водород, являясь продуктом дегидрирования метанола, снижает как равновесную концентрацию метилформиата, так и скорость его образования вдали от равновесия. В то же время количество образующегося диметилового эфира, в общем, несколько увеличивается, как при низких температурах, так и при высоких температурах реакции (рис. 2). Если при низких температурах это увеличение обусловлено подавлением параллельного маршрута образования метилформиата, и соответственно большая часть метокси-групп может перейти в диметиловый эфир, то при высоких температурах очевидно большая концентрация водорода подавляет реакцию разложения диметилового эфира, так как водород является одним из его продуктов.
Согласно литературным данным, механизм получения ДМЭ из синтез-газа предполагает образование метанола и его последующую дегидратацию, поэтому в настоящей работе изучен процесс получения метанола и диметилового эфира на смеси катализаторов: метанольного CuO∙ZnO∙Al2O3 (СНМ-У, С-79) и активной g-Al2O3 (кислотно-
Рис.2. Зависимости производительности катализатора CuO∙ ZnO/Al2O3 от температуры реакции в реакции разложения метанола по ДМЭ (1; 1′), МФ (2; 2’) и метану (3; 3’): 1, 2, 3 – исходная смесь MeOH/Ar; 1’, 2’, 3’ – исходная смесь MeOH/(Ar+h3). |
основного). Были апробированы различные способы смешения этих катализаторов: механическая смесь гранул, смесь мелкой фракции катализаторов с последующим таблетированием, а также смесь катализаторов, обработанную в вибромельнице с последующим таблетированием. Показано, что более тесный контакт частиц катализаторов, который достигается при измельчении смеси и таблетировании, ухудшает каталитические свойства системы в отношении получения диметилового эфира. Это может быть обусловлено перекрытием активной поверхности оксида алюминия мелкими частицами метанольного катализатора, и исключением её из реакции.
С увеличением доли метанольного катализатора в смеси (при одинаковом объёме загрузки) сильно возрастает концентрация образующегося диметилового эфира (рис. 3). Это говорит о сильной зависимости скорости маршрута дегидратации от концентрации исходного вещества – метанола. При этом, большая доля кислотно-основного катализатора еще не обеспечивает высокую производительность смеси по диметиловому эфиру, т. к. при более низкой концентрации метанола скорость его дегидратации также получается невысокой. Перерасчет общей производительности смеси на индивидуальные катализаторы показывает, что с увеличением доли кислотно-основного катализатора его удельная производительность уменьшается. В тоже время производительность метанольного катализатора, с учетом количества образовавшегося диметилового эфира, остается величиной примерно постоянной, но увеличивается по сравнению с работой индивидуального метанольного катализатора, что обусловлено переработкой образующегося метанола на кислотно-основном компоненте смеси.
Третья глава посвящена математическому моделированию. Для расчета процесса получения метанола и диметилового эфира на смеси катализаторов в промышленном реакторе разработана математическая модель и соответствующее программное обеспечение. В основе описания лежит двухфазная модель, в которой рассматриваются концентрации реагентов в объеме газового потока и грануле катализаторов. Разность температур между катализатором и потоком не учитывается, т. к. в условиях промышленного катализа коэффициент теплоотдачи оказывается достаточно высоким, а теплопроводность материала катализатора обеспечивает прогрев гранул. В математическом описании промышленного аппарата не учитывается диффузионное торможение в порах катализатора, а таблетки рассматриваются как гранулы с определённой эффективной активностью объёма катализатора.
pandia.ru
9. Производство ДМЭ из метанола. Получение диметилового эфира дегидратацией метанола на АlPO4 +SiO2 катализаторах
Похожие главы из других работ:
Висмут и его соединения в природе
2.1.3 Добыча и производство
Традиционные потребители висмута - металлургическая, фармацевтическая и химическая промышленность. В последние десятилетия к ним прибавились ядерная техника и электроника...
Влияние управляющих параметров на равновесие и скорость реакции синтеза метанола
1. Общие сведения о производстве метанола
Метанол (метиловый спирт, древесный спирт) - простейший одноатомный спирт. Он представляет собой бесцветную прозрачную жидкость со слабым спиртовым запахом, сильнейший яд. Молекулярная масса равна 32. Плотность р=793 кг/м3 (20°С)...
Влияние управляющих параметров на равновесие и скорость реакции синтеза метанола
1.1 Промышленные способы получения метанола
В промышленности существует несколько способов получения метанола: При сухой перегонке дерева получаются твердые, жидкие и газообразные продукты. Жидкими продуктами являются древесный деготь и водный слой...
Влияние управляющих параметров на равновесие и скорость реакции синтеза метанола
1.2 Схема производства метанола
Ввиду высокой экзотермичности реакции и необходимости точного регулирования температуры, повышение которой отрицательно сказывается как на равновесии, так и на избирательности процесса...
Получение диметилового эфира дегидратацией метанола на АlPO4 +SiO2 катализаторах
2. Получение метанола
Метанол является одним из важнейших по значению и масштабам производства органическим продуктом, выпускаемым химической промышленностью. Способы его получения могут быть различны: сухая перегонка древесины...
Получение диметилового эфира дегидратацией метанола на АlPO4 +SiO2 катализаторах
3. Использование метанола
На основании лабораторных и дорожных испытаний было установлено, что метанол представляет собой перспективное «чисто» сгорающее автомобильное топливо. При работе на метаноле возникают небольшие проблемы, которые могут быть легко преодолены...
Получение диметилового эфира дегидратацией метанола на АlPO4 +SiO2 катализаторах
4. Получение диметилового эфира дегидратацией метанола
Дегидратация метанола с получением диметилового эфира-исторически первый путь проведения данного синтеза. Этому процессу ещё с 1960-х годов было посвящено множество работ советских и зарубежных учёных [10, 13 - 16]...
Получение диметилового эфира дегидратацией метанола на АlPO4 +SiO2 катализаторах
5. Направления использования продуктов разложения метанола
...
Получение хлористого винила
1.5 Производство винилиденхлорида
Винилиденхлорид, хлористый винилиден, 1, 1 -- дихлорэтилен, СН2=СС12 --бесцветная жидкость со слабым запахом, температура кипения 31,7°С; температура замерзания-122,1°С, удельный вес 1,219. Пределы взры-ваемости с воздухом от 7 до 16% объемных...
Получение хлористого винила
1.6 Производство винилацетата
Уксусновиниловый эфир или винилацетат Ch3=CHOCOCh4--жидкость специфического запаха, слезоточивого действия, температура кипения 73°С, температура плавления--84°С, удельный вес 0,9342. Винилацетат способен полимеризоваться, образуя поливипилацетаты...
Получение хлористого винила
1.7 Производство этиленгликоля
Этиленгликоль СН2ОН--СН2ОН--бесцветная густая жидкость сладкого вкуса, температура кипения 197,2°С, температура плавления--13,2°С, удельный вес 1,114. Это простейший двуатомный спирт...
Производство уксусной кислоты
1.3.5 Производство уксусной кислоты из метанола и оксида углерода
Производство уксусной кислоты жидкофазным карбонилированием метанола осуществляется при 250°С и 63...
Развитие химической технологии на основе синтез-газа
Получение метанола
Метанол, один из основных продуктов многотоннажной химии, широко используется для получения множества ценных химических веществ: формальдегида, сложных эфиров, аминов, растворителей, уксусной кислоты...
Развитие химической технологии на основе синтез-газа
Применение метанола
Химическая промышленность. В данной индустрии метанол или метиловый спирт применяется как полупродукт большинства промышленных синтезов. Метанол вступает в реакцию со многими органическими соединениями...
Синергизм пищевых добавок
3.6 Производство пектинов
Производство пектина - динамически развивающийся бизнес с ежегодным увеличением производства на 3-4 %. Мировое производство и рынок пектина в основном сосредоточены в Европе (Германия, Швейцария, Дания, Прибалтика и др.), а также в Аргентине...
him.bobrodobro.ru
4. Получение диметилового эфира дегидратацией метанола. Получение диметилового эфира дегидратацией метанола на АlPO4 +SiO2 катализаторах
Похожие главы из других работ:
Анализ технологического процесса схемы переэтерификации диметилового эфира цианоэтилфосфоновой кислоты моноэтиленгликоль (мет) акрилатом
2. Концептуальное описание схемы переэтерификации диметилового эфира в-цианоэтилфосфоновой кислоты моноэтиленгликоль(мет)акрилатом
В колбу Кляйзена, снабженную водяным холодильником, помещают диметилового эфира в-цианоэтилфосфоновой кислоты. Добавляют моноэтиленгликольметакрилат (МЭГ), а также около 1 % гидрохинона для ингибирования реакции полимеризации МЭГа...
Анализ технологического процесса схемы переэтерификации диметилового эфира цианоэтилфосфоновой кислоты моноэтиленгликоль (мет) акрилатом
3. Конструктивно-функциональный анализ лабораторного реактора для проведения переэтерификации диметилового эфира в-цианоэтилфосфоновой кислоты моноэтиленгликоль(мет)акрилатом
Рис...
Анализ технологического процесса схемы переэтерификации диметилового эфира цианоэтилфосфоновой кислоты моноэтиленгликоль (мет) акрилатом
5. Анализ технологического процесса переэтерификации диметилового эфира в-цианоэтилфосфоновой кислоты моноэтиленгликоль (мет)акрилатом
Проведем анализ реакции переэтерификации диметилового эфира в-цианоэтилфосфоновой кислоты моноэтиленгликоль(мет)акрилатом...
Влияние управляющих параметров на равновесие и скорость реакции синтеза метанола
1. Общие сведения о производстве метанола
Метанол (метиловый спирт, древесный спирт) - простейший одноатомный спирт. Он представляет собой бесцветную прозрачную жидкость со слабым спиртовым запахом, сильнейший яд. Молекулярная масса равна 32. Плотность р=793 кг/м3 (20°С)...
Влияние управляющих параметров на равновесие и скорость реакции синтеза метанола
1.1 Промышленные способы получения метанола
В промышленности существует несколько способов получения метанола: При сухой перегонке дерева получаются твердые, жидкие и газообразные продукты. Жидкими продуктами являются древесный деготь и водный слой...
Влияние управляющих параметров на равновесие и скорость реакции синтеза метанола
1.2 Схема производства метанола
Ввиду высокой экзотермичности реакции и необходимости точного регулирования температуры, повышение которой отрицательно сказывается как на равновесии, так и на избирательности процесса...
Желтые вещества из кобаламинов в присутствии перекиси водорода
Структура и электронные свойства гептаметилового эфира дициано - и аквацианокобириновой кислоты и стабильных желтых форм гептаметилового эфира дициано - и аквацианокобириновой кислоты
Сокращения: стабильное желтое производное гептаметилового эфира кобириновой кислоты, (5R,6R) - Coб,Coв-дициано-5,6-дигидро-5-гидрокси-гептаметилкоб (III) иринат-с...
Получение диметилового эфира дегидратацией метанола на АlPO4 +SiO2 катализаторах
2. Получение метанола
Метанол является одним из важнейших по значению и масштабам производства органическим продуктом, выпускаемым химической промышленностью. Способы его получения могут быть различны: сухая перегонка древесины...
Получение диметилового эфира дегидратацией метанола на АlPO4 +SiO2 катализаторах
3. Использование метанола
На основании лабораторных и дорожных испытаний было установлено, что метанол представляет собой перспективное «чисто» сгорающее автомобильное топливо. При работе на метаноле возникают небольшие проблемы, которые могут быть легко преодолены...
Получение диметилового эфира дегидратацией метанола на АlPO4 +SiO2 катализаторах
5.3. Направления использования диметилового эфира
Диметиловый эфир в настоящее время используется главным образом как безвредный для окружающей среды наполнитель аэрозольных баллончиков...
Получение диметилового эфира дегидратацией метанола на АlPO4 +SiO2 катализаторах
6. Использование диметилового эфира в качестве моторного топлива дизельных двигателей
В России с 1992-го, а за рубежом с 1994 г. ведутся работы по использованию ДМЭ в качестве моторного топлива для дизелей. Основными фирмами разработчиками в России является НИИ двигателей, а за рубежом Haldtr Topse A/S, Technical University of Denmark, AVL LIST Gmbh (Austria), Amoco Corp...
Получение диметилового эфира дегидратацией метанола на АlPO4 +SiO2 катализаторах
9. Производство ДМЭ из метанола
Пошел второй год, как на новомосковском "Азоте" работает единственная на территории СНГ действующая установка для получения диметилового эфира из метанола сырца. Диметиловый эфир, ценный хладагент, заменитель фреонов и дизельных топлив...
Развитие химической технологии на основе синтез-газа
Получение метанола
Метанол, один из основных продуктов многотоннажной химии, широко используется для получения множества ценных химических веществ: формальдегида, сложных эфиров, аминов, растворителей, уксусной кислоты...
Развитие химической технологии на основе синтез-газа
Применение метанола
Химическая промышленность. В данной индустрии метанол или метиловый спирт применяется как полупродукт большинства промышленных синтезов. Метанол вступает в реакцию со многими органическими соединениями...
Синтез диэтилового эфира малоновой кислоты. Свойства и основные методы получения сложных эфиров
1.1. Свойства диэтилового эфира малеиновой кислоты
Диэтиловый эфир малеиновой кислоты, диэтилмалеат, этилмалеат C2H5OOCCH=CHCOOC2H5. Температура замерзания: ~-11.5°C, температура кипения: 225.3°C, дипольный момент: 2.54 Дебай, диэлектрическая проницаемость: 8.58 при 230С, плотность: 1.0687 при 20°С, г/мл...
him.bobrodobro.ru
Способ получения диметилового эфира
Использование: нефтехимия. Сущность: метанолсодержащий поток контактируют с дегидратирующим катализатором в одной или нескольких реакционных зонах. Компоненты реакционной смеси с помощью дистилляции и/или ректификации разделяют с возвращением непрореагировавшего метанола в реакционную(ые) зону(ы). Дегидратацию метанола и образование эфира проводят в жидком и/или парожидкостном состоянии в присутствии кислого катионита при температуре от 100 до 160°С и поддерживают концентрацию воды в возвращаемом в реакционную(ые) зону(ы) метанольном потоке менее 12% мас., предпочтительно менее 5% мас. Технический результат - упрощение технологии процесса. 12 з.п. ф-лы, 4 ил.
Изобретение относится к области получения диалкиловых эфиров. Более конкретно изобретение относится к области получения диметилового эфира из метанолсодержащего потока.
Известен способ [US Pat. 4560807, 24.12.1985 г.] получения диметилового эфира путем парофазной дегидратации метанола в присутствии твердого кислотного катализатора с последующим охлаждением реакционной смеси и ее разделением в двух последовательных ректификационных колоннах с возвращением непрореагировавшего метанола в зону дегидратации. При этом в качестве катализаторов процесса дегидратации заявлены алюминиевый катализатор и/или кремниевый катализатор, не являющийся цеолитом.
Недостатком процесса является значительная энергоемкость из-за необходимости нагревать и испарять большие количества исходного и рециркулируемого метанола.
Известен также способ [US Pat. 5750799, 12.05.1998 г.] получения диметилового эфира путем газофазного контактирования метанолсодержащего потока, включающего свежий метанол и рециркулируемый метанол и воду, с дегидратирующим катализатором с получением газовой смеси, содержащей диметиловый эфир, метанол и воду. Газовую смесь подвергают разделению дистилляцией, при которой отделяют диметиловый эфир от метанола и воды, а затем из остающейся смеси метанола и воды отгоняют поток метанола с частью воды, который рециркулируют в указанную зону контактирования метанолсодержащего потока с дегидратирующим катализатором. Заявлены мольное отношение (МО) воды по отношению к метанолу в указанном рециркулируемом потоке как минимум 0,25:1, что соответствует более 12% маc. воды, либо (в независимом пункте) как минимум МO=0,6, что соответствует более 25% маc. воды.
Недостатком способа также является значительная энергоемкость, связанная с необходимостью нагревания и испарения большого количества метанолсодержащего потока, в том числе излишней воды. Недостатком является также отрицательное влияние возвращаемого в зону реакции чрезмерно большого количества воды на конверсию метанола: как на равновесную конверсию, так и на скорость превращения при преимущественной сорбции воды катализатором.
В описании процессов US Pat. 5750799 в качестве катализатора указано лишь кислое соединение алюминия и весьма высокая температура в реакционной зоне - от 288 до 343°С, что также требует большего энергопотребления.
Мы предлагаем способ получения диметилового эфира из метанолсодержащего потока путем его контактирования с дегидратирующим катализатором в одной или нескольких реакционных зонах и разделения компонентов реакционной смеси с помощью дистилляции и/или ректификации с возвращением непрореагировавшего метанола в реакционную(ые) зону(ы), при котором дегидратацию метанола и образование эфира проводят в жидком и/или парожидкостном состоянии в присутствии кислого катионита при температуре от 100 до 160°С и поддерживают концентрацию воды в возвращаемом в реакционную(ые) зону(ы) метанольном потоке менее 12% мас., предпочтительно менее 5% мас.
Как вариант предлагаем способ, при котором используют метанолсодержащий поток, получаемый в результате химического взаимодействия оксида углерода и водорода, отгонки непрореагировавших исходных веществ и возможно отгонки как минимум части диметилового эфира, причем указанный метанолсодержащий поток подают в реакционную зону и/или последующую зону отгонки диметилового эфира и/или зону ректификации метанола от воды.
Как вариант предлагаем способ, при котором дегидратацию метанола и образование эфира проводят в одной или нескольких реакционных зонах, возможно с подводом или отводом теплоты в реакционных зонах и/или между последовательными реакционными зонами.
Как вариант предлагаем способ, при котором между последовательными реакционными зонами осуществляют промежуточный вывод испаренного(ых) потока(ов), содержащего(их) преимущественно диметиловый эфир.
Как вариант предлагаем способ, при котором метанолсодержащий поток подают в вертикальную реакционную зону снизу, в реакционной зоне проводят частичное испарение потока, сверху выводят в паровой фазе поток, в котором преобладает диметиловый эфир, и выводят в жидкой фазе поток, содержащий преимущественно воду и метанол.
Как вариант предлагаем способ, при котором из жидкой смеси, выводимой из реакционной(ых) зон(ы), отделяют диметиловый эфир в отгонной зоне, после чего из остающейся смеси выделяют метанол в качестве дистиллата в последующей ректификационной зоне выделения метанола и возвращают его в реакционную(ые) зону(ы).
Как вариант предлагаем способ, при котором в отгонной зоне отделение диметилового эфира от метанола и воды осуществляют ректификацией.
Как вариант предлагаем способ, при котором в указанную отгонную зону предпочтительно выше точки подачи реакционной смеси подают поток(и), содержащий(е) преимущественно диметиловый эфир, выводимый(е) между реакционными зонами и/или сверху реакционной зоны.
Как вариант предлагаем способ, при котором получение диметилового эфира осуществляют в реакционно-ректификационной системе, в которой реакционная зона соединена противоточными потоками жидкости и пара с исчерпывающей и укрепляющей реакционными зонами, метанолсодержащий поток подают в реакционную зону и/или в верхнюю часть исчерпывающей ректификационной зоны и/или в нижнюю часть укрепляющей ректификационной зоны и сверху указанной укрепляющей зоны выводят поток, содержащий преимущественно диметиловый эфир, а снизу указанной исчерпывающей зоны выводят поток, содержащий преимущественно воду.
Как вариант предлагаем способ, при котором получение диметилового эфира осуществляют в реакционно-ректификационной системе, включающей ректификационную зону и как минимум одну соединенную с ней входящим и выходящим потоками прямоточную реакционную зону, в которую направляют боковой поток указанной ректификационной зоны, предпочтительно выводимый ниже питающего потока, и сверху указанной ректификационной зоны выводят поток, содержащий преимущественно диметиловый эфир, а снизу выводят поток, содержащий преимущественно воду.
Как вариант предлагаем способ, при котором синтез диметилового эфира первоначально осуществляют в прямоточной(ых) реакционной(ых) зоне(ах), а затем в реакционно-ректификационной системе, сверху которой выводят преимущественно диметиловый эфир, а снизу выводят преимущественно воду.
Как вариант предлагаем способ, при котором при синтезе диметилового эфира в прямоточной(ых) реакционной(ых) зоне(ах) используют мелкозернистый сульфокатионит, а при синтезе диметилового эфира в реакционно-ректификационной системе используют сульфокатионитный катализатор с размером частиц не менее 3 мм, предпочтительно имеющий форму цилиндров или массообменной насадки, в частности колец.
Как вариант предлагаем способ, при котором выделяемый поток, содержащий преимущественно диметиловый эфир, подвергают дополнительно водной отмывке от метанола и водно-метанольную смесь подают в зону ректификации от воды и/или в исчерпывающую ректификационную зону реакционно-ректификационной системы.
Использование предлагаемого способа иллюстрируется чертежами (фиг.1-4) и примерами. Указанные чертежи и примеры не исчерпывают всех возможных вариантов реализации способа и возможно использование иных технических решений при соблюдении признаков, изложенных в формуле изобретения.
Согласно фиг.1 исходный метанолсодержащий поток подают по линии 1. Его смешивают с рециркулируемым метанолсодержащим потоком 10, подогревают в теплообменнике и по линии 2 подают в реакционную зону Р1, содержащую кислый катионит. Из реакционной зоны Р1 по линии 3 выводят реакционную смесь, которую подают в отгонную зону К1 по линиям 3а и 4б, либо во вторую реакционную зону Р2 по линии 3б (предпочтительно после охлаждения). Для выравнивания температуры в Р1 часть потока 3 и/или 3б может быть после охлаждения рециркулирована по линии 3в на вход в P1. Поток 3а или его часть может быть направлен(а) в сепаратор-испаритель С, откуда испаренный поток, содержащий преимущественно диметиловый эфир (ДМЭ), по линиям 3г и 4а подают в К1, а неиспаренную часть по линии 3д направляют в Р2.
При использовании реакционной зоны Р2 реакционную смесь из нее выводят по линии 4 и подают в К1 по линии 4б.
Отгонная зона К1 может представлять из себя выпарной аппарат (рибойлер), либо отгонную или ректификационную колонну. Сверху отгонной зоны К1 выводят паровой поток 5, который подвергают парциальной или полной конденсации. В случае парциальной конденсации по линии 6 выводят несконденсированный поток, содержащий преимущественно ДМЭ. По линии 7 выводят сконденсированный поток, содержащий преимущественно ДМЭ. Предпочтительно часть сконденсированного потока по линии 8 возвращают в отгонную зону К1 в качестве флегмы.
Поток 6 далее может быть дополнительно подвергнут компремированию и/или конденсации. Потоки 6 и 7 могут быть дополнительно подвергнуты отмывке от примеси метанола и осушке (на фиг.1 не показано).
Если исходный поток 1 содержит значительное количество ДМЭ и, возможно, воды, то он может быть полностью или частично подан в отгонную зону К1 по линии 1б (показано пунктиром), а при значительном содержании только воды (без ДМЭ) - ректификационную зону К2.
Снизу К1 по линии 9 выводят поток, содержащий преимущественно воду и метанол, и направляют его в ректификационную зону К2. Сверху зоны К2 по линии 10 выводят метанолсодержащий поток, который рециркулируют на вход в реакционную зону Р1 (возможно, частично в Р2). Снизу К2 по линии 11 выводят поток, содержащий в основном воду.
Согласно фиг.2 исходный метанолсодержащий поток 1 и рециркулируемый метанолсодержащий поток 10 подогревают и по линии 2 вводят снизу в реакционную зону Р.
Сверху зоны Р выводят по линии 3 в парообразном состоянии поток, содержащий преимущественно диметиловый эфир с примесью метанола и возможно воды. Указанный поток полностью или частично выводят по линии 3а (возможно предварительно сконденсировав и подвергнув водной отмывке), либо направляют по линии 3б в верхнюю часть отгонной зоны К1 предпочтительно выше подачи потока 4а.
Из верхней части зоны Р выводят по линии 4 в жидком состоянии поток, содержащий преимущественно воду, метанол и возможно частично диметиловый эфир. Поток 4 подают в отгонную зону (колонну) К1 по линии 4а.
Если исходный поток 1 имеет высокое содержание ДМЭ, его полностью или частично подают в К1 по линиям 1б и 4а.
Сверху К1 по линии 5 выводят паровой поток, содержащий преимущественно диметиловый эфир, с которым далее поступают аналогично описанному для фиг.1.
Снизу отгонной зоны К1 по линии 9 выводят поток, содержащий преимущественно воду и метанол, который далее подают в ректификационную зону К2. Сверху К2 выводят по линии 10 метанолсодержащий поток, который рециркулируют на вход в реакционную зону Р, предпочтительно после смешения с потоком 1 и нагревания.
Снизу К2 по линии 11 выводят поток, содержащий в основном воду.
Согласно фиг.3 для химического превращения метанола и непрерывного выделения ДМЭ и воды из реакционной смеси используют реакционно-ректификационную систему, включающую реакционную зону Р3 с кислым катионитным катализатором, укрепляющую ректификационную зону УЗ и исчерпывающую ректификационную зону ИЗ.
Исходный метанолсодержащий поток, поступающий по линии 1 или его часть возможно направляют в реакционно-ректификационную систему по линиям 2б, 4 и далее 4а и/или 4б и/или 4в. Как вариант, указанный поток или его часть могут быть сначала направлены по линии 2а в прямоточную реакционную зону Р. Из нее реакционная смесь по линии 3 и далее по линиям 3б, 3в, 4 и по линиям 4а и/или 4б и/или 4в поступает в реакционно-ректификационную систему (УЗ+РЗ+ИЗ) или по линии 3а поступает в сепаратор С, из которого испаренный поток, содержащий преимущественно диметиловый эфир, предпочтительно направляют по линии 3г и далее по линии 4а в нижнюю часть укрепляющей ректификационной зоны УЗ. Неиспаренную часть, выводимую из сепаратора С по линии 3а, далее направляют в реакционную зону Р3а/ или исчерпывающую ректификационную зону ИЗ, возможно предварительно смешивая с потоком 2б, если в реакционную зону Р был направлен не весь метанолсодержащий поток.
Сверху зоны УЗ выводят по линии 5 в парообразном состоянии поток 5, который подвергают парциальной или полной конденсации. По линиям 6 и/или 7 выводят поток(и), содержащий(е) преимущественно диметиловый эфир. Часть конденсированного потока возвращают по линии 8 в зону УЗ в качестве флегмы.
Снизу зоны ИЗ выводят по линии 9 поток, содержащий в основном воду.
Согласно фиг.4 используют схему с реакционно-ректификационной системой, включающей ректификационную зону (колонну) К и соединенную с ней входящим и выходящим потоками прямоточную реакционную зону Р2.
Поступающий по линии 1 исходный метанолсодержащий поток направляют непосредственно в ректификационную зону К по линиям 2б, 4 и 4б, и/или первоначально подвергают химическому превращению в прямоточной реакционной зоне Р1 (подают в нее по линии 2а и выводят реакционную смесь по линии 3). Поток 3 непосредственно подают в ректификационную зону К по линиям 3б, 3в, 4 и 4б и/или 4а, либо подвергают разделению в сепараторе-испарителе С и в К направляют раздельно поток по линии 3г (далее по линии 4а), содержащий преимущественно ДМЭ, и поток 3в (далее по линиям 4 и 4б), содержащий преимущественно метанол, воду и частично ДМЭ.
Сверху ректификационной зоны К выводят ДМЭ по линиям 6 и/или 7 поток, содержащий главным образом ДМЭ. Снизу ректификационной зоны К выводят по линии 9 поток, содержащий преимущественно воду.
В качестве прямоточных реакционных зон, показанных на фиг.1-4, могут использоваться различные известные реакторы: адиабатические жидкофазные реакторы, либо реакторы (или сочетание последовательных реакторов) с удалением теплоты (кожухотрубчатые, с частичным испарением реакционной массы, с промежуточным межреакторным охлаждением, с рециркуляцией части охлажденного потока реакционной смеси на вход в реактор и т.п.).
Далее приведены примеры использования изобретения.
Пример 1
Переработке подвергают концентрированный метанол согласно фиг.1.
Метанол по линии 1 подают в количестве 1,0 кг/ч. По линии 10 из ректификационной зоны К2 рециркулируют метанол, содержащий 8% воды.
Смесь потока 1 (по линии 1а) и потока 10, содержащую менее 0,1% диметилового эфира (ДМЭ), 96,6% метанола и 3,4% воды, подают в реакционный узел сверху. Реакционную массу поддерживают в жидком состоянии. В реакционном узле используется только реакционная зона Р1. Реакционная зона представляет собой реактор адиабатического типа.
Реакционная зона Р содержит 15,0 кг сульфокатионита Амберлист-36 производства компании Rohm & Haas. Его статическая обменная емкость СОЕ=5,4 мг-эквН+/г, размер частиц 0,3-1,2 мм.
Температура при входе в Р1 110°С, при выходе из Р1 140°С.
Конверсия метанола за проход составляет 60%.
Реакционная смесь из Р1 в количестве 1724 г/ч направляется по линиям 3а и далее 4б в отгонную зону К1. Потоки 3а и 4б содержат 41,7% ДМЭ, 38,6% метанола и 19,7% воды.
Выводимый сверху отгонной зоны К1 поток конденсируют полностью и по линии 7 выводят 719 г/ч продукта, содержащего 99,9% ДМЭ и 0,1% метанола.
Сверху ректификационной зоны К2 выводят 724 г/ч потока 10, содержащего 91,9% метанола, 0,1% ДМЭ и 8,0% воды, который рециркулируют в реакционную зону Р.
Снизу зоны К2 выводят 281 кг/ч воду, содержащую 0,01% метанола.
Общая конверсия метанола в процессе с учетом рецикла составляет 99,9%.
Пример 2
Переработке подвергают концентрированный метанол согласно фиг.1 и подобно примеру 1 (составы потоков и конверсия метанола практически те же).
В отличие от примера 1 в качестве реакционной зоны Р1 используется изотермический кожухотрубчатый реактор, в трубки которого загружен катализатор Амберлист-36. Отвод реакционной теплоты осуществляют за счет подачи хладоагента в межтрубном пространство.
Процесс проводят при температуре 130°С.
За счет использования изотермического реактора загрузка катализатора снижается до 6,0 кг.
Пример 3
Переработке подвергают концентрированный метанол согласно фиг.1 и подобно примеру 1 (составы потоков и конверсия метанола практически те же с той разницей, что состав потока 4 в примере 3 аналогичен составу потоков 3а и 4б в примере 1).
В отличие от примера 1 в реакционном узле используется две реакционные зоны (Р1 и Р2), представляющие собой реакторы адиабатического типа с промежуточным охлаждением между ними.
В реакционных зонах поддерживают температуру на входе 125°С, на выходе 140°С.
Загрузка катализатора Амберлист-36 при такой организации реакционного узла составляет 5,0 кг.
Пример 4
Переработке подвергают концентрированный метанол согласно фиг.1.
Метанол по линии 1 подают в количестве 1 кг/ч. По линии 10 рециркулируют метанол - дистиллат ректификационной зоны К2.
Реакционную узел содержит два последовательных адиабатических реактора (Р1 и Р2), заполненных мелким сульфокатионитом Амберлист-36 (см. пример 1) Загрузка катализатора составляет: Р1 - 4,5 кг, Р2 - 2,0 кг.
Смесь потоков 1 и 10, содержащую 0,6% ДМЭ, 96,0% метанола и 0,4% воды, подают в реактор Р1 узел сверху и поддерживают в жидком состоянии за счет повышенного давления - 32 ата.
Температура в реакторе Р1: на входе 115°С, на выходе 140°С. Конверсия метанола в P1 - 45%.
Из реактора Р1 по линии 3 выводят 1635 г/ч жидкой реакционной смеси, содержащей 32,5% ДМЭ, 54,5% метанола и 13,0% воды, которая в сепараторе С дросселируется до давления 15 ата и охлаждается до 125°С. При этом происходит ее частичное испарение. Из сепаратора С выводятся паровая фаза (поток 3г), содержащая 74,6% ДМЭ, 22,4% метанола и 3,0% воды в количестве 523 г/ч, и жидкая фаза (поток 3д), содержащая 12,8% ДМЭ, 69,6% метанола и 17,6% воды в количестве 1112 г/ч. Паровую фазу из сепаратора направляют в отгонную зону К1, а жидкую фазу направляют в реактор Р2, повышая давление насосом до 30 ата.
Температура в реакторе Р2: на входе 125°С, на выходе 140°С. Конверсия метанола в Р2 - 35%.
Суммарная конверсия метанола за проход в реакционном узле составляет 62%.
Сверху отгонной зоны К1 проводят полную конденсацию парового потока. Часть конденсата возвращают в зону К1 по линии 8 в качестве флегмы, а остальное количество 718 г/ч по линии 7 выводят в составе продукта, содержащего 99,99% ДМЭ и 0,01% метанола.
Сверху ректификационной колонны К2 выводят в количестве 635 г/ч по линии 10 поток метанола, содержащий 1,4% ДМЭ, 97,6% метанола и 1,0% воды, который рециркулируют в реакционный узел.
Снизу колонны К2 выводят в количестве 281 г/ч поток 11. содержащий в основном воду и 0,01% метанола.
Общая конверсия метанола в процессе ~100%.
Пример 5
Переработке подвергают концентрированный метанол согласно фиг.2.
Метанол по линии 1 подают в количестве 1 кг/ч. По линии 10 рециркулируют метанол - дистиллат ректификационной зоны К2.
Реакционная зона Р заполнена 12,0 кг формованного катализатора КИФ (сульфированная смесь сополимера стирола с дивинилбензолом и этиленом) с цилиндрической формой гранул (длина - 2-3 мм, диаметр - 2-3 м), имеющим статическую обменную емкость СОЕ=4,1 мг-эквН+/г.
Смесь потоков 1 и 10, содержащую 0,4% диметилового эфира (ДМЭ), 92,7% метанола и 6,9% воды, в количестве 2685 г/ч подают в реакционную зону Р снизу. В зоне Р поддерживают температуру ~120°С.
В реакционной зоне Р за счет выделения реакционной теплоты происходит частичное испарение образующегося ДМЭ. По линии 3 выводят 537 г/ч газообразного потока, содержащего 73,5% ДМЭ, 23,5% метанола, 3,0% воды. По линии 4 выводят 2148 г/ч жидкого потока, содержащего 15,4% метанола, 63,7% воды, 20,9% ДМЭ.
Конверсия метанола за проход в зоне Р составляет 40%.
Оба потока (3 и 4) направляют в отгонную зону К1 (поток 3 выше потока 4). Осуществляют парциальную конденсацию потока 5, выводимого с верха зоны К1. По линии 6 выводят 719 г/ч потока, содержащего 99,5% ДМЭ и 0,5% метанола.
Сверху ректификационной колонны К2 по линии 10 выводят 1685 г/ч метанольного потока, содержащего 11,0% воды, 0,6% ДМЭ.
Снизу зоны К2 выводят 281 кг/ч воду, содержащую 0,01% метанола.
Общая конверсия метанола в процессе 99,6%.
Пример 6
Переработке согласно фиг.1 подвергают смесь, содержащую 60% метанола, 30% ДМЭ и 10% воды, получаемую из синтеза-газа (смеси СО + Н2).
Смесь подают по линии 1 в количестве 1 кг/ч и первоначально направляют по линии 1б в отгонную зону К1. В зону К1 направляют также поток 3 реакционной смеси из зоны Р1.
Реакционная зона Р1 содержит 1,0 кг сульфокатионита Амберлист-38 производства компании Rohm & Haas. Его статическая обменная емкость СОЕ=5,8 мг-эквН+/г, размер частиц 0,3-1,2 мм.
Поток 10, содержащий 1,3%ДМЭ, 97,7% метанола и 1,0% воды, подают в реакционную зону Р1 сверху и в зоне Р1 поддерживают в жидком состоянии. Температура при входе в Р 125°С, при выходе из Р 160°С.
Конверсия метанола за проход составляет 65%.
Из реакционной зоны Р1 по линии 3 выводят 1596 г/ч смеси, содержащей 46,9% ДМЭ, 34,2% метанола и 18,9% воды, и направляют ее по линиям 3а, 4б в зону К1.
Сверху отгонной зоны К1 выводят паровой поток 5, полностью конденсируют его, и часть конденсата возвращают в зону К1 в качестве флегмы, а остальное количество (1243 г/ч) выводят по линии 7. Поток 7 содержит 99,5% ДМЭ и 0,5% метанола.
Выводимый снизу зоны К1 поток 9 направляют в ректификационную зону К2.
Поток 10, выводимый сверху зоны К2, рециркулируют в реакционную зону Р.
Снизу зоны К2 в количестве 455 г/ч поток 11, содержащий в основном воду и 0,01% метанола.
Общая конверсия метанола в процессе с учетом рецикла составляет 99,4%.
Пример 7
В соответствии с фиг.3 осуществляют переработку концентрированного метанола. Метанол по линии 1 подают в количестве 1,0 кг/ч. Далее половину потока 1 направляют по линии 2а в прямоточную реакционную зону Р, а вторую половину по линиям 2б, 4 и далее и по линиям 4а, 4б и 4в (в равных количествах) направляют в реакционно-ректификационную систему.
В прямоточной реакционной зоне Р размещено 1,5 кг катализатора Амберлист-36 (аналогичного указанному в примере 1), а в реакционной зоне РЗ размещено 10,0 кг катализатора КИФ (аналогичного указанному в примере 2).
Температура при входе в Р 115°С, при выходе из Р 140°С, давление в Р 30 ата.
Конверсия метанола за проход составляет 45%.
Из реакционной зоны Р по линии 3 выводят 500 г/ч жидкой реакционной смеси, содержащей 32,3% ДМЭ, 55,0% метанола и 12,7% воды, которая в сепараторе С дросселируется до давления 11 ата и охлаждается до 110°С. При этом происходит ее частичное испарение. Из сепаратора С выводятся паровая фаза (поток 3а), содержащая 76,7% ДМЭ, 21,1% метанола и 2,2% воды в количестве 125 г/ч, и жидкая фаза (поток 3б), содержащая 17,5% ДМЭ, 66,3% метанола и 16,2% воды в количестве 375 г/ч. Обе фазы из сепаратора направляют в реакционно-ректификационную систему: паровую - по линии 4б, жидкую - по линии 4в.
Сверху укрепляющей зоны УЗ выводят по линии 5 в парообразном состоянии поток, содержащий преимущественно ДМЭ с примесью метанола. Его подвергают парциальной конденсации, и конденсат возвращают по линии 8 в зону УЗ, а несконденсированную часть выводят в количестве 718 г/ч по линии 6. Состав потока 6: 99,5% ДМЭ, 0,5% метанола.
Снизу исчерпывающей зоны ИЗ выводят по линии 9 в количестве 282 г/ч поток, содержащий в основном воду с примесью 0,5% метанола.
Общая конверсия метанола в процессе с учетом рецикла составляет 99,5%.
Пример 8
В соответствии с фиг.3 осуществляют переработку метанола с примесью 5% ДМЭ. Указанную смесь, подаваемую по линии 1 в количестве 1 кг/ч, далее по линии 2б и по линиям 4а, 4б и 4в (в равных количествах) направляют в реакционно-ректификационную систему. В реакционной зоне РЗ размещено 12,0 кг катализатора КИФ (см. пример 2).
Сверху укрепляющей зоны УЗ выводят по линии 5 в парообразном состоянии поток, содержащий преимущественно ДМЭ с примесью метанола. Его подвергают парциальной конденсации, и конденсат возвращают по линии 8 в зону УЗ, а несконденсированную часть выводят в количестве 719 г/ч по линии 6. Состав потока 6: 99,0% ДМЭ, 1,0% метанола.
Снизу исчерпывающей зоны ИЗ выводят по линии 9 в количестве 281 г/ч поток, содержащий в основном воду с примесью 0,1% метанола.
Пример 9
В соответствии с фиг.4 осуществляют переработку концентрированного метанола. Метанол по линии 1 подают в количестве 1,0 кг/ч и далее по линии 2а направляют в прямоточную реакционную зону P1.
В прямоточной реакционной зоне Р размещено 2,0 кг катализатора Амберлист-36 (см. пример 1).
Температура при входе в Р 120°С, при выходе из Р 145°С, давление в Р - 30 ата.
Конверсия метанола за проход составляет 45%.
Из реакционной зоны Р по линии 3 выводят 1000 г/ч жидкой реакционной смеси, содержащей 32,3% ДМЭ, 55,0% метанола и 12,7% воды, которая в сепараторе С дросселируется до давления 11 ата и охлаждается до 100°С. При этом происходит ее частичное испарение. Из сепаратора С выводятся паровая фаза (поток 3а), содержащая 84,3% ДМЭ. 14.4% метанола и 1,3% воды в количестве 137 г/ч, и жидкая фаза (поток 3б), содержащая 24,1% ДМЭ, 61,4% метанола и 14,5% воды в количестве 863 г/ч. Обе фазы из сепаратора направляют в ректификационную колонну К паровую - по линии 4а, жидкую - по линии 4б.
Из нижней части колонны К выводят в количестве 2211 г/ч боковой поток, содержащий 4,9% ДМЭ, 70,4% метанола и 24,7% воды который по линии 10а направляют в прямоточную реакционную зону Р2.
В прямоточной реакционной зоне Р размещено 4,0 кг катализатора Амберлист-36.
Температура при входе в Р 125°С, при выходе из Р 138°С.
Конверсия метанола за проход составляет 35%.
Выводимый сверху колонны К поток конденсируют полностью и по линии 7 выводят 718 г/ч продукта, содержащего 99,5% ДМЭ и 0,5% метанола.
Снизу колонны К по линии 9 выводят в количестве 219 кг/ч воду, содержащую 0,5% метанола.
Общая конверсия метанола в процессе с учетом рецикла составляет 99.5%.
1. Способ получения диметилового эфира из метанолсодержащего потока путем его контактирования с дегидратирующим катализатором в одной или нескольких реакционных зонах и разделения компонентов реакционной смеси с помощью дистилляции и/или ректификации с возвращением непрореагировавшего метанола в реакционную(ые) зону(ы), при котором дегидратацию метанола и образование эфира проводят в жидком и/или парожидкостном состоянии в присутствии кислого катионита при температуре 100 - 160°С и поддерживают концентрацию воды в возвращаемом в реакционную(ые) зону(ы) метанольном потоке менее 12 мас.%, предпочтительно менее 5 мас.%.
2. Способ по п.1, при котором используют метанолсодержащий поток, получаемый в результате химического взаимодействия оксида углерода и водорода, отгонки непрореагировавших исходных веществ и возможно отгонки как минимум части диметилового эфира, причем указанный метанолсодержащий поток подают в реакционную зону и/или последующую зону отгонки диметилового эфира и/или зону ректификации метанола от воды.
3. Способ по п.1, при котором дегидратацию метанола и образование эфира проводят в одной или нескольких реакционных зонах, возможно с подводом или отводом теплоты в реакционных зонах и/или между последовательными реакционными зонами.
4. Способ по п.1, при котором между последовательными реакционными зонами осуществляют промежуточный вывод испаренного(ых) потока(ов), содержащего(их) преимущественно диметиловый эфир.
5. Способ по п.1, при котором метанолсодержащий поток подают в вертикальную реакционную зону снизу, в реакционной зоне проводят частичное испарение потока, сверху выводят в паровой фазе поток, в котором преобладает диметиловый эфир, и выводят в жидкой фазе поток, содержащий преимущественно воду и метанол.
6. Способ по п.1, при котором из жидкой смеси, выводимой из реакционной(ых) зоны(зон), отделяют диметиловый эфир в отгонной зоне, после чего из остающейся смеси выделяют метанол в качестве дистиллата в последующей ректификационной зоне выделения метанола и возвращают его в реакционную(ые) зону(ы).
7. Способ по п.6, при котором в отгонной зоне отделение диметилового эфира от метанола и воды осуществляют ректификацией.
8. Способ по п.7, при котором в указанную отгонную зону предпочтительно выше точки подачи реакционной смеси подают поток(и), содержащий(е) преимущественно диметиловый эфир, выводимый(е) между реакционными зонами и/или сверху реакционной зоны.
9. Способ по п.1, при котором получение диметилового эфира осуществляют в реакционно-ректификационной системе, в которой реакционная зона соединена противоточными потоками жидкости и пара с исчерпывающей и укрепляющей ректификационными зонами, метанолсодержащий поток подают в реакционную зону и/или в верхнюю часть исчерпывающей ректификационной зоны и/или в нижнюю часть укрепляющей ректификационной зоны и сверху указанной укрепляющей зоны выводят поток, содержащий преимущественно диметиловый эфир, а снизу указанной исчерпывающей зоны выводят поток, содержащий преимущественно воду.
10. Способ по п.1, при котором получение диметилового эфира осуществляют в реакционно-ректификационной системе, включающей ректификационную зону и как минимум одну соединенную с ней входящим и выходящим потоками прямоточную реакционную зону, в которую направляют боковой поток указанной ректификационной зоны, предпочтительно выводимый ниже питающего потока, и сверху указанной ректификационной зоны выводят поток, содержащий преимущественно диметиловый эфир, а снизу выводят поток, содержащий преимущественно воду.
11. Способ по п.1, при котором синтез диметилового эфира первоначально осуществляют в прямоточной(ых) реакционной(ых) зоне(ах), а затем в реакционно-ректификационной системе, сверху которой выводят преимущественно диметиловый эфир, а снизу выводят преимущественно воду.
12. Способ по п.1, при котором при синтезе диметилового эфира в прямоточной(ых) реакционной(ых) зоне(ах) используют мелкозернистый сульфокатионит, а при синтезе диметилового эфира в реакционно-ректификационной системе используют сульфокатионитный катализатор с размером частиц не менее 3 мм, предпочтительно имеющий форму цилиндров или массообменной насадки, в частности колец.
13. Способ по п.1, при котором выделяемый поток, содержащий преимущественно диметиловый эфир, подвергают дополнительно водной отмывке от метанола и водно-метанольную смесь подают в зону ректификации от воды и/или в исчерпывающую ректификационную зону реакционно-ректификационной системы.
www.findpatent.ru
Диссертация на тему «Получение диметилового эфира из синтез-газа на базе метанольного производства» автореферат по специальности ВАК 05.17.01 - Технология неорганических веществ
1. Бочкарёв В.В. Перспективные процессы переработки метанола в органические продукты / Бочкарёв В.В., Волгина Т.Н. // Химическая промышленность сегодня. 2008. - № 3. - С. 13 - 17.
2. Кильзие Ф. Тенденции и перспективы мирового рынка метанола. / Кильзие Ф. // Тезисы и доклады Московской международной конференции «Метанол 2006». Москва, - с. 72-84.
3. Смирнова Т. Н. Диметиловый эфир экологически чистое моторное топливо XXI века. Теория и практика внедрения на городском транспорте / Смирнова Т. Н., Захаров С.А. // Автогазозаправочный комплекс. — 2003. - № 3. — С. 69 — 72.
4. Розовский А.Я. Утилизация С02 — потенциальный источник углерода для нефтехимии / Розовский А.Я. // Нефтехимия. 1995. - Т. 35, № 3. - С. 34-42.
5. Розовский А.Я. Физико-химические аспекты утилизации С02 / Розовский А.Я. // Журнал физической химии. 1996. - Т. 70, № 2, С. 199 - 207.
6. Временный технологический регламент установки обезэфиривания метанола-сырца с выделением побочного продукта — ДМЭ. Дополнение к постоянному технологическому регламенту № 51 цеха Синтеза 1-С ПАМ, утв. 04.05.2001г., ОАО HAK «Азот».
7. Установка получения ДМЭ. Рабочий проект. // АООТ «НИАП», г.Новомосковск, 1995, с.56.
8. Brant A. Peppley Methanol-steam reforming on Cu/ZnO/АЬОз catalysts. A comprehensive kinetic mode / Brant A. Peppley, John C. Amphlett, Lyn M. Kearns, Ronald F. Mann // Applied Catalysis A: General, Volume 179, Issues 1-2, 5 April 1999, Pages 31-49.
9. П.Шелдон P.A. Химические продукты на основе синтез-газа. М.:Химия, 1990. С.249.
10. Wang Shou-guo Получение диметилового эфира дегидратацией метанола на катализаторе FLiSiW^O^-I^Os/y-AbOs / Wang Shou-guo, Wang Yuan-hong, Shao Yun, Gong Jian, Qu Lun-yu // Fenzi kexue xuebao=J. Mol. Sei. -2001, -V.17, №2, -P.99-104.
11. Hou Zhao-yin Прямой синтез диметилового эфира на нанесенных Cu-Mn-катализаторах / Hou Zhao-yin, Fei Jin-hua, Qi Gong-xin, Zheng Xiao-ming // Shiyou huagong Petrochem. Technol., -2000, -V.29, №11, -P.819-822.
12. QÍ Gong-xin Влияние марганца на катализаторы Cu/A1203 для гидрирования СО / Qi Gong-xin, Fei Jin-hua, Hou Zhao-yin, Zheng Xiao-ming // Ranliao huax-ue xuebao. J. Fuel Chem. and Technol. -2000. -V.28, №4, -P.382-384.
13. Т.Шикада Синтез диметилового эфира из синтез-газа, полученного из природного газа/Т.Шикада, Ф.Охно, Е.Огава, М.Око, М.Мизугучи, К.Томура, К.Фуджимото//Кинетика и катализ -1999, -Т.40, №3. -С.440-446.
14. Заявка №2002101353/04 Катализатор и способ получения диметилового эфира и метанола из синтез-газа/ Розовский А.Я., Лиин Г.И., Соболевский B.C.; заявлено 01.09.2002; опубл. 10.09.2003.
15. Заявка №97114880/04 Способ получения продукта, содержащего диметило-вый эфир, до 20% по массе метанола и до 20 % по массе воды/ Бодил Фосс, Финн Енсен, Ен Хансен; заявлено 29.01.1996; опубл. 27.01.2000.
16. Xu М. Synthesis of dimethyl ether from methanol over solid-acid catalysts / Xu M., Lunsford J.H., Goodman D.W., Bhattachaiyya A. // Applied Catalysis A: General, -1997, -V.149, №2, P.289-301.
17. Xu M. Catalytic dehydration of methanol to dimethyl ether over Pd/Cab-O-Sil catalysts / Xu M., Goodman D.W., Bhattacharyya A. // Applied Catalysis A: General, -1997, -V.149, №2, P.303-309.
18. Co-production of dimethyl ether and methanol from C02 hydrogénation: development of a stable hybrid catalyst / Tao Jia-Lin, Jun Ki-Won, Lee Kyu-Wan // Appl. Organomet. Chem., -2001, -V.15, №2, P.105-108.
19. Zheng Jingzhi Изучение каталитического синтеза диметилового эфира из метанола с использованием модифицированного каолина / Zheng Jingzhi, Мао Liqiu, Yin Dulin, Yin Dulin, Wen Bin, Zhang Juewu, Gan Jun//Hunan hua-gong, -2000, -V.30, V.l, P.9-10.
20. Chen Song-zhe Лазеро-стимулированные поверхностные реакции метанола на гетерополисоединениях / Chen Song-zhe, Zhong Shun-he, Xin Xiu-lan, Xiao Xiu-fen//Fenzi cuihua=J. Mol. Catal. (China), -2001, V.l5, №5, -P.321-326.
21. J.S.Lee Methyl formate as a new building block in CI chemistry / J.S.Lee, J.C.Kim, Y.G.Kim // Appl. Catal., -1990, V.57, №1, P.l-30.
22. Linghu Wen-sheng Исследование активности щелочно-метоксидных катализаторов карбонилирования метанола / Linghu Wen-sheng, Liu Zhen-yu,137
23. Zhong Bing, Li Yong-wang// Ranliao huaxue xuebao=J. Fuel Chem. and Tech-nol.,-2000, V.28, №3, P.233-238.
24. Патент США №1400195, Process of making methyl formate / Willkie, Herman F.; 13.12.1921.
25. Патент США №1975853 Catalytic dehydrogenation of primary alcohols / Lazier, Wilbur A.; 09.10.1934.
26. Патент США №2160064 Manufacture of formic acid / Eversole, James F.; 30.05.1939
27. Патент США №4778923 Process for the production of methyl formate / Aplin Richard P; 18.10.1988.
28. Патент США №4149009 Process for producing methyl formate / Yoneoka Mikio; 10.04.1979.
29. Патент США №5144062 Process for producing methyl formate / Chen Shien-Chang; 1.09.1992.
30. Патент США №4480122 Process for producing methyl formate / Horlenko; 30.10.1984.
31. M. Ai Dehydrogenation of methanol to methyl formate over copper-based catalysts / M. Ai //Applied Catalysis, -1984, -V.l 1, №2, -P,259-270.
32. Патент США 5194675 Preparation of methyl formate / Joerg; Klaus, Mueller; Franz-Josef, Irgang; Matthias, Marosi; Laszlo, Borchert; Gerhard; 16.03.1993.
33. Патент №2875172, Получение формальдегида. Мисоноо Макото, Ямамото
34. Такэси, Порипарасутиккусу, Заявл. 20.12.1985. Опубл. 10.11. 1987. Япония.
35. Патент №6410793, Способ получения формальдегида из метанола. Janear Stefan, Bodajla Michal Kondelka, Ladislav Butkovsky Ludovit, Ridarsky Andrej, Kovac Jozef, Vasil Pavol, Заявл. 01.07.1981. ЧССР.
36. Патент №4544773, Способ получения формальдегида. Masakazu Sagou, Заявл. 22.06.1984. Опубл. 1.10.1985, Япония.
37. Патент №4420641, Получение формальдегида. Gerberich Robert М., Smith Elgred Т., Заявл. 12.01.1983. Опубл. 13.12.1983, США.
38. Патент №3485543, Катализатор для окисления метанола в формальдегид. Хохлер Р.Я., Курина Л.Н., Кудрина Н.В., Заявл. 18.05.1982. СССР, Томск.
39. Wu Jing-Tao Изучение мембранного катализа. 1. Производство формальдегида с помощью каталитического дегидрирования метанола в реакторе с палладием на керамической мембране / Wu Jing-Tao, Deng Jing-Fa // Acta chim. Sim., -1993, № 5, -P.475-480.
40. Патент №4439624, Конверсия диметилового эфира в формальдегид над Bi-Mo-Cu катализатором. Lewis Robert М, Ryan Robert С., Slaugh Lynn H., Заявл. 7.10.1982. Опубл. 27.03.1984, США.
41. Авторское свидетельство Лапидус А.Л., Третьяков В.Ф., Бурдейная Т.Н., Голубева И.А., Ковалева Н.И. Каталитическое неокислительное дегидрирог вание метанола в формальдегид.
42. Rinaldo S. A mechanistic study of the methanol dehydration reaction on y-alumina catalyst / Rinaldo S. Schiffino, Robert P. // J. Phys. Chem. -1993, -P.6425-6435.
43. Choi Y. Fuel cell grade hydrogen from methanol on a commercial Cu/Zn0/A1203 catalyst / Choi Y., Stenger H.G. // Applied Catalysis B: Environmental, -2002, -V.38, №4, -P.259-269.
44. Розовский А.Я. Механизм и кинетика реакций одноуглеродных молекул на Си-со держащих катализаторах / Розовский А .Я. // Кинетика и катализ. -2003, -Т.44, №3, -С.391-411.
45. Ионе К.Г. Синтезы углеводородов из соединений, содержащих один углеродный атом, с применением бифункциональных цеолитных катализаторов / Ионе К.Г., Степанов В.Г., Романников В.Н., Шепелев С.С. // Химия твёрдого топлива, -1982, №6, С. 35-50.
46. Патент №2220939 Комплексный способ получения диметилового эфира из углеводородных газов/ Розовский А.Я., Лин Г.И., Кубиков В.Б., Майдуров > Н.П., Петров В.Н., Брандт Б.Б., Махлин В.А.; заявлено 09.01.2002; опубл. 10.01.2004.
47. Патент №1173696 Способ получения диметилового эфира / Ионе К.Г., Мысов В.М. и др.; заявлено 03.03.1983; опубл. 10.03.1997, бюл. №7.
48. Заявка №97114880/04 Способ получения простого диметилового эфира, применяемого в качестве топлива/ Бодил Фосс, Финн Енсен, Ен Хансен; заявлено 03.09.1997; опубл. 20.06.1999.
49. Синицына О. А. Кинетика дегидратации метанола до диметилового эфира на СВК цеолите / Синицына О. А., Чумакова В. Н., Московская Н. Ф. // Кинетика и катализ- 1986-Т. 27. №5-с. 1160-1165.
50. J.-L. Li Inui Synthesis of dimethyl ether under forced composition cycling / J.-L. Li, X. G Zhang, T. // Applied Catalysis A: General 164 (1997) 303-311.
51. Аэров М.Э., Тодес O.M., Наринский Д.А. Аппараты со стационарным слоем: гидравлические и тепловые основы работы. Л.: Химия, -1979. -176С.
52. Попов И.Г. Термодинамическое равновесие реакций образования диметилового эфира и метанола из оксидов углерода и водорода / И.Г. Попов, Л.Ф.140
53. Решетняк, А.С. Шмелёв, B.C. Соболевский // Химическая промышленность,-2000, №7, -С. 29-32.
54. Popov B.I. Effect of excess molybdenum trioxide on the activity and selectivity of some molybdates in methanol oxidation / Popov B.I., Shkuratova L.N., Orlova L.B. // React. Kinet. Catal. Lett., -1976, -V.4, №3, -P.323-328.
55. Горшков C.B. Механизм дегидрирования метанола в метилформиат и пути управления селективностью процесса / Горшков С.В., Лиин Г.И., Розовский А .Я. // кинетика и катализ, -1999, -Т.40, №3, С.372-375.
56. Minyukova Т.Р. Dehydrogenation of methanol over copper-containing catalysts / Minyukova T.P., Simentsova 1.1., Khasin A.V., Shtertser N.V., Baronskaya N.A., Khassin A.A., Yurieva T.M. // Applied Catalysis A: General, -2002, -V.237, №12, P.171-180.
57. Матышак В.А. Поверхностные соединения в системе метилформиат-метанол-диметиловый эфир-уА1203 по данным ИК-спектроскопии IN SITU / Матышак В.А., Хоменко Т.И., Лиин Г.И., Завалишин Н.И., Розовский А.Я. // Кинетика и катализ, -1999, -Т.40, №2, С.295-301.
58. Шлегель Л. Разложение метанола на Cu-содержащих катализаторах синтеза метанола / Шлегель Л., Гутшик Д., Розовский А.Я. // Кинетика и катализ. -1990, -Т.31, №4, С. 1000-1003.
59. Takagi К. Catalytic Activation of Coppers in the Various Oxidation States for the Dehydrogenation of Methanol / Takagi K., Morikawa Y., Ikawa T. // Chemistry Letters, -1985, №4, P.527-530.
60. Kobayashi H. Dispersion of Copper Supported on Silica and Methanol Reforming Reaction / Kobayashi H., Takezawa N., Minochi C., Takahashi K. // Chemistry Letters, -1980, №10, P.l 197-1200.
61. Курина Л.Н. Взаимодействие участников реакции окисления метанола с окислами Ti, Mo, Fe. / Курина Л.Н., Герасимова В.Н., Давыдов А.А., Судако-ва Н.Н. //Теор.Экспер.химия, 1981, Т17, №5, С713-718.
62. Gorazd Bercic Intrinsic and Global Reaction Rate of Methanol Dehydration over у-АЬОз Pellets / Gorazd Bercic, Janez Levee // J.Ind.Eng.Chem., -1992, -V.31, -P.1035-1040.
63. Zhaoguang Nie Intrinsic Kinetics of Dimethyl Ether Synthesis from Syngas / Zhaoguang Nie, Hongwei Liu, Dianhua Liu, Weiyong Ying, Dingye Fang // Journal of Natural Gas Chemistry, -2005, -V.14, №1, -P.22-28.
64. Ali Hadipour Kinetic Parameters and Dynamic Modeling of Reactor for Direct Conversion of Synthesis Gas to Dimethyl Ether / Ali Hadipour, Morteza Sohrabi // J.Ind.Eng.Chem., 2007, Vol. 13, № 4, P. 558-565.
65. K.L. Ng Kinetics and modelling of dimethyl ether synthesis from synthesis gas / K.L. Ng, D. Chadwick, B.A. Toseland // Chemical Engineering Science, -1999, -V.54, № 15-16, -P.3587-3592.
66. Graaf G.H. Chemical equilibria in methanol synthesis / G. H. Graaf, P. J. J. M. Sijtsema, E. J. Stamhuis, G. E. H. Joosten // Chem.Eng. Science, -1986, -V.41, № 11, -P.2883-2890.
67. Graaf G.H. Intra-particle diffusion limitations in low-pressure methanol synthesis / G. H. Graaf, H. Scholtens, E. J. Stamhuis, А. А. С. M. Beenackers.// Chem.Eng. Science, -1990, -V.45, № 4, -P.773-783.
68. Сосна M.X. О выборе кинетического уравнения реакции дегидратации метанола до ДМЭ на промышленном катализаторе / Сосна М.Х., Соколинский Ю.А., Королёв Е.В.// Хим. пром-сть сегодня. -2008, № 7, -С.6-12.
69. Патент №6458856 Процессы разделения при одностадийном получении диметилового эфира из синтез-газа / Peng, Xiang-dong, Diamond, Barry W., Tsao, Tsun-chiu Robert, Bhatt, Bharat Lajjaram,; заявлено 11.07.2001; опубл. 01.10.2002.
70. Патент №3449249/23-04 Способ получения диметилового эфира/ Джованни Манара; заявлено 01.06.1982; опубл. 07.08.1987. Бюл. №29.
71. Патент №2857788/23-04 Способ получения диметилового эфира/ Ионе Г.К., Носырева Г.Н., Вострикова Л.А., Леонов В.Е, Герич А.П., Топчий, В.А.; заявлено 19.12.1979; опубл. 07.05.1982. Бюл. №17.
72. Патент №2190954/23-04 Способ получения простых эфиров/ Витторио Фат-торе, Джованни Манара, Бруно Нотари; заявлено 20.11.1975; опубл. 23.06.81. Бюл. №23.
73. Патент №2556955/23-04 Способ получения диметилового эфира/ Джованни Манара, Бруно Нотари, Витторио Фатторе; заявлено 22.12.1977; опубл. 15.03.1982. Бюл. №10.
74. Патент №27478125/23-04 Способ совместного получения N-метилморфолина и диметилового эфира/ Николаенко Ю.А., Попов A.B., Горбунов Б.Н., Царенко C.B., Новикова C.JL, Сивкова Р.И.; заявлено 06.04.1979; опубл. 30.04.1981. Бюл. №16.
75. Патент №2748629/23-04 Способ совмещённого получения морфолина и диметилового эфира/ Николаенко Ю.А., Попов A.B., Горбунов Б.Н., Царенко C.B., Новикова С.Л., Сивкова Р.И.; заявлено 06.04.1979; опубл. 07.01.1981. Бюл. №1.
76. Патент №200232017/04 Способ получения диметилового эфира/ Павлов Д.С., Павлов О.С., Телков Ю.К.; заявлено 28.11.2002; опубл. 20.07.2005.
77. Патент №1978809/23-04 Способ получения диметилового эфира / Джорд-жио Пагани; заявлено 20.12.1972; опубл. 15.05.1982. Бюл. №18.
78. Е.И. Бункина Разработка технологического процесса получения диметилового эфира с использованием бифункционального катализатора / Е.И. Бункина, А.П. Какичев, A.A. Лендер, Н.П. Павлова//Хим.пром.,1999, №3 (145). С10-15.
79. Патент США №6608114 Process to produce DME / Heydorn; Edward C., Bhatt; Bharat Lajjaram, Diamond; Barry W.; заявлено 13.03.2002. опубликовано 19.08.2003.,
80. Элвин Б. Стайлз. Носители и нанесенные катализаторы. М.:Химия, -1991. -С. 240
81. Kolbel H.The Fischer-Tropsch Synthesis in the Liquid Phase / Kolbel H., Ralek M.//Catal.Rev.Sci.Eng. -1980, -V.21, №2, -P.225.
82. Dry M.E. Practical and theoretical aspects of the catalytic Fischer-Tropsch process / Dry M.E. //Appl.Catal.A: Gen. -1996, -V.138, №2, -P.319.
83. Guy Schmitz, Deshydratation dy methanol sur silice-alumine, / Guy Schmitz // Journal de chimic physique. -1978. -V.75, №6, -P.650-655
84. Бесков B.C., Флокк В., Моделирование каталитических процессов и реакторов. М.: Химия, 1991, с. 256.
85. Rinaldo S. Schiffino A mechanistic study of the methanol dehydration reaction on y-alumina catalyst / Rinaldo S. Schiffino, Robert P. Merrill // J. Phys. Chem. -1993. -V.97, №24, -P. 6425-6435.
86. Choi Y. Fuel cell grade hydrogen from methanol on a commercial Cu/Zn0/A1203 catalyst / Choi Y., Stenger H.G. // Applied Catalysis B: Environmental, -2002, -V.38, №4, -P.259-269.
87. Горшков C.B. Механизм дегидрирования метанола в метилформиат и пути управления селективностью процесса / Горшков C.B., Лиин Г.И., Розовский А .Я. // кинетика и катализ, -1999, -Т.40, №3, -С.372-375.
88. Розовский А.Я., Лин Г.И. Теоретические основы процесса синтеза метанола. -М.: Химия, -1990. С. 160.
89. Караваев M. М., Леонов В. Е., Попов И. Г. Технология синтетического метанола. -М.: Химия, 1984. С.240.
90. A. Jonasson, О. High Pressure Solubility of Carbon Dioxide and Carbon Monooxyde in Dimethyl Ether / A. Jonasson, O. Persson, A. Fredenslund // J.Chem.Eng.Data, -1995, №40, -P.296-300.
91. P. Рид, Дж. Праусниц, Т. Шервуд. Свойства газов и жидкостей: Справочное пособие. Л.: Химия, 1982. 592 с.
92. М.А. Берлин, В.Г. Гореченков, Н.П. Волков. Переработка нефтяных и природных газов. М.: Химия, 1981. 472 с.
93. Г.С. Борисов, В.П. Брыков, Ю.И. Дытнерский и др. Под ред. Ю.И. Дыт-нерского. Основные процессы и аппараты химической технологии: Пособие по проектированию. М.: Химия, 1991. 496 с.
94. Гороновский И.Т., Назаренко Ю.П., Некряч Е.Ф. Краткий справочник по химии. — Киев: издательство Академии наук Украинской ССР, 1962. — 569 с.
95. Нормируемые показатели точности измерений в методиках выполнения измерений, регламентированных в документации на химическую продукцию. МУ 6/113-30-19-83. -М., 1983. 52 с.
96. Дерффель К. Статистика в аналитической химии. — М.: Мир, 1994. — 268с.
97. Расчёт эффективности ректификационной тарелки по Мерфри
98. Данная модельная система, рассматривается аналогично схеме, представленной в разделе 2.5.2.1.
99. Расчёт параметров модельной системы Для расчета параметров модельной системы используем данные по работе промышленной установки в режиме вывода инертов из сборника флегмы.
100. Приход ДМЭ: Бдмэ = 385 кг/ч = 385 / 46 = 8,37 кмоль / ч.
101. Мольная доля С02 в питании: Nco2 = 0,9 / 10 = 0,09.
102. Мольная доля ДМЭ в питании: Ыдмэ = 8,37 / 10 = 0,84.
103. Мольная доля инертов в питании: NHHepT = 0,68 / 10 = 0,07.
104. Поток флегмы Ф = 18 т/ч = 18000 / 46 = 390 кмоль/ч.
105. Поток жидкости в колонне L = Ф = 390 кмоль/час = 390/3600 = 0,108 кмоль/с.
106. Средняя молярная масса пара и жидкости Мх ~ Му ~ 46 кг/кмоль. Плотность паровой фазы:ру = Му-Р/(8,314-Т-1000) = 46-1Д • 10б/(8,314-(273+40> 1 ООО) = 19,4 кг/м3.1. Рабочее сечение тарелки:
107. FPa6 = f-0,785-D2 = 0,874-0,785-1,082 = 0,8 м2.
108. Скорость пара в рабочем сечении тарелки:wm = 1000-G-8,314-T/(P- Fpa6) = 1000-0,111-8,314-(273+40)/(1,1-106-0,8) = = 0,328 м/с.
109. Массовый расход жидкости: LM = L- Мх = 0,108-46 = 4,97 кг/с.
110. Плотность жидкой фазы принимаем равной плотности жидкого ДМЭ при температуре 40 °С: рх = 629,2 кг/м3.
111. Удельный расход жидкости на 1 м ширины сливной перегородки: q = LM/(b- рх) = 4,97/(0,7-629,2) = 0,0113 м2/с.
112. Вязкость, поверхностное натяжение жидкой фазы принимаем равными вязкости, поверхностному натяжению жидкого ДМЭ при температуре 40 °С: (ix = 0,130 мПа-с; <тх = 0,01 Н/м.
113. Вязкость воды при температуре 40 °С:1. Ojeo 0,0696 Н/м.
114. Высота светлого слоя жидкости:1. Л,09
115. Л2 056 (0,05-4,60,1) (-0,110,13) ( 0,01 Л nnpu h() = 0,7870,01l¥,Z 0, Г"30 0,328 J (\-0,31е J) —- =0,08141. V. 0,0696)01. Критерий Фруда:
116. Fr = wm2/(9,81-/70) = 0,3282/(9,81 -0,0814) = 0,135. Паросодержание барботажного слоя:1. Jñ = JW .1 + 1 + J 0,135 Плотность орошения:
117. U = Lм/( Fpa6 • рх) = 4,97/(0,8-629,2) = 0,00987 м3/м2-с.
118. Коэффициент диффузии в паровой фазе для системы ДМЭ С02 при 40 °С: = 0,118-10-7 м2/с.
119. Коэффициент диффузии в жидкой фазе для системы ДМЭ С02 при 40 °С и 1,1 МПа:1. Бу = 0,866-10"6 м2/с.
120. Вязкость паровой фазы принимаем равной вязкости газообразного ДМЭ при температуре 40 °С: цу = 0,00975 мПа-с.
121. Коэффициент массоотдачи для жидкой фазы:0 5/ \0>5 / \0>51.п ПППО'7 \ / Л ЛЛП7С \0,08146,24105 (0,11810~7)0,009870,009750,00975+0,130)1. А-0,269)
122. Коэффициент массоотдачи для паровой фазы:0,5 г п г ЛЛЛЛ„ \0,50,169 м/с.р 6,24105 0,04 (0,86610'6)0,328 0,269)0,08140,009750,00975+0,130)0,551 м/с.
123. Среднее значение константы межфазового равновесия в пределах концентраций С02 0,1 -3 (% мольн.) при 40 °С и 1,1 МПа: ш = 3,54.л
124. Пересчет коэффициентов массоотдачи на кмоль/м -с: рхг = 0,169-р Х/МХ = 0,169-629,2/46 = 2,31 кмоль/м2-с Рз*=0,551-ру/Му =0,551- 19,4/46 = 0,232 кмоль/м2-с. Коэффициент массопередачи:
125. Ку£ = 1 /(1 /руГ+ш/рхГ)= 1 /(1 /0,232 + 3,54/2,31) = 0,171 кмоль/м2-с.
126. Общее число единиц переноса:поу = КугМу/( ру- шт) = 0,171-46/(19,4-0,328) = 1,24.1. Локальная эффективность:
127. Еу = 1 ехр(-поу) = 1 - ехр(—1,24) = 0,71.1. Фактор массопередачи:
128. X = т-в/Ь = 3,54-400/390 = 3,63.1. Фактор скорости:= = 0,328- ЩТ=1,4Л.
129. При данном значении Б принимаем долю байпасирующей жидкости 0 = 0,1. Число ячеек полного перемешивания Б определим как отношение длины пути жидкости на тарелке 1х к длине, соответствующей одной ячейке (-350 мм): 8 = 1Т / 350 = 830 / 350 = 2,37 ~ 2.
130. Коэффициент, учитывающий влияние свойств жидкости и пара на унос:т' = 1,15 100,295 . .0,425а \ ( о р \г X г ур
www.dissercat.com
СПОСОБ ПОЛУЧЕНИЯ ДИМЕТИЛОВОГО ЭФИРА
Данное изобретение относится к способу получения диметилового эфира из метанольного исходного сырья. В частности, изобретение обеспечивает каталитическую конверсию метанольного исходного сырья в охлаждаемом газом реакторе получения диметилового эфира с помощью непрямого теплообмена с охлаждающим газом, пропускаемым через этот реактор прямотоком к направлению потока реагирующего исходного метанольного сырья.
Изобретение служит для решения проблемы, связанной с вредным образованием углерода на поверхности катализатора в процессе реакции дегидратации метанола до диметилового эфира, причем проблема решается за счет охлаждения этой реакции, чтобы снизить или избежать образования углерода на катализаторе.
В соответствии с этим, настоящее изобретение в своем самом широком варианте осуществления представляет собой способ получения диметилового эфира, включающий стадии:
a) обеспечения содержащего метанол исходного сырья;
b) введения исходного сырья в реакционную зону внутри охлаждаемого газом реактора получения диметилового эфира и прохождения исходного сырья через реакционную зону;
c) введения потока охлаждающего газа в охлаждающее пространство внутри охлаждаемого газом реактора получения диметилового эфира;
d) реагирования исходного сырья в реакционной зоне в присутствии катализатора, активного в отношении дегидратации метанола до диметилового эфира, с получением выходящего из реактора потока, содержащего диметиловый эфир;
e) прохождения потока охлаждающего газа через охлаждающее пространство в условиях непрямого теплообмена с исходным сырьем в реакционной зоне, при этом поток охлаждающего газа является прямотоком к направлению потока исходного сырья в реакционной зоне.
Подходящий реактор для применения в способе согласно изобретению содержит внутри общего корпуса множество катализаторных трубок, образующих реакционное пространство. Эти трубки располагаются на расстоянии друг от друга, чтобы оставить место для охлаждающего пространства. Тогда охлаждающий газ вводится в межтрубное пространство катализаторных трубок в охлаждающем пространстве и движется вдоль этого межтрубного пространства в условиях теплообмена с реагирующим газом в трубном пространстве этих катализаторных трубок. За счет этого процесса реагирующий газ охлаждается до температуры ниже критической температуры для образования углерода.
В другом варианте осуществления изобретения поток охлаждающего газа, используемый в реакторе, формируется с помощью исходного метанольного сырья, которое после испарения вводится в охлаждающее пространство реактора.
При использовании исходного сырья в качестве потока охлаждающего газа предпочтительно после охлаждения реакции дегидратации вводить этот поток в реакционную зону в качестве исходного сырья для реакции дегидратации метанола.
В другом варианте осуществления изобретения исходное метанольное сырье перед введением в реакционную зону предварительно нагревается путем непрямого теплообмена с потоком охлаждающего газа, отведенным из охлаждающего пространства, и это предварительно нагретое исходное сырье перед введением в реакционную зону дополнительно нагревается вторым горячим потоком газа.
В последнем варианте осуществления предпочтительно, чтобы второй горячий поток газа представлял собой выходящий реакционный поток из работающего в адиабатическом режиме каталитического реактора для конверсии метанола в диметиловый эфир.
При использовании реактора, работающего в адиабатическом режиме, поток исходного сырья для этого реактора предпочтительно представляет собой выходящий реакционный поток из охлаждаемого газом реактора получения диметилового эфира, поступаемый в этот адиабатический реактор получения диметилового эфира для дальнейшей адиабатической конверсии непрореагировавшего метанола в этом выходящем потоке в присутствии катализатора, активного в отношении конверсии метанола в диметиловый эфир, с целью получения выходящего потока из реактора получения диметилового эфира, работающего в адиабатическом режиме.
Катализаторы, подходящие для применения в данном изобретении, по существу, известны в уровне техники и предпочтительно выбираются из группы твердых кислот, включая оксид алюминия, алюмосиликаты или смесь этих соединений.
Изобретение раскрывается более подробно со ссылкой на чертеж, где на Фиг.1 показана упрощенная технологическая схема способа получения диметилового эфира в соответствии с одним вариантом осуществления данного изобретения.
В этом варианте осуществления поток жидкого исходного метанольного сырья подается по линии 2 в испарительную установку 4 и испаряется с переходом в газообразную форму. Этот поток газообразного исходного метанольного сырья затем направляется по линии 6 в первый теплообменный аппарат 8.
В первом теплообменном аппарате поток газообразного метанола предварительно нагревается до 220°С путем непрямого теплообмена с горячим потоком газообразного метанола 20, который служил в качестве охлаждающего газа в охлаждаемом газом реакторе 16 получения диметилового эфира, который дополнительно описан ниже.
Предварительно нагретый поток метанола вводится через линию 10 во второй теплообменный аппарат 12. В теплообменном аппарате 12 этот предварительно нагретый поток метанола дополнительно нагревается до 260°С путем непрямого теплообмена с горячим потоком продукта - диметилового эфира, выходящим из работающего в адиабатическом режиме реактора 28 получения диметилового эфира при 336°С.
Нагретое таким образом исходное метанольное сырье потом вводится через линию 14 в верхней секции охлаждаемого газом реактора 16 в охлаждающее пространство 18. Это охлаждающее пространство образуется между трубками реактора 24 в их межтрубном пространстве.
При введении в охлаждающее пространство газообразный поток исходного метанольного сырья применяется в качестве охлаждающего газа и пускается прямотоком к направлению потока реагирующего исходного метанольного сырья в трубках 24. Таким образом, газ охлаждает реакцию дегидратации метанола, происходящую на катализаторе, расположенном внутри трубок 24. Охладив реакцию путем непрямого теплообмена, газообразное метанольное сырье отводится при температуре 320°С из охлаждающего пространства 18 в нижней части реактора 16 через линию 20.
Этот подведенный поток, отслуживший в качестве охлаждающего газа, затем вводится в теплообменный аппарат 8, чтобы предварительно нагреть поток исходного сырья из линии 6, как описано выше, и за счет этого охлаждается до 270°С.
Затем охлажденное исходное сырье подается в реактор 16 по линии 22 и вводится в верхней части реактора в реакционную зону, образованную множеством катализаторных трубок 24.
В реакционной зоне метанол в потоке исходного сырья каталитически дегидратируется с получением газа, обогащенного диметиловым эфиром. Участвующий в реакции поток исходного сырья проходит прямотоком к направлению потока охлаждающего газа в межтрубном пространстве, и тем самым охлаждается путем непрямого теплообмена с охлаждающим газом. Выходящий из реактора поток, обогащенный диметиловым эфиром, отводится при 329°С из нижней части реактора и через линию 26 подается в адиабатический реактор 28, необязательно после охлаждения в теплообменном аппарате (не показан).
Реактор 28 снабжен неподвижным слоем катализатора дегидратации метанола 30, и оставшиеся количества метанола в выходящем из реактора 16 потоке конвертируются в адиабатических условиях в диметиловый эфир.
Прежде чем продукт, обогащенный диметиловым эфиром, собирается посредством линии 34, этот продукт отводится из реактора 28 при температуре 336°С и проходит с помощью линии 32 через теплообменный аппарат 12, чтобы нагреть исходное метанольное сырье, как описано выше.
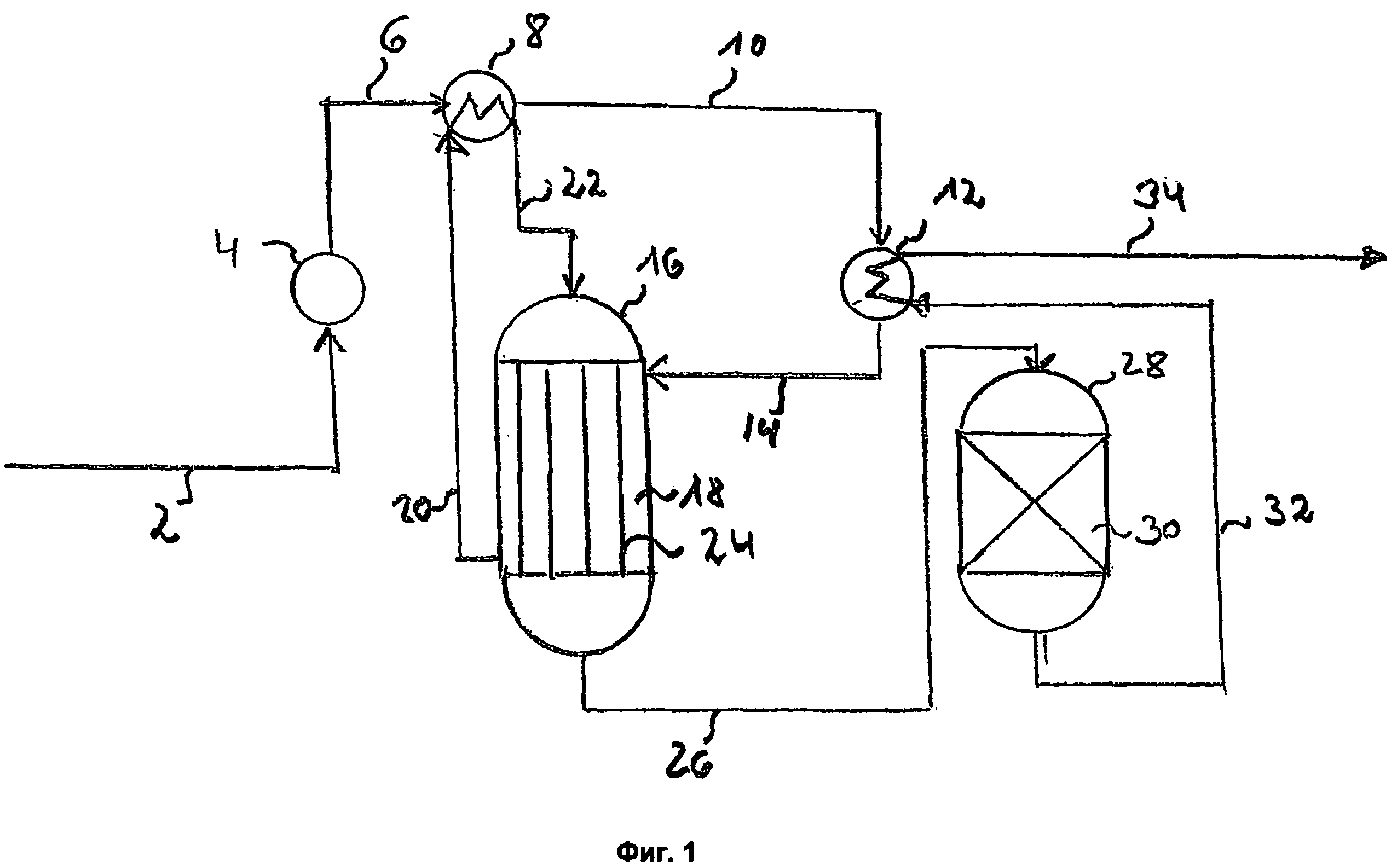
edrid.ru
Способ получения диметилового эфира из метанола
Настоящее изобретение относится к способу получения диметилового эфира, применяемого в качестве хладагента и газа вытеснителя аэрозольных упаковок, из метанола. Способ заключается в контактировании метанола с дегидратирующим катализатором в реакционной зоне и разделении компонентов реакционной смеси с помощью ректификации с возвращением непрореагировавшего метанола в реакционную зону, при котором дегидратацию метанола и образование эфира проводят в присутствии катализатора при повышенной температуре. При этом в качестве катализатора применяют молекулярные сита цеолитного типа с крупными порами, выбранные из группы, состоящей из цеолитов структуры FAU, являющихся цеолитами типа X и их модификациями, дегидратацию осуществляют в газообразном состоянии при температуре в реакционной зоне 280÷330°C и давлении 17÷22 атм, в первой ректификационной колонне отгоняют от воды фракцию, состоящую из метанола и диметилового эфира, во второй ректификационной колонне отгоняют от непрореагировавшего метанола диметиловый эфир и возвращают метанол в реакционную зону. Способ позволяет получить диметиловый эфир с высокими выходом и чистотой. 1 ил., 1 табл., 4 пр.
Область техники
Данное изобретение относится к химической промышленности, конкретно к области получения диметилового эфира (ДМЭ), применяемого в качестве хладагента и газа вытеснителя аэрозольных упаковок.
Качество очистки газа вытеснителя определяет его использование в тех отраслях, где очень высоки требования к газу по содержанию меркаптанов и влаги (парфюмерно-косметическая продукция, медицинские аэрозоли, производство автокосметики, монтажной пены, лакокрасочной продукции).
Уровень техники
Известно достаточно много процессов, в которых ДМЭ получают дегидратацией метанола с использованием различных катализаторов.
Согласно патенту [1] [патент RU 2459799, С2, дата публикации 27.08.2012 г.] в качестве катализаторов могут использоваться молекулярные сита цеолитного и/или нецеолитного типов. В качестве молекулярных сит используются одно или несколько сит, с FAU структурой, выбранных из группы, состоящей из цеолитов Y-типа, которые имеют большие поры. Молекулярное сито нецеолитного типа может быть силикоалюмофосфатным.
К недостаткам указанного способа следует отнести высокую склонность к косообразованию катализаторов при температуре реакции.
В патенте [2] [патент RU 2282613, С2, дата публикации 27.08.2006 г.] дегидратацию метанола проводят в присутствии сульфоионитного катализатора при повышенной температуре и давлении в совмещенном реакционно-ректификационном аппарате.
Наиболее близким по своей технической сущности и достигаемому техническому результату является изобретение «Способ получения диметилового эфира» [3], [патент RU №2256645, С2, дата публикации 20.07.2005 г.]. Согласно данному изобретению метанолсодержащий поток контактирует с дегидратирующим катализатором в одной или нескольких реакционных зонах. Компоненты реакционной смеси с помощью дистилляции и/или ректификации разделяют с возвращением непрореагировавшего метанола в реакционную зону. Дегидратацию метанола и образование эфира проводят в жидком и/или парожидкостном состоянии в присутствии кислого катионита при температуре 100-460°C и поддерживают концентрацию воды в возвращаемом реакционную зону метанольном потоке менее 12% масс, предпочтительно менее 5% масс.
Основными недостатками прототипа являются:
- применение двухреакторной схемы для дегидратации;
- применение водной отмывки выделенного потока диметилового эфира от метанола и подача воднометанольной смеси в зону ректификации от воды;
- применение реакционно-ректификационного аппарата приведет к усложнению технологической схемы.
Задача предлагаемого способа заключается в создании экологически чистой технологии получения ДМЭ дегидратацией метанола на молекулярном сите цеолитного типа, которая позволит получить продукцию необходимого качества для использования ее в качестве газа вытеснителя аэрозольных упаковок и значительно снизить эксплуатационные и капитальные затраты на реализацию и проведение процесса.
Раскрытие изобретения
Поставленная задача достигается тем, что в способе получения диметилового эфира из метанола, путем его контактирования с дегидратирующим катализатором в реакционной зоне и разделении компонентов реакционной смеси с помощью ректификации с возвращением непрореагировавшего метанола в реакционную зону, при котором дегидратацию метанола проводят в присутствии катализатора при повышенной температуре, в отличие от прототипа, в качестве катализатора применяют молекулярные сита цеолитного типа с крупными порами, выбранные из группы, состоящей из цеолитов структуры FAU, являющихся цеолитами типа X и их модификациями, дегидратацию осуществляют в газообразном состоянии при температуре в реакционной зоне 280÷380°C и давлении 17÷22 атм, в первой ректификационной колонне отгоняют от воды фракцию, состоящую из метанола и диметилового эфира, во второй ректификационной колонне отгоняют от непрореагировавшего метанола диметиловый эфир и возвращают метанол в реакционную зону. Предлагаемый способ получения диметилового эфира осуществляется на установке, которая представлена на чертеже, где приведена принципиальная схема установки.
Установка работает следующим образом.
Для получения ДМЭ используют метанол концентрации не менее 99,5%, массовая доля серы не более 0,0001%, массовая доля воды не более 0,05%, массовая доля альдегидов и кетонов не более 0,003%.
Согласно схемы установки на чертеже метанол поступает по линии 1. Его смешивают с рециркулируемым метанольным потоком 11, поступающим из куба колонны 14, подогревают в теплообменнике до температуры 300-350°C и по лини 2 направляют в реакционную зону реактора 12, содержащую цеолит типа X. Из реакционной зоны реактора 12 по линии 3 выводят реакционную смесь, которую подают в отгонную зону колонны 13 по линии 3. Отгонная зона колонны 13 представляет собой ректификационную колонну.
Сверху ректификационной колонны 13 по линии 5 выводят паровой поток, содержащий преимущественно ДМЭ и метанол. Далее поток охлаждается в конденсаторе дефлегматоре и поступает в колонну 14 по линии 7. Часть сконденсированного потока по линии 6 возвращают в колонну 13 в виде флегмы. Снизу колонны 13 по линии 4 выводят поток, содержащий преимущественно воду. Ректификационная колонна 14 предназначена для разделения ДМЭ от метанола. Сверху ректификационной колонны 14 по линии 8 выводят паровой поток, содержащий ДМЭ. Далее поток охлаждается в конденсаторе дефлегматоре и поступает по линии 10 на склад. Часть сконденсированного потока по линии 9 возвращают в колонну 14 в виде флегмы. Снизу колонны 14 по линии 11 выводят поток, содержащий преимущественно метанол.
Примеры 1-4 показывают реализацию настоящего изобретения по способу получения диметилового эфира, путем контактирования его с дегидратирующими катализаторами с использованием различных вариантов загрузки в реакционную зону молекулярных сит цеолитного типа с крупными порами, выбранных из группы, состоящей из цеолитов структуры FAU, являющихся цеолитами типа X.
Пример 1. Данный пример иллюстрирует реализацию по способу получения диметилового эфира с применением в качестве катализатора молекулярного сита цеолитного типа с крупными порами, выбранного из группы, состоящей из цеолитов структуры FAU, являющееся цеолитом NaX.
Способ получения ДМЭ реализован на установке см.чертеж.
Согласно схемы установки на чертеже метанол в количестве 463,3 кг/ч поступает по линии 1. Его смешивают с рециркулируемым метанольным потоком 11, поступающим из куба колонны 14, подогревают в теплообменнике преимущественно до температуры 310°C и по лини 2 направляют в реакционную зону реактора 12, содержащую цеолит типа NaX, размер гранул 1,8÷2,2 мм, в количестве 0,5 м3. Реактор представляет собой аппарат адиабатического типа. Реакция дегидратации осуществляется при температуре 300°C и давлении 2,0 МПа. Конверсия метанола за проход 90%. Из реакционной зоны по линии 3 выводят реакционную смесь. Реакционную смесь из реактора 12 в количестве 1000 кг/ч подают в ректификационную колонну 13 по линии 3. Поток 3 содержит 32,31% ДМЭ; 53,67% метанола и 14,02% воды. Процесс ректификации осуществляют при абсолютном давлении в кубе колонны 13 равном 0,37 МПа, верха колонны 13 равном 0,32 МПа. Температуры: куба - 140°C; тарелки питания - 55°C; верха - 40°C.
Сверху ректификационной колонны 13 по линии 5 выводят паровой поток, содержащий ДМЭ и метанол. Далее поток охлаждается в конденсаторе дефлегматоре и поступает в колонну 14, по линии 7 выводится 859,8 кг/ч продукта, содержащего 37,60% ДМЭ и 62,40% метанола. Часть сконденсированного потока по линии 6 возвращают в колонну 13 в виде флегмы. Снизу колонны 13 по линии 4 выводится поток, содержащий преимущественно воду в количестве 140,2 кг/ч. Ректификационная колонна 14 предназначена для разделения ДМЭ от метанола. Сверху ректификационной колонны 14 по линии 8 выводится паровой поток, содержащий ДМЭ. Далее поток охлаждается в конденсаторе дефлегматоре и поступает по линии 10 на склад в количестве 323,1 кг/ч. Часть сконденсированного потока по линии 9 возвращается в колонну 14 в виде флегмы. Снизу колонну 14 по линии 11 выводится поток, содержащий преимущественно метанол в количестве 536,7 кг/ч.
Пример 2. Данный пример иллюстрирует реализацию по способу получения диметилового эфира аналогично примеру 1, отличающемуся тем, что в качестве катализатора применяют молекулярное сито цеолитного типа с крупными порами, выбранное из группы, состоящей из цеолитов структуры FAU, являющееся цеолитом НХ.
Пример 3. Данный пример иллюстрирует реализацию по способу получения диметилового эфира аналогично примеру 1, отличающийся тем, что в качестве катализатора применяют молекулярное сито цеолитного типа с крупными порами, выбранное из группы, состоящей из цеолитов структуры FAU, являющихся цеолитом LiX.
Пример 4. Данный пример иллюстрирует реализацию по способу получения диметилового эфира аналогично примеру 1, отличающемуся тем, что в качестве катализатора применяют молекулярное сито цеолитного типа с крупными порами, выбранное из группы, состоящей из цеолитов структуры FAU, являющихся цеолитом HLiX.
Показатели качества полученных диметиловых эфиров приведены в таблице 1.
Достигаемый технический результат
Преимуществом заявляемой установки перед прототипом являются:
- получение ДМЭ высокой концентрации 99,99% и выше без постороннего запаха, что позволит его использовать в качестве газа вытеснителя аэрозольных упаковок;
- получение ДМЭ высокого качества с низким содержанием воды до 0,0001%;
- получение ДМЭ с низким содержанием сернистых соединений до 0,0001%;
- предложен катализатор дегидратации метанола в виде молекулярных сит цеолитного типа с крупными порами, выбранных из группы, состоящей из цеолитов структуры FAU, являющихся цеолитами типа X и их модификациями, который позволил увеличить конверсию ДМЭ до 90% и выше.
Формула изобретения
Способ получения диметилового эфира из метанола, путем его контактирования с дегидратирующим катализатором в реакционной зоне и разделении компонентов реакционной смеси с помощью ректификации с возвращением непрореагировавшего метанола в реакционную зону, при котором дегидратацию метанола и образование эфира проводят в присутствии катализатора при повышенной температуре, отличающийся тем, что в качестве катализатора применяют молекулярные сита цеолитного типа с крупными порами, выбранные из группы, состоящей из цеолитов структуры FAU, являющихся цеолитами типа X и их модификациями, дегидратацию осуществляют в газообразном состоянии при температуре в реакционной зоне 280÷330°C и давлении 17÷22 атм, в первой ректификационной колонне отгоняют от воды фракцию, состоящую из метанола и диметилового эфира, во второй ректификационной колонне отгоняют от непрореагировавшего метанола диметиловый эфир и возвращают метанол в реакционную зону.
bankpatentov.ru
- В эфире ню
- Эфир т сайт
- Ню в эфире
- Пятая стихия эфир
- Аригус прямой эфир
- Лдпр прямой эфир
- Ультра радио эфир
- Слиться с эфиром
- Энергия генератора эфира
- Прямой эфир проклова
- Прямой эфир зтв